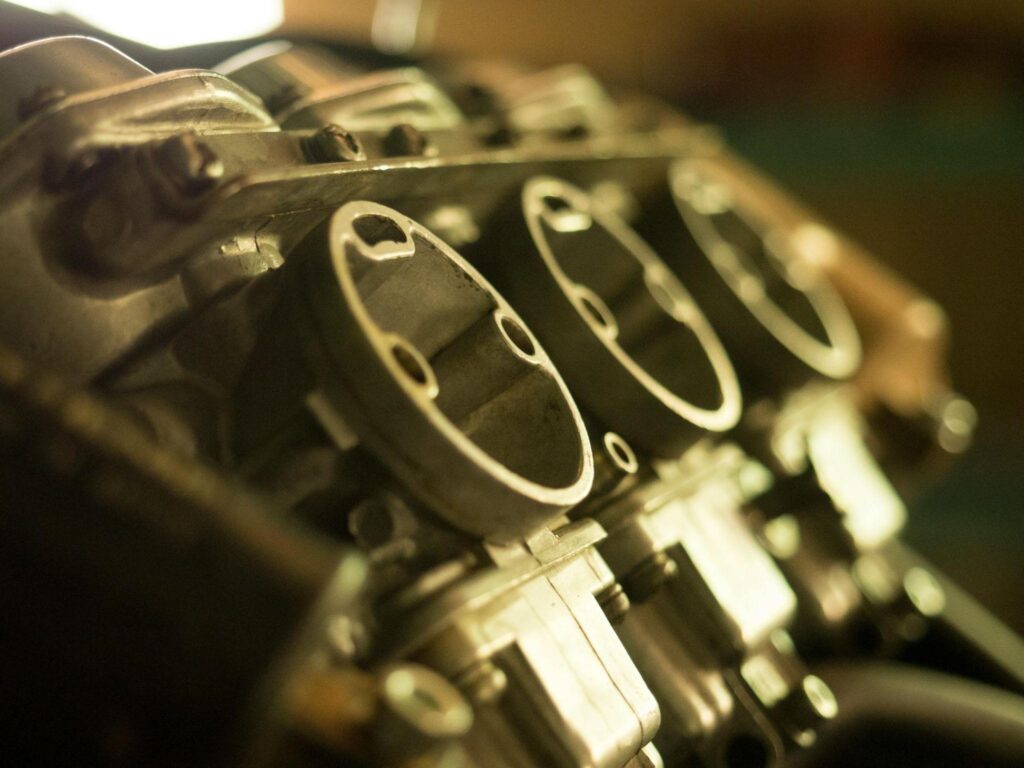
The automotive industry has long relied on cutting-edge technologies to shape and refine components with precision and efficiency. As manufacturing evolves, so do the tools used to cut metals and other materials. Traditional cutting methods have given way to advanced technologies such as laser cutting, waterjet cutting, and plasma cutting, each offering unique benefits. With the increasing demand for speed, accuracy, and cost-effectiveness, choosing the right cutting technology has become crucial for manufacturers aiming to stay competitive.
What Are the Main Cutting Technologies Used in Auto Production?
Cutting processes in the automotive sector have evolved significantly, transitioning from mechanical techniques to more sophisticated methods that enhance precision, reduce material waste, and improve production speed. Each method plays a specific role in automotive manufacturing, influencing factors such as efficiency, cost, and environmental impact.
Laser Cutting
Laser cutting is a high-precision process that uses a focused laser beam to cut through metal sheets and other materials. It is widely used in the automotive industry for its ability to create intricate designs with minimal material wastage.
Waterjet Cutting
Waterjet cutting involves the use of a high-pressure stream of water, sometimes mixed with abrasive particles, to cut through various materials. This method is known for its versatility and ability to cut materials without generating heat, making it ideal for applications where heat distortion is a concern. Leading manufacturers like TECHNI waterjets offer advanced waterjet cutting systems that enhance precision and efficiency across various industries.
Plasma Cutting
Plasma cutting uses an electrically conductive gas to generate a plasma arc that melts and removes material from the workpiece. It is commonly used for cutting thick metals and is preferred for its speed and efficiency in heavy-duty applications.
Mechanical Cutting (Shearing, Milling, Sawing)
Mechanical cutting methods, such as shearing, milling, and sawing, remain relevant for certain applications that require durability and reliability. These processes are often combined with automated systems to enhance precision and repeatability.
Hybrid and Emerging Cutting Technologies
New cutting technologies are continuously emerging, combining the strengths of existing methods. Hybrid cutting systems integrate multiple techniques, such as laser and plasma, to optimize performance and expand the range of materials that can be processed.
How Does Laser Cutting Work in Automotive Manufacturing?
Laser cutting is a process that uses a high-powered laser beam to melt, burn, or vaporize material. It is widely used in automotive production for cutting metal sheets, precision components, and even body panels. The process offers superior precision, minimal material waste, and high-speed operation. Understanding factors like laser intensity and heat levels is crucial, as explored in How Hot Is a Laser Cutter, which explains the temperatures involved in different laser cutting applications.
What Are the Different Types of Laser Cutters Used in Auto Manufacturing?
Various laser cutting systems are used in the automotive industry, each offering distinct advantages depending on the material and application.
Fiber Laser Cutters
Fiber lasers use a solid-state laser source to generate a high-intensity beam. They are highly efficient for cutting metals like steel and aluminum due to their precision and energy efficiency.
CO₂ Laser Cutters
CO₂ lasers use a gas mixture to produce the laser beam. These cutters are effective for non-metallic materials and some thin metals but are less efficient than fiber lasers for automotive applications.
Nd: YAG Laser Cutters
Nd: YAG (neodymium-doped yttrium aluminum garnet) lasers offer high power and are commonly used for deep penetration welding and cutting applications in the automotive industry.
What Are the Main Components of an Automotive Laser Cutter?
- Laser Source – Generates the laser beam
- Beam Delivery System – Directs the laser beam to the cutting head
- Cutting Head – Houses the focusing lens and nozzle
- Assist Gas System – Uses gases like oxygen or nitrogen to enhance cutting efficiency
- CNC Controller – Controls the movement and parameters of the cutting process
- Cooling System – Prevents overheating of the laser components
What Are the Key Parameters in Laser Cutting for Auto Production?
- Laser Power (kW)
- Cutting Speed (m/min)
- Focal Length
- Assist Gas Type and Pressure
- Material Thickness
- Beam Quality
What Are the Cutting Tolerances for Laser Cutting in Automotive Applications?
- Kerf Width: Typically 0.1 – 0.4 mm
- Dimensional Tolerance: ±0.05 mm
- Positioning Accuracy: ±0.03 mm
What Is the Thickest Metal That Can Be Laser Cut in Auto Production?
- Mild Steel: Up to 25 mm (1 inch)
- Stainless Steel: Up to 20 mm (0.8 inches)
- Aluminum: Up to 15 mm (0.6 inches)
How Does Waterjet Cutting Compare to Laser Cutting in Auto Production?
Waterjet cutting is an alternative to laser cutting that provides unique advantages, particularly when dealing with heat-sensitive materials.
What Are the Main Parts of a Waterjet Cutting System?
- High-Pressure Pump – Generates the required water pressure
- Nozzle and Mixing Chamber – Directs and accelerates the water stream
- Abrasive Hopper – Feeds abrasive particles for cutting hard materials
- CNC Control System – Guides the cutting path
What Are the Advantages of Using Waterjet Cutting in Automotive Applications?
- No heat-affected zone (HAZ)
- Can cut virtually any material
- No mechanical stress on the workpiece
- Minimal kerf width for precise cutting
What Are the Limitations of Waterjet Cutting Compared to Laser Cutting?
- Slower cutting speed
- Higher operational costs due to water and abrasive consumption
- Less effective for high-precision metal cutting
Conclusion
As automotive manufacturing continues to advance, the choice between laser and waterjet cutting depends on factors such as material type, required precision, and cost considerations. While laser cutting offers unmatched speed and accuracy, waterjet cutting provides versatility and the ability to cut materials without heat distortion. By understanding the strengths and limitations of each method, manufacturers can optimize their cutting processes and drive efficiency in auto production.
Future advancements in cutting technologies, such as AI-driven automation and hybrid systems, will further enhance efficiency and precision in automotive manufacturing. Companies must stay informed about these developments to maintain a competitive edge in the industry.
More Stories
Sonatus – The industry is shifting gears to software
Cybord warns of dangers of the stability illusion
HERE building trust in ADAS systems