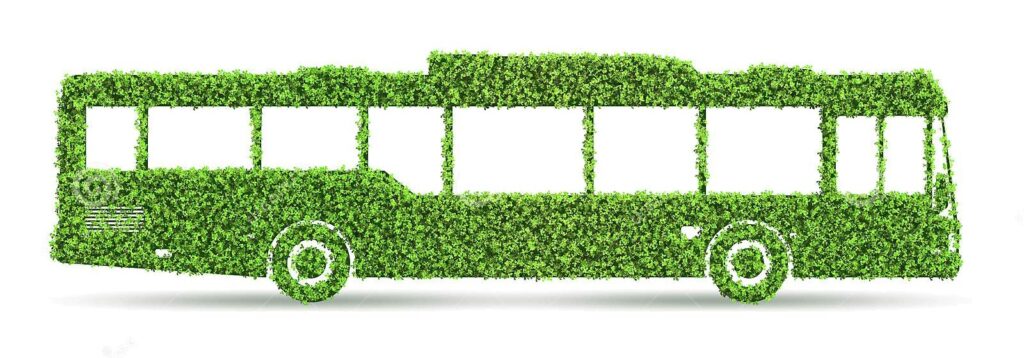
In today’s fast-paced manufacturing world, sustainability isn’t just a buzzword—it’s a necessity. As industries strive to keep up with demand, the pressure to minimize waste and cut down on energy consumption is more intense than ever.
But what if there were ways to not only meet these challenges but to turn them into opportunities? Embracing greener manufacturing practices can not only benefit the environment. They can also enhance your operational efficiency and bottom line.
So, are you ready to achieve a more sustainable manufacturing process? Here are some practical strategies that make a real difference.
1. Waste Reduction Strategies
Reducing waste is the foundation of greener manufacturing. Here’s how you can tackle it:
● Lean Manufacturing
Lean manufacturing focuses on maximizing value while minimizing waste. By streamlining processes, you reduce unnecessary steps and materials. This leads to cost savings and less waste. Lean principles, like continuous improvement and value stream mapping, help find and fix inefficiencies.
● Process Optimization
Optimizing your manufacturing processes can significantly reduce waste and enhance efficiency. One effective way to do this is by upgrading machinery and equipment. For instance, using high-quality ball bearings can make a big difference.
These seemingly simple components reduce friction in machinery. This ability can lead to less energy consumption and longer equipment life. This efficiency helps minimize waste by ensuring that machines run smoothly and last longer.
● Recycling and Reuse
Recycling materials in this process can drastically cut down on waste. Many materials, such as metals and plastics, can be reused or recycled rather than discarded.
Implementing a robust recycling program helps the environment and can lead to cost savings. For instance, companies that recycle scrap metal often see reduced material costs and less landfill use.
2. Energy Consumption Reduction Strategies
Power is a major cost and environmental concern in manufacturing. Here’s how to cut down on its use:
● Energy-efficient Equipment
Investing in energy-efficient equipment can lead to substantial savings. Modern machinery is designed to use less power while performing the same tasks. For example, energy-efficient motors and lighting systems consume less power.
These reduce both costs and environmental impact. Upgrading to such equipment often pays off quickly through lower energy bills and reduced carbon footprint.
● Renewable Energy Sources
Including renewable power sources, such as solar or wind power, can greatly reduce your reliance on fossil fuels. Using renewable energy in your operations cuts costs and helps the environment.
● Energy Management Systems
Energy Management Systems (EMS) are essential for tracking and optimizing energy use. These methods monitor power consumption in real time. They identify areas for improvement and suggest actions to enhance efficiency.
By implementing an EMS, you can make data-driven decisions to reduce energy waste and improve overall use.
3. Implementing Sustainable Practices
Turning strategies into practice is key to achieving greener manufacturing. Here’s how to make it happen:
● Employee Training and Engagement
Getting your team on board with sustainability goals is crucial. Training programs on waste reduction and power conservation can empower them to help achieve these goals. Engaging staff through workshops and incentives ensures everyone is aligned with your sustainability objectives.
● Monitoring and Reporting
Regular monitoring and reporting help track progress and identify areas for improvement. Measuring waste and power use with tools gives insights into your operations. Transparent reporting aids internal assessments and builds stakeholder trust. It shows your commitment to sustainability.
● Setting Goals and Benchmarks
Establishing clear, measurable goals for waste reduction and power efficiency is essential. Setting benchmarks allows you to track progress and make adjustments as needed.
For example, you might aim to reduce waste by 20% over the next year or cut power consumption by 15%. These goals provide direction and motivation for continuous improvement.
4. Challenges and Solutions
Implementing greener practices isn’t without its challenges. Common obstacles include high initial costs and resistance to change. However, these challenges can be overcome with thoughtful planning and strategy.
Solutions include:
- Phased Implementation: Gradually introducing changes can ease the transition and spread out costs.
- Employee Involvement: Engaging employees can help overcome resistance. It can also build support for new practices.
- Financial Incentives: Grants or incentives for greener practices can offset initial costs. They can make investments more manageable.
5. Future Trends in Green Manufacturing
Manufacturing’s future is increasingly green. New technologies and practices are shaping the industry. Trends include advanced recycling, smart production, and more renewable energy use.
To stay ahead:
- Keep Abreast of Innovations: Stay updated on new technologies and practices that can enhance sustainability.
- Invest in Research and Development: Innovating within your processes can lead to new ways to reduce waste and power consumption.
Conclusion
Greener manufacturing helps both the environment and your business. You can save money and boost efficiency by cutting waste and using energy better.
The above strategies are a roadmap. They can create a more sustainable manufacturing process. The long-term benefits—both environmental and economic—are well worth the effort.
More Stories
Best Wheel Size for Off-Road Adventures: What People Get Wrong
Trusted Auto Collision Repair That Restores Both Performance and Peace of Mind
What You Need to Know About Tire Pressure in Winter vs Summer