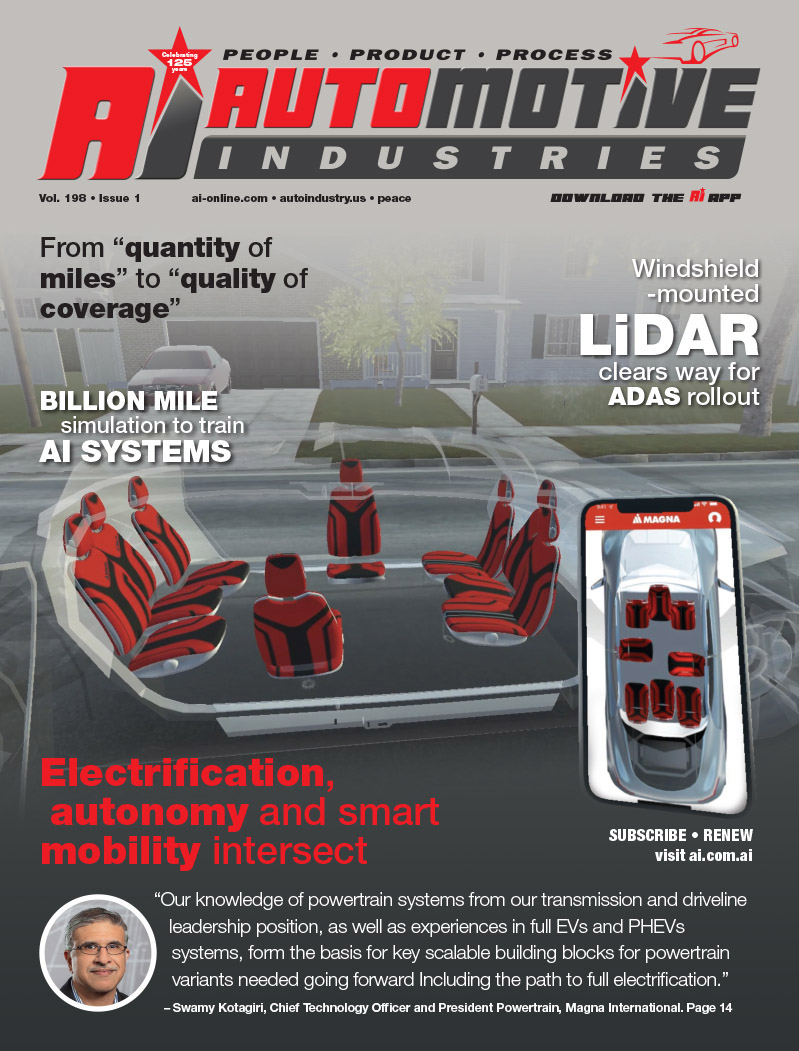
In the spring of 2012 Hauzer Techno Coating organized the conference ‘Environment Protection by Plasma Coating Technologies’, which attracted more than one hundred attendants. “As technology leader Hauzer wanted to bring together well-known experts in the field with interested people worldwide in order to make a step forward in our aim to help protect the environment by plasma coating technology,” Thomas Krug, CEO of Hauzer explains. The conference was followed by the launch of a new inline coating production platform, the Hauzer Metalliner.
“Plasma coating technologies can play an important role in environment protection,” Thomas Krug says. “Tribological coatings such as various Diamond Like Carbon (DLC) coatings can reduce friction and thus reduce fuel consumption and CO2 emissions. Each year a hundred million automotive parts are being coated in Hauzer equipment worldwide to help reduce these emissions. Another way to use plasma coating technology for environment protection is developing decorative coatings as alternatives for the environmentally unfriendly ‘electroplating on plastics’, which dissipates Cr6+, a banned substance in many countries worldwide.” Well-known experts from leading organizations, such as BMW, Schaeffler Technologies and Fraunhofer IST from Germany, University of Leeds from the UK, HVM Plasma from Czech Republic, Ionbond USA, Sidasa from Spain and Hauzer from the Netherlands presented their latest developments during the conference.
Automotive Industry
BMW set the tone by calling CO2 reduction the top challenge of the automotive industry. In their presentation BMW focused on coating solutions for the powertrain, whereas Schaeffler did the same thing for valve train. Both companies showed the potential to reduce friction by applying Physical Vapour Deposition (PVD) and Plasma Assisted Chemical Vapour Deposition (PACVD) coatings on their components. They concentrated on carbon coatings as part of the solution, but also mentioned the importance of interaction with lubrication. Leeds University then explained in detail what the effect of the lubricant is in the tribological system of DLC with oil and steel. Consequently, Fraunhofer IST gave the latest overview of their research on Diamond Like Carbon (DLC) coatings.
Cathodes and Decorative Coatings
As the expert on design and production of coating sources, HVM Plasma gave a lecture on target cooling effects in high rate and high pulse sputtering, followed by Ionbond, who presented the audience with their experience with the Hauzer Flexicoat® 1500, a large industrial batch machine used for tribological and decorative coating purposes. Sidasa, the Spanish company that developed Cromatipic®, presented the latest results of this two-layer decorative coating process, which is qualified for many automotive applications. Cromatipic® will have the same levelling effect and glossy appearance that ‘electroplating on plastics’ has, whereas it is an environmentally friendly, dry process. Hauzer Techno Coating shared their knowledge in two presentations. The first one explained about doped DLC and doped hydrogen-free carbon coating, ta-C, which both show higher temperature stability (> 400ºC) than the normal DLC (limit around 300ºC) and excellent friction reduction properties. The second Hauzer presentation showed the features and benefits of the new inline coating production platform, the Hauzer Metalliner.
Launch Metalliner
Thomas Krug explains why the step to an inline coating production platform was a logical one for Hauzer Techno Coating. “Plasma coatings can add functionalities, such as hardness, wear and friction reduction, corrosion protection and scratch resistance to many different products. But the price for these coatings must be as low as possible in order to manufacture competitive products. Since 1983 Hauzer gained a lot of experience in building robust, stable batch machines for mass production in for example the automotive market, so the step to an inline production platform for coating two dimensional and even three dimensional products was a logical one. The market moves forwards and we like to stay ahead by fully using our strength as a creative equipment manufacturer.”
Fully Automated Production Plant
The Hauzer Metalliner is an inline solution, which can be integrated in a fully automated production plant with guaranteed traceability of products. The design of the machine is smart, enabling the use of multiple plasma coating technologies together in one Metalliner. Upgrades of technologies are afterwards always possible. The modular design makes it possible to expand the productivity even at a later time. Starting with five process chambers for example and growing to ten chambers when production needs to be scaled up. Furthermore, the inline solution is characterized by high uptime and low cost of ownership.
Creative Equipment Building Team
The production of the Metalliner has been a combined effort of Hauzer’s creative project team together with dedicated suppliers. The result is a machine that can be productive in many different markets, using many different technologies and creating opportunities for companies that never thought about plasma coatings and their advantages before. Tailor-made, mass production and flexibility are all terms that directly relate to the Metalliner and Hauzer expects that this machine can make a change in two and three dimensional plasma coating and their markets.
Conclusion
“We wanted to take a step forward in protecting the environment with plasma coating technology,” Thomas Krug says. “And listening to our guests at the conference, we succeeded in that aim. They gave us feedback on the opportunities they saw for their own applications and all in all a lot of knowledge was shared. We hope this will lead to closer cooperation in our industry and an acceleration of developments in protecting the environment with the aid of plasma coating technology.”
More information: www.hauzer.nl.
More Stories
Hexagon’s MAESTRO reinvents CMM systems through digitization
Avery Dennison PSA tapes support rapid evolution of EV batteries
BRANO and DOMO join forces to replace aluminum with TECHNYL® polyamide