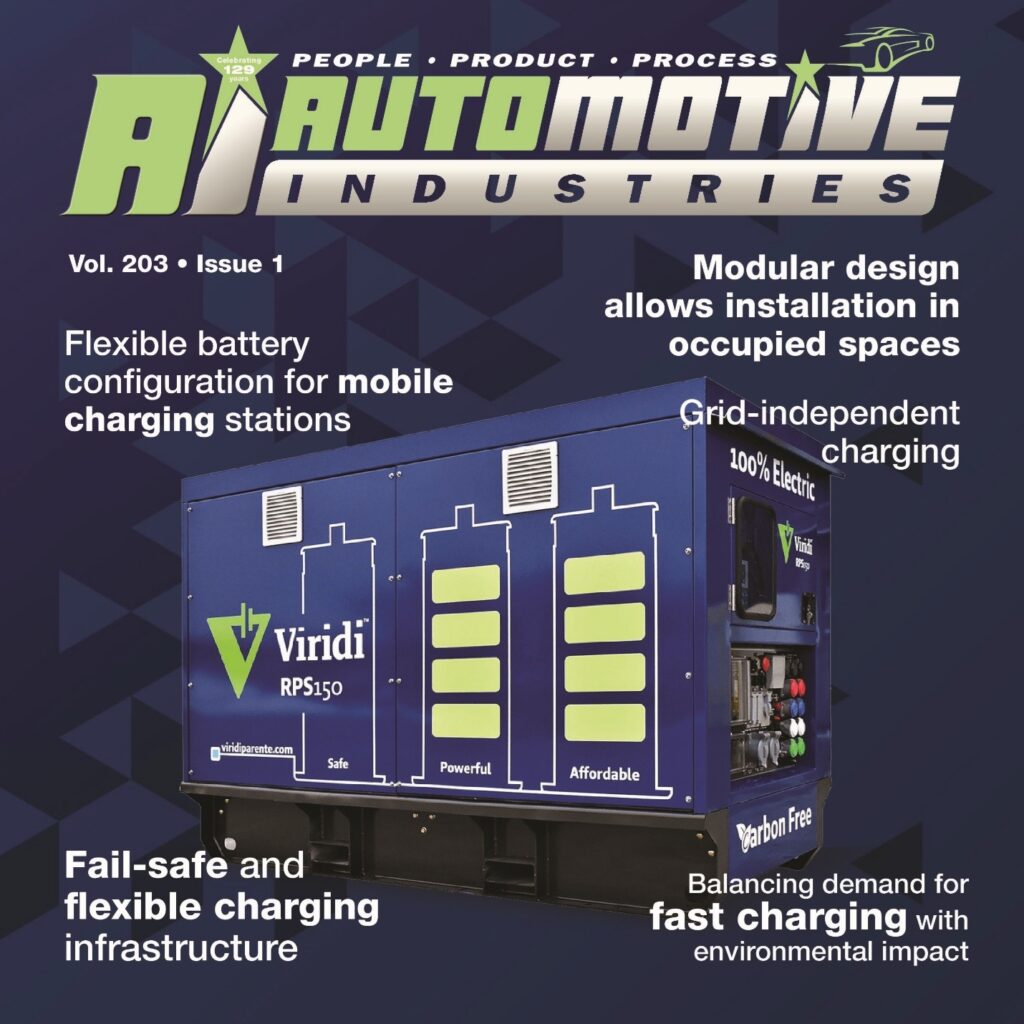
In the fast-evolving world of energy storage, safety, reliability, and sustainability are paramount. Viridi, under the leadership of Jon M. Williams, has emerged as a trailblazer in fail-safe battery technology. With innovations like anti-propagation systems, advanced automation, and a commitment to sustainability, Viridi is reshaping the energy landscape.
In this exclusive interview with Automotive Industries, Jon M. Williams shares insights into Viridi’s technological advancements, the challenges and opportunities of onshoring, and the transformative role of energy storage across industries. From scaling production to addressing the needs of automotive dealerships and fleet markets, Viridi’s journey exemplifies how innovation can drive progress while prioritizing safety and sustainability.
Automotive Industries: Hi Jon, what inspired Viridi to pursue fail-safe battery technology, and how has the technology evolved since the company was first established?
Jon M. Williams: Our inspiration for fail-safe battery technology stems from a commitment to safety and reliability. Early on, we recognized that energy storage systems needed to address not only performance but also critical safety concerns. Since our inception, we’ve focused on anti-propagation technology, ensuring that if one cell fails, it doesn’t compromise the entire system. Over the years, our technology has evolved through rigorous testing, enhanced automation, and continuous innovation, enabling us to deliver industry-leading safety and durability standards.
Automotive Industries: Can you tell us more about the recent automation line installation and its impact on scaling the production of 50kWh pack systems?
Jon M. Williams: The new automation line marks a significant milestone in our production capabilities. By integrating advanced robotics and precision engineering, we’ve streamlined the assembly process, allowing us to scale production efficiently while upholding the highest quality standards. This line enables us to produce our 50kWh pack systems at scale, addressing the growing demand for safe, reliable energy storage solutions across multiple industries.
Automotive Industries: With the onshoring of module manufacturing to Buffalo, what challenges and opportunities has Viridi encountered during this transition?
Jon M. Williams: Onshoring has presented both challenges and opportunities. While we had to navigate the complexities of supply chain realignment and workforce development, it has enabled us to reduce lead times, improve quality control, and support the local economy. Additionally, it aligns with our sustainability goals by significantly reducing emissions associated with overseas shipping. This transition has strengthened our ability to deliver innovative products more efficiently and sustainably.
Automotive Industries: The new smart lines can produce over 9,000 packs annually, significantly reducing production time to just 20 minutes per pack. How has this transformative technology impacted Viridi’s competitiveness in the market?
Jon M. Williams: Smart lines are a game-changer for Viridi. By reducing production time and increasing output, we’ve improved our ability to meet market demand quickly and cost-effectively. This efficiency not only reduces production costs but also allows us to offer competitive pricing without sacrificing quality. It’s a critical factor in maintaining our leadership in the energy storage market.
Automotive Industries: Safety has been a major focus in your manufacturing process. How do the new automated systems, such as cell tap stations and safety devices, contribute to both operator safety and product quality?
Jon M. Williams: Safety is at the core of everything we do. Our automated systems, including cell tap stations and integrated safety devices, minimize human error while ensuring consistent quality. These systems are designed to protect operators by automating potentially hazardous tasks and maintaining strict safety protocols. Additionally, the enhanced precision of these systems ensures that each pack meets our rigorous safety and performance standards.
Automotive Industries: The integration of automated cell sorting and traceability for all modules within the RPS50 pack system ensures quality. How does this approach align with Viridi’s commitment to delivering reliable and durable products?
Jon M. Williams: Automated cell sorting and full traceability are vital to delivering products our customers can trust. By ensuring that every cell meets our specifications and is traceable throughout its lifecycle, we maintain unparalleled quality control. This approach enhances reliability while providing valuable insights for continuous improvement and long-term customer support.
Automotive Industries: Onshoring has reportedly saved 60 containers’ worth of overseas production. What role does sustainability play in your manufacturing processes and overall strategy?
Jon M. Williams: Every decision we make is guided by the goal of creating a more sustainable future. Onshoring has significantly reduced the carbon footprint associated with shipping and logistics. Beyond that, we’re committed to minimizing environmental impact through efficient resource utilization, optimizing energy use in our facilities, and designing products that prioritize longevity and recyclability.
Automotive Industries: With a 10-year product life and 3,500-cycle capacity, how does Viridi’s anti-propagation Li-ion battery system address the evolving needs of the automotive dealerships and fleet market?
Jon M. Williams: Battery energy storage systems (BESS) are poised to play a critical role in the automotive and fleet industries. EV sales are rising rapidly, and charging these vehicles—especially with fast chargers—places enormous new loads on the grid. BESS solutions help dealerships and fleet managers manage energy costs, reduce peak demand, and create charging infrastructure in areas with insufficient electrical supply. By participating in grid support programs like virtual power plants, they can also generate financial returns while contributing to grid stability.
Automotive Industries: As energy storage solutions gain traction, how do you envision Viridi’s technology influencing other industries in the future?
Jon M. Williams: Energy storage is a transformative technology with impact that extends far beyond traditional applications. Viridi has powered a remote mountain race, a music festival in the desert, the nation’s largest sporting event, and provided resiliency for telecom towers. From critical infrastructure to unique and challenging environments, our solutions showcase the versatility of energy storage in addressing complex, industry-specific needs.
Conclusion
Viridi’s journey underscores the importance of innovation, safety, and sustainability in energy storage. Under Jon M. Williams’ leadership, the company continues to push boundaries, addressing the unique challenges of various industries while contributing to a more sustainable future. As the demand for reliable energy solutions grows, Viridi is well-positioned to lead the charge in powering a cleaner, safer world.
More Stories
Towing Services Explained: 6 Key Facts You Need to Know
Environmental Factors That Influence Ceramic Coating Choices
Professional vs. DIY Tinting: What You Should Know