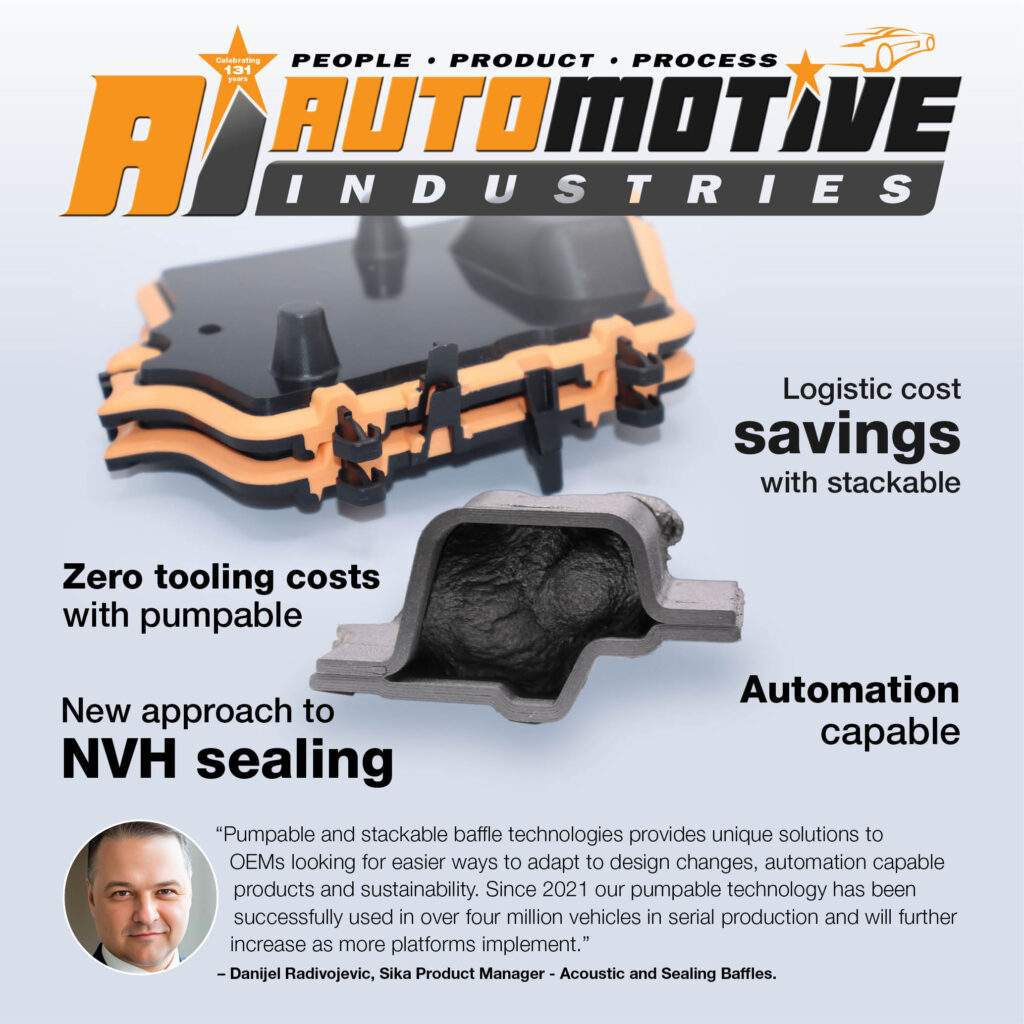
Minimizing noise and vibration levels inside the vehicle is key to achieving higher levels of passenger comfort and differentiating models and marques. At the same time OEMs are under relentless pressure to reduce costs.
Automotive Industries (AI) asked Danijel Radivojevic, Sika Product Manager – Acoustic and Sealing Baffles, how the company’s pumpable baffle system helps reduce costs.
Radivojevic: Car designs are drastically changing to reduce weight and costs where possible. Sika is seeing cavities in vehicle design become more and more tight with each new platform, making parts and tapes difficult and sometimes impossible to apply.
A highly expandable pumpable baffle system solves this issue as it can be applied with robotics. This helps customers build lighter, gree
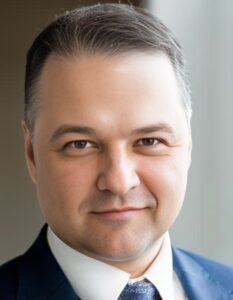
ner, stronger and quieter vehicles.
The pumpable system changes the traditional NVH cavity sealing solutions, where baffles usually are either injection molded parts or extruded tapes.
Pumpable baffle technology enables a completely new approach as OEMs can easily adapt to design changes at a late stage without the need to redesign the baffle part.
It’s a truly innovative, one-component, heat-reactive and high expandable cavity filler.
It is also worth noting that our highly expandable pumpable baffle was recently given an award status as a finalist for the 2025 PACE Awards presented by Automotive News. The significance of this finalist award status for Sika Automotive is the recognition within the automotive supplier industry as an innovation.
AI: Does the new pumpable baffle technology reduce tooling costs?
Radivojevic: Significantly, there are no associated tooling costs whatsoever with a pumpable system. When compared to standard parts for small cavities, a tool can cost more than $250,000 and extrusion dyes cost $20,000+.
In fact, this one component product can utilize standard adhesive pumping equipment that is already used on most OEM production lines.
The pumpable baffle also eliminates the need for additional tools for components that differ by model variant, such as sedans, station wagons, or hatchbacks. Reducing the number of components also contributes to lower logistical demands, both in administration and in transportation.
AI: What trends is Sika seeing with OEM customers in terms of car design?
Radivojevic: OEMs are starting to rethink body-in-white design and pumpable baffles will become a necessity to fill these smaller cavities where traditional baffles and tapes cannot be implemented anymore be humans or robots.
As mentioned earlier, it is allowing vehicle body design creativity within the OEMs to be expanded on future platforms while helping to reduce costs and increase production efficiency.
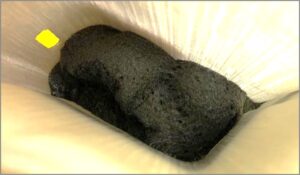
OEMs have already begun modifying their body designs to facilitate pumpable baffle applications.
AI: When will the first vehicles (have the first vehicles) roll off the assembly line using the technology?
Radivojevic: Sika started to develop the pumpable baffle more than a decade ago. Soon after we started, a major OEM saw immense potential in this technology and implemented Sika’s pumpable baffle technology over the next years in serial production.
Since 2021 our technology has been successfully used in over four million vehicles in serial production and will further increase as more platforms implement.
AI: Does the technology support the trend towards automation?
Radivojevic: Most definitely, the pumpable baffle system is designed just for that. OEMs are looking to reduce costs, and automation will play a key role in doing so. We designed this pumpable system to work with current robotic pumping equipment that any OEM has on the production line where adhesives are used.
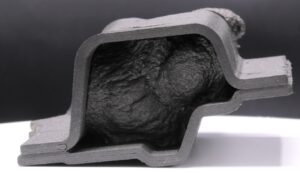
Our stackable baffle system was also designed with automation in mind, as robots can be programmed to grab and place in the selective cavity areas of the vehicle body.
With stackable baffles being optimized for packaging efficiency, programming robotics is just matter of trial to pick and place correctly each time. Thus, it increases efficiency on the production line.
The good news is that both innovations can be used together. This combination is enabling the sealing of large and complex cavities completely by robotic application.
AI: What is a stackable baffle?
Radivojevic: This may sound quite simple, but a baffle you can stack. When we see traditional baffles, they come in all different shapes and sizes which makes it quite difficult with packaging, and they normally just placed into boxes.
Sika has developed special design features to enable stacking and automated application of baffle parts.
AI: What are the other benefits of using a stackable baffle?
Radivojevic: There are two major benefits: Automated application and reduced logistic resources through the possibility of denser packaged parts.
The automated application enables baffle parts to reach repeatable assembling quality, enabling monitoring and tracking as well as fine tuning the clips used in the application process when applying occurs.
The stacked packaging increases the packaging density which thus requires less boxes and lower logistic costs to move the same number of products to the assembly line.
AI: Where are the savings in logistics costs when using a stackable baffle?
Radivojevic: This will be highly dependent on volume and the part design being used currently. For example, with a current OEM customer of ours, traditional bulk parts fit 41 parts per box on average, while moving to a stackable baffle configuration increased this to 84 parts per box (over a 2x increase).
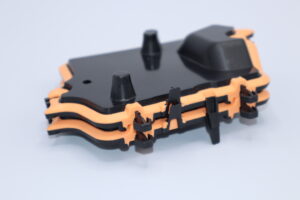
This led to logistic cost savings of 40%.
AI: How does Sika support OEMs wanting to benefit from stackable baffles?
Radivojevic: We can help the customer in design, engineering, prototype builds, and serial production; all in-house under one organization.
We don’t see it as just a supplier to customer relationship, but rather a partner in both trust and development collaboration to achieve goals. Supported by a strong collaboration with our customers. This innovation is already in serial production for several OEMs.
More Stories
K-ALLIANCE: MESSE DÜSSELDORF’S GLOBAL PLASTICS AND RUBBER PORTFILIO UNDER NEW UMBRELLA BRAND
Power Integrations Names Jennifer Lloyd as Its Next CEO
Towing Services Explained: 6 Key Facts You Need to Know