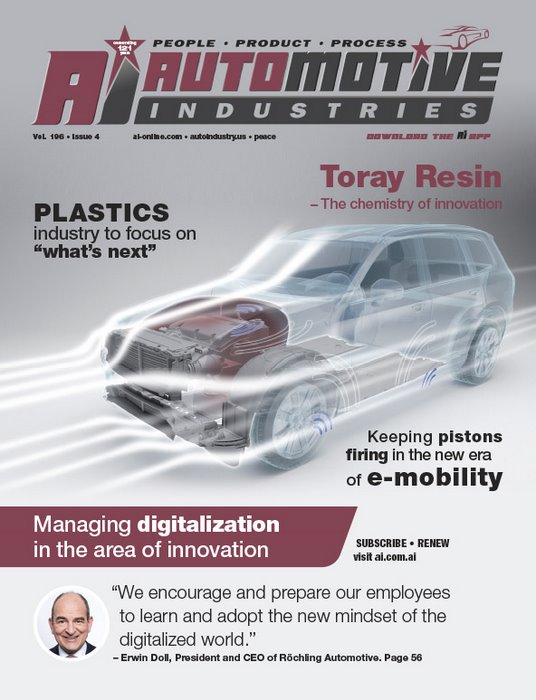
At a technical level the automotive industry is among the leaders in the development of smart factories as part of the fourth industrial revolution (Industry 4.0), which combines automation and data processing. Now companies are focusing on internal cultures and mindsets – where people schooled in linear thinking now have to be more creative and less structured.
Automotive Industries (AI) asked Erwin Doll, President and CEO of Röchling Automotive, how the company’s vision combines work satisfaction with efficiency.
Doll: Our vision is to boost the efficiency of mobility. Our motto is “enjoy efficiency”. It has two elements. One is enjoyment – having fun and being involved; and the second is being efficient in what you do and how you do it. I really like the concept of enjoying efficiency.
AI: How do you help OEMs improve comfort while reducing weight and emissions?
Doll: One example is what we did with a BMW model where the noise created by air passing through the ducting in the passenger compartment could be heard because the car was so quiet inside. A further challenge was the packaging, because there was not much space available and this especially in the center console. By using our compact air ducts we were able to reduce noise levels significantly. We did the same thing for Volkswagen on a manifold which is used to distribute heated air and with Audi revolutionizing the dirty air intake system on a SUV. These are examples of elements that bring comfort for the driver and passenger and at the same reduce weight.
AI: What are your areas of specialty?
Doll: We are very good at air-flow management, which includes the filtration of air. We understand, how to separate the air from water, and then to transfer it through the air conditioner or heater and into the passenger compartment. We are now also focusing on the thermal and crash management of batteries and the acoustics associated with air flow.
AI: How do you optimize airflow around the car?
Doll: We have developed our own software to calculate the pressure distribution and the airflow underneath the car – it is the only program of its type. The raw data was collected during many tests we conducted in a huge wind tunnel in Canada. Our advantage is that we can now accurately map the distribution of pressure under a vehicle. Once we understand how air is flowing we can define the needed solutions and engineer them to suit the minimum available space. We can say “in this area we have high pressure on the component, which means we need a fixing point and here we need this stability in the vehicle’s underbody panel in order to prevent or considerably reduce the generation of noise. Our know-how and expertise in layered material combinations and the manufacturing processes enables us to define the needed mix of different materials and solutions to attain the optimum result related to weight and noise.
AI: What are the newest innovations in thermodynamics and acoustics?
Doll: The newest one is the ISF – Integrated Sandwich Floor, a solution that combines excellent acoustic, crash and stiffness characteristics into a single component. At half the weight and thickness of a conventional floor system, the design also provides excellent electromagnetic compatibility, protecting the sophisticated electrical systems of hybrid and electric vehicles from potentially harmful magnetic fields. Basically, we are replacing the current steel structure of the car.
This has been made possible by our new lightweight materials. Stratura® Hybrid is a composite that outperforms steel in terms of energy absorption, crash and acoustic requirements. It consists of micro perforated aluminum layers combined with low weight reinforced thermoplastics (LWRT). Our lightweight solutions include a recently expanded line of cost-effective underbody panels for the small car segment.
AI: What powertrain technologies do you offer?
Doll: For many years we’ve supplied polypropylene air intake manifolds as well as complete low-pressure air induction systems. We also manufacture intake manifolds with integrated engine intercoolers in order to reduce weight. Performance is improved and emissions are reduced because the air is compressed, and this leads to more efficient combustion. Currently we are working on dedicated solutions for hybrid and e-charged engines and are bringing to market the first water injection system solutions for petrol engines.
AI: How does your delivery system minimize NOX emissions?
Doll: Our functionally integrated, injection-molded SCR tank is optimized in terms of both space and weight. It is also designed to compensate for expansion of the urea solution as it freezes. Utilizing our full-surface heater, the solution can quickly return to its liquid state to facilitate optimal system operation. In addition, anti-sloshing baffles reduce ambient noise. We also developed a new, patented and cost-efficient delivery system solution.
AI: What new mobility solutions are you developing?
Doll: We challenged small teams of in-house experts asking them to think completely out of the box and focus on three main areas. The first area is to reduce the body weight of vehicles in general but specifically of electric vehicles. The second area covers the housing, the charging and the thermal management of the battery itself, and the third area of interest was to improve the performance of fuel cells. Related to the lightweight body project, the team came up with the Integrated Sandwich Floor ISF.
On the battery side, we have developed housings and frames for pouch cells, which enables us to build battery stacks including plates for heat transfer. Stratura® Hybrid showed that this material is the ideal choice for lightweight battery housings with excellent acoustic characteristics and crash performance absorbing energy without breaking or splintering.
Related to inductive charging we integrated the charging coil into the car’s underbody, which facilitates convenient electric driving by removing the need to “plug in” cars and offers an all-in-one package, acoustic and aerodynamic solution by integrating the receiving coil into an underbody manufactured out of Röchling Automotive’s proprietary material.
It is a little trickier with the fuel cell as this technology does not have the necessary supporting infrastructure and hence drive in the market. Products developed in this field include bi-polar plates, an ion-exchanger and a degas bottle for the cooling system.
AI: What’s next for Röchling Automotive?
Doll: The biggest challenge for us, besides the ongoing innovation of products and the further development of our competences, is digitalization. We are already well advanced when it comes to the implementation of smart factory, due to the fact that the automotive industry requires from every supplier on-time delivery and the use of EDI (Electronic Data Interchange). All our machines have IP addresses to communicate with each other, and all our planning is done automatically. By mid-2019 all our plants will be smart, connected and digitalized.
Where the digitalization challenge lies is primarily in the alignment of our innovation process to the exponential world of digitalization. Most of our people still think “linearly”. If we decide to invest $20 million in a new plant, we know exactly how many machines we can buy, how many products we will produce and how much revenue this will generate. This is automatic as we have done exactly that for the last 100 years.
By embracing the digitalized world we have the opportunity to grow faster and exponentially. I think this is something that every company should do. There are people out there with completely new ideas. Look at Uber or Airbnb, which have no physical assets. We have started transforming the company to respond to the challenges of the digitalized world. We’ve changed the process of how we set the advanced development budget for next year. To date only a few people were involved in the innovation process. It was basically the advanced development team, the product management team, sales and marketing who looked at where the market is going, what the customer wants, and what ultimately should be done next. This year we did it differently.
We began the digitalization journey in January 2017 when the Board, together with a core team, defined the search fields on which our innovation should be focused. An internet-based gamified ideation and venture process was rolled out to all employees within the company worldwide. At the end, the best ventures had the opportunity to pitch their innovation and business plan. Not only did the top three venture teams receive the full attention of top management, an award and recognition, but their product ideas were – together with other valuable innovation ideas – considered for next year’s research and advanced development project activities.
We continue to encourage and prepare our employees to learn and adopt the new mindset of the digitalized world which continuously challenges the status-quo and pushes people and organizations to perform more audacious innovation.
More Stories
Is Your 70 Series Land Cruiser Underperforming? Here’s How to Unleash Its True Potential
What to Do After a Motorcycle Accident to Protect Yourself
Injured in a Motorcycle Crash? Talk to an Attorney Now