
Glyn Dennehy, President Europe of TTI IP&E - Europe
Interconnect, Passive and Electromechanical (IP&E) products are used in every electronic or electrical vehicle system.
These include body electronics applications such as lights, ECUs, safety and lighting systems, advanced driver assistance systems, infotainment, and antenna systems.
They are also found in high voltage powertrain systems such as battery packs, inverters and electric motors used in the latest electric and fuel cell vehicles.
To support this market need, Global TTI IP&E, which operates out of more than 136 locations worldwide, an authorized specialty distributor of IP&E components and discrete semiconductors, is strengthening its technical support capability to facilitate the transport sector’s transition to connected, electric and hybrid vehicles.
Enhancing this technical resource is a global logistics infrastructure of 13 major distribution centers covering over three million square feet and over eight thousand employees.
Automotive Industries (AI) asked Glyn Dennehy, President Europe of TTI IP&E – Europe, what are the main trends in IP&E components.
Dennehy: The automotive industry is driving a very significant increase in component use as it transitions to electric vehicles because every electric vehicle includes new electronic automotive applications, like battery packs, electric motors and inverter systems that are not found in traditional vehicles.
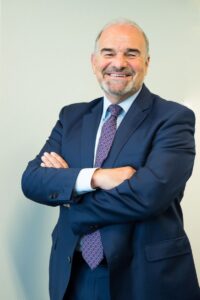
So, there is an incremental growth in component volumes.
As the complexity of automotive and vehicle electronics grows through the increased use of semiconductor devices, the number of passive type of components required increases significantly by a multiple of five to 10 per semiconductor.
AI: Which means increased complexity in terms of IP&E components?
Dennehy: To understand the complexity, just look at internal connectivity, which includes anything from standard wire to wire, wire to board, PCB type applications through to the plastic and metal types of input and output connectors, and the more rugged and high voltage connectors and cable assemblies and harnesses used in electric vehicles.
Similarly, the rise in the use of advanced driver assistance systems on vehicles means there are more and more sensors being included in every single part of the automobile.
The volumes of these passive parts being used by the automotive, commercial, and electric vehicle markets is so large that components such as capacitors and resistors are seen as commodities.
But other products, like inductors or circuit protection, which are typically PCB applications, and high power and automotive grade MLCC capacitors, are specifically designed for transportation and automotive applications.
These are the product sets where TTI IP&E – Europe is focused as a specialist distributor. Some 90% of TTI business is supplying these components.
AI: What about advances in the connectivity of internal combustion engine powered vehicles?
Dennehy: Good question because it is still not certain which technology is going to prevail.
There is increasing talk about hydrogen cells and a number of other propulsion systems.
Those still include petrol and diesel. We see a number of countries pushing out the deadlines for the total phasing out of internal combustion engines.
So, that technology is going to be with us for a long time.
In fact, the automotive sector drove significant increases in electronic component consumption for many years before the focus on electric vehicles. Even before there was any thought of electric vehicles, digital dials and computer screens started replacing mechanical dials.
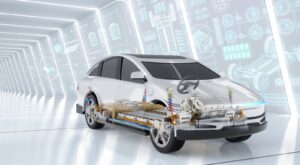
Vehicles are now wirelessly connected internally as well as externally, regardless of the vehicle powertrain. In addition, there are many new vehicle safety solutions which have increased the complexity of the electronics inside all vehicles and not just passenger cars.
AI: How does this influence the latest IP&E technological trends?
Dennehy: A major trend in IP&E components has always been product miniaturization, such as smaller fine pitch PCB connectors or capacitors and smaller component case sizes. These smaller components must now handle higher speed data, which has resulted in new generations of FAKRA or Ethernet connectors, EMI filters and inductors for infotainment and camera systems.
Many new components are being introduced by connector, sensor, and passive component suppliers to support the higher frequencies required in these systems.
Another key trend is the high voltage systems operating at 400V, 800V and 1000V required in electric and fuel-cell vehicles.
Manufacturers have been driven to develop new high voltage solutions like MOSFETs, contactors and connector systems for the powertrain of these electric vehicles.
And we are not talking just about the vehicle itself. Similar technologies are needed in the charging stations that are required to power these new vehicles.
AI: Is copper still the material of choice?
Dennehy: For high-speed data connectivity applications, the copper-based connector systems, like FAKRA, HSD, and other ethernet type connector products found in vehicles, are capable of handling speeds that are beyond what is required at present.
It is therefore not expected that the industry will need to move to fiber optic technology used in the aerospace and telecom industries. In some applications however, wireless technology will probably replace some of the wiring in the car.

For electric and hybrid vehicles, where the vehicle powertrain requires thick copper high voltage cables, every gram per centimeter of wiring counts, so vehicle manufacturers are investigating the use of lighter aluminum cables and connector manufacturers are introducing new connector systems capable of supporting either cable type.
AI: What are the main challenges in the automotive sector?
Dennehy: The biggest challenge is the pace of change.
The number of design and development activities that are ongoing in the automotive sector is quite extraordinary.
It is not just from the established original equipment manufacturers and traditional tier suppliers; it is a plethora of new startup companies in the electric vehicle sector.
These are a very different types of business to the established motor companies, and some are making real inroads into the market.
For companies like TTI IP&E, the challenge is to ensure we have engineers available who can help both the older companies and the new entrants to select the right products from the start.
They have to be knowledgeable both technically and commercially.
One can design a product that seems to be the perfect fit from an engineering perspective, but it must also be suitable for scaling and commercialization.
As the distributor for a range of manufacturers, we can advise on the right supply chain solution, which is the best component at the optimum cost and the right level of support that is required beyond the design stage.
AI: How important is logistics?
Dennehy: The solution we offer moves from the design side right through the chain to production, which is where we provide a distribution solution that is much more than warehousing and delivery.
A single electronic PCB may have hundreds of parts in its bill of materials.
The challenge is to control the supply of components from the design cycle through pre-production and into production while dealing with numerous suppliers in different parts of the world.
To do that, we have the systems needed to forecast demand and ensure that there is a stockpile of components to meet the needs of our customers in all stages of the development cycle.
In terms of systems, many of the components we supply are low-cost devices that sell in extremely high volume.
So, we must ensure that we can handle large volumes of parts profitably, and the only way to do that is to touch them as few times as possible.
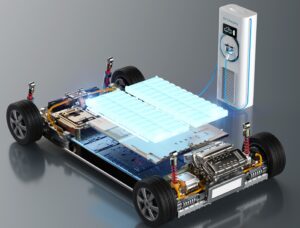
For that, we have very well-developed systems of procurement from manufacturers to make sure the materials are on our shelves well before the customers need them, and that we have the right processes and logistics solutions to deliver to the customer on time.
These logistics solutions have been developed over time for a wide range of industries, and well before there was a need for automotive electronics.
The solutions include everything from supply chain programs specifically designed to customer requirements, right through to the hardware we use in our warehouses, such as automated picking, and robotic shuttle systems.
So, it is a sophisticated distribution center rather than a warehouse.
AI: Please give us an example of the support you provide.
Dennehy: We have been supplying passive components into electronic applications for many years.
When it comes to automotive or transportation customers, we supply the same logistics solutions.
It is just the technologies which are changing; a development which has arisen with the arrival of new entrants in the market.
For example, we are working with a customer who is a startup from outside of the main automotive manufacturing hubs.
They are involved in designing a new brand and range of buses and light commercial vehicles from the design concept stage. We are working with them at all stages of the design, including their battery systems, their high voltage cabling, and the charging system.
Simultaneously, we are building up inventory stock of components and assemblies to provide ongoing support.
Furthermore, to meet the needs of the automotive sector, we have acquired the UK automotive harness wiring manufacturer and distributor Raffenday that specializes in the design of harnesses for transportation. This purchase gives us the capability to work with a customer on small volume prototype applications.
This allows us to be even more quick and flexible and to respond to our customers’ needs – no matter whether they are large companies or small startups – with speed and agility.
We can now design the full harness and cable systems, whilst providing and stocking the various parts and components required when they are ready to take their vehicle to market.
AI: Looking ahead, where is TTI IP&E – Europe focused?
Dennehy: We will continue to focus on transportation, along with the aerospace and defense industries, as there are synergies: the aerospace and defense forces are investigating the use of electrification technology in their new airplanes and military vehicles.
We will not lose our focus on fulfilment, because nothing gets made unless the parts are available.

That expertise will be balanced by being able to provide more engineering support.
We are adding more technical competence so that we can support engineers and design programs from an earlier stage of development than we have been able to before.
That includes using our sister company, Mouser Electronics, which is already talking to the engineers and providing them overnight with one or two components needed for a prototype.
We can work with the customers to ensure that they have the necessary inventory on hand as they scale.
At the same time, we will strengthen our links with our suppliers. We work with a very focused group of manufacturers to ensure that we can continue to provide high levels of service, rather than providing an ok service because we are working with hundreds of suppliers.
For more information on the services TTI IP&E – Europe provides, please visit the website www.ttieurope.com
More Stories
MESSRING completes new crash test facility for Mahindra in India
ROHM Develops an Ultra-Compact MOSFET Featuring Industry-Leading* Low ON-Resistance Ideal for Fast Charging Applications
More than 30 of the top 50 global suppliers have production facilities in Turkey