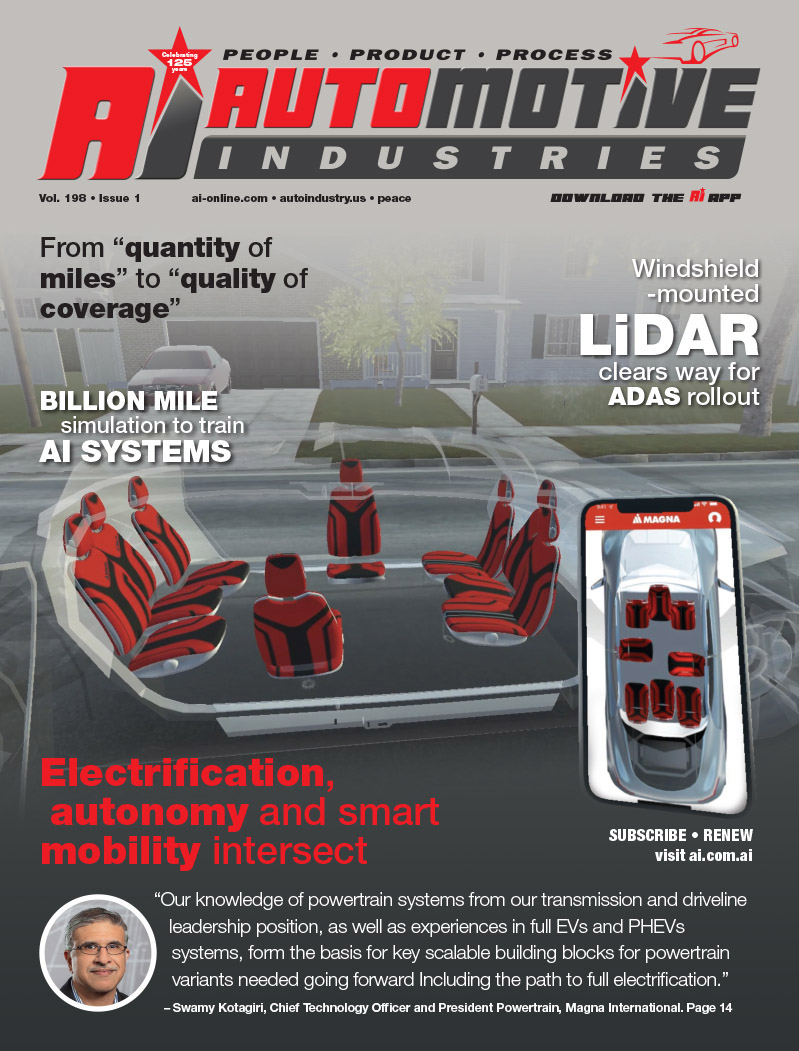
There is always an element of risk when introducing new materials or processes into any production process. But, for the motor industry, staying with the tried and tested has never really been an option.
At present the focus is on reducing weight through the use of new materials such as aluminum. One of the leaders in “de-risking” the use of new alloys is Constellium. With 23 plants around the world, the company has been providing aluminum products for close on a century. Listed on the New York Stock Exchange in 2013, it traces its history back to Pechiney, Alcan and Rio Tinto.
Automotive Industries (AI) asked Dr Andreas Afseth, Constellium R&D Group Manager, what measures the company has in place to meet the growing demand for lightweight components.
Afseth: We are investing massively in new capacity on both sides of the Atlantic. In Europe we are investing in 120 kT (thousand ton) Body-in-White (BiW) capacity in Neuf- Brisach (France) and a 20 kT capacity upgrade in Singen (Germany). We are also investing €22.5 million to expand casting, extrusion and fabrication capacity for aluminum automotive hard alloy bars and profiles in Decin (Czech Republic). In the USA we are building, through a joint venture with UACJ, a 100 kT finishing line which is scheduled to start operations in the first half of 2016. Constellium acquired Alabama-based Wise Metals in January 2015. Our plan is to invest US$750 million by 2022 to increase the hot rolling capacity to 700 kT and to add 200 kT BiW finishing capacity. As part of the US$ 750 million investment plan, we have announced in April this year, our plans to build a second 100 kT capacity BiW finishing line in the U.S. for an investment that is expected to reach US$160 m. It is due to start production in early 2018.
We have also unveiled our newly expanded plant in Van Buren, Michigan, where we have doubled our capacity for automotive structures. We are seeing faster growth in the USA, as they tend to use more aluminum per car, whereas in Europe the growth started earlier and is more progressive, with part-by-part substitution. In addition to increasing capacity for existing products, we are increasing our research and development (R&D) efforts. What differentiates Constellium is we know what it means to develop products, to do R&D and to bring innovative solutions to the market. Modern cars are quite complex, and with aluminium we can achieve and even exceed the technology standards required.
AI asked Lionel Chapis, Managing Director Automotive Structures, to tell us about Constellium’s automotive expertise.
Chapis: Our core business is really to transform aluminium, and because of the current market perspective we are able to provide very relevant solutions to the challenges that the automotive industry is facing. Our automotive experience and expertise encompasses different technologies, including rolling, extrusion, finishing and assembling. It enables us to offer a broad range of innovative solutions and meet lightweighting goals without compromising on design, safety and aesthetics.
Two business units dedicated to the automotive business provide rolled, extruded products and assembled components for automotive applications:
– Packaging & Automotive Rolled Products: for automotive body sheets with FORMALEX® / SECURALEX® / STRONGALEX® / SURFALEX® and their variants optimized for skins, inners and structure parts, for heat-exchangers cladded products and for decorative surfaces for interior and exterior car design Automotive Structures & Industry with design, simulation, prototyping and testing capabilities so as to develop structures based on functional specifications (new profile for side impact beams, new generation of high-strength Crash Management Systems, Body-in-White structures).
AI: What are your main strengths in the market?
Chapis: We are a global leader in the markets in which we mainly operate: packaging, automotive and aerospace, innovation is the oxygen that feeds our strategy and that enables bringing new standards of performance to customers. Being a leader in packaging brings us the ability to develop and produce solutions which are suited to high volumes and efficient processes.
Our strong R&D capabilities in the aerospace sector have enabled us to make step changes in alloy developments with our new breakthrough AIRWARE® solution. This has been developed closely with OEMs and Tier 1s. In the automotive segment we have built on the experiences in those two sectors to bring the best of both worlds: high tech alloys and tailored solutions, with a strong focus on manufacturing efficiency.
This has been achieved thanks to C-TEC, Constellium’s Technology Center, which brings together more than 200 specialists, and has characterization and numerical simulation equipment and unique prototyping facilities backed by world-class expertise. Our equipment can be used to design, test and model high performance materials and processes, from the nano to the macro scale.
AI: How closely do you work with OEMs?
Chapis: Our success in automotive has come from, and will continue to be driven by, a close working relationship with OEMs with whom we have developed strong long-term customer relationships. In-house engineering teams are deployed for the development of tailor-made solutions with our key premium OEMs customers.
Regarding CMS, we offer leadership service in modelling and simulation tools used at the early stages of vehicle development as well as in integrated and safer CMS with redesigned alloys associated to new designs (a good example is our work for the Ford F150). For body sheets, we currently supply 250 MPa yield strength sheet to Audi, with our Strongalex® solution. For the next generation we will reach 300 MPa, and future projects run up to 500 MPa.
AI: What does your new generation high strength Crash Management System offer?
Chapis: It is setting new industry standards for enhanced structural protection in the event of collision for the front and rear of a vehicle. At the same time, this new system is 15% lighter or 10 % stronger than current aluminum CMS.
AI asked Dieter Höll, Director Sales and Marketing, Automotive and Specialties of Constellium’s Packaging and Automotive Rolled Products business unit, to share some of the company’s development strategy and approach to innovation.
Höll: Our approach to innovation is based on our C-TEC innovation engine working in partnership with the best labs and universities worldwide, combined with very close work with OEMs. Our innovation focusses not only on products and solutions to the customer, but also on processes, including our own manufacturing technologies. In a time of capacity expansion we want to make sure we build the best lines and chose the best tools to serve the market.
A good example of our innovation engine is collaboration with Brunel University and Jaguar Land Rover. Announced in 2013, it obtained a £4.4M (Euro 5.1M) grant allocation from the Engineering and Physical Sciences Research Council (EPSRC) in the United Kingdom for the creation of a national scale-up facility for automotive light metals research. Constellium is co-director of the center and has full access for research and development projects. The center’s aim is to provide high-performance light alloys, resource-efficient casting technologies, extrusion processing technologies and component innovations. AI: Car makers want skin alloys that allow for very sharp lines. How does your new alloy Surfalex® HF meet this requirement?
Höll: Surfalex® HF is a new aluminum highly formable skin material for complex parts, which provides superior formability during the stamping process without compromising on design. Surfalex® HF has been nominated by the International OEM Advisory Board “AEE Innovation Star 2015”.
AI: What can we expect from Constellium in the future?
Höll: Our vision is to become a leading global player in all three of the markets in which we operate – aerospace, automotive and packaging. Our success in seizing opportunities across the globe depends primarily on our ability to deliver innovations. We already invest substantially in R&D and we have a track record of proven innovation. We intend to continue on this route and ensure that our R&D portfolio offers new alloys and lightweighting solutions for automotive body sheets and components for our OEM customers. Our technology center provides us with a “lab to industrial-scale” capability which enables us to bring ideas to fruition quickly and to de-risk innovations to customers.
AI
More Stories
Is Your 70 Series Land Cruiser Underperforming? Here’s How to Unleash Its True Potential
What to Do After a Motorcycle Accident to Protect Yourself
Injured in a Motorcycle Crash? Talk to an Attorney Now