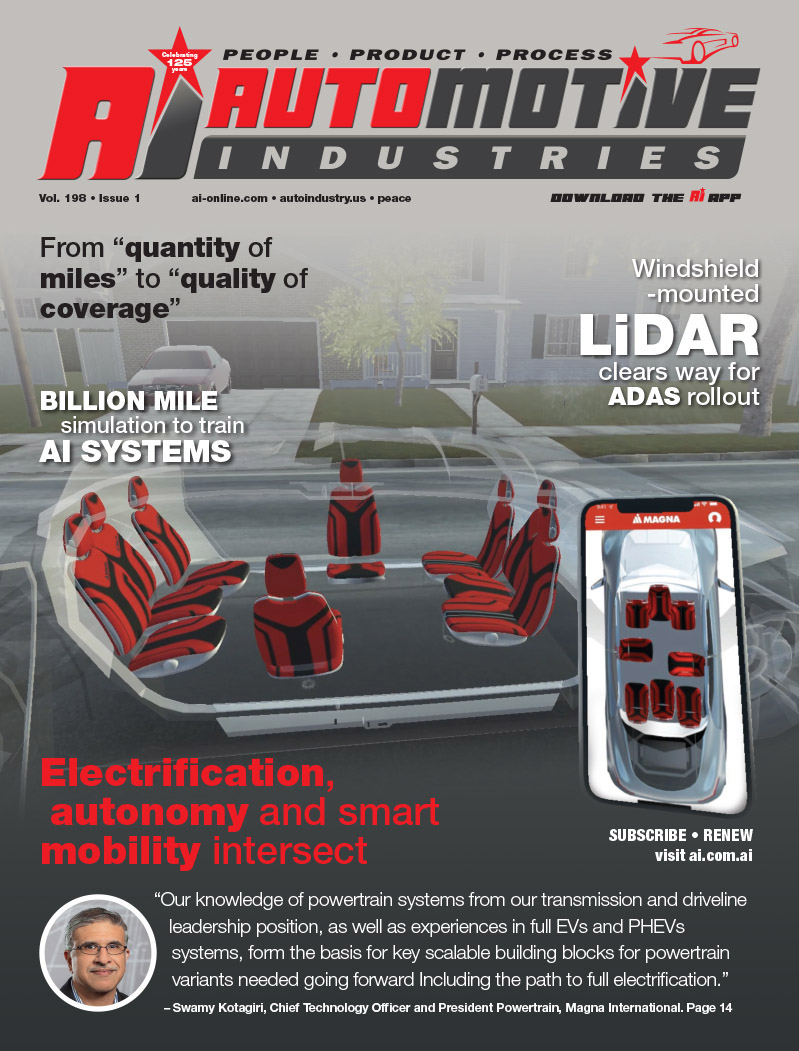
Building on a 40-year tradition of hands-on, shop-floor experience working with OEMs and custom molders, the Chem Polymer unit of Teknor Apex Company has invested in advanced engineering capabilities for assisting customers in developing applications for Chemlon® custom nylon compounds, according to national sales manager Todd Bresson.
“Chem Polymer has invested in new engineering resources to support customers at a time when many processors maintain lean engineering staffs and face reduced levels of assistance from other suppliers,” said Bresson. “We are prepared to provide quick-turnaround analysis and evaluation, helping customers to optimize design and reduce lead times. Our mission is to support customers through the entire product development phase, from napkin sketch through production approval.”
Among recent engineering investments by Chem polymer are these:
â— Moldflow® computer aided engineering. While Chem Polymer has long provided Autodesk® Moldflow® support for injection molding customers by outsourcing the work, it now has licensed MPA performance task level software and operates it in-house. The software includes modules for cooling, warpage, shrinkage, molded-in stresses, and fiber reinforcement. “Because the MPA software represents a significant upgrade over standard Moldflow,” noted Bresson, “we can provide advanced engineering resources to customers who utilize the standard version.”
â— RJG eDart System™ process control. This portable system can be implemented right in the customer’s plant, interfacing with most types of equipment. It reviews molding machine operation and process performance, making it possible to optimize the process for a new tool, troubleshoot a quality issue, and solve other problems.
â— Infrared camera imaging. Used on the shop floor, infrared imaging provides a highly accurate thermal image of the entire part surface instantaneously in real time, generating data that can be mapped, reported, and evaluated in electronic format. The analysis is critical in evaluating the cooling profile of a part and is more accurate than the conventional method of placing multiple pyrometers at various locations in the mold after the part has been ejected.
The investment in these technologies is the latest step in a program of modernization and expansion that began after Teknor Apex acquired Chem Polymer in 2004 and has included the construction of a 24,000,000-lb. (10,900-metric ton) compounding line at Brownsville, TN.
CHEM POLYMER is an international supplier of engineering thermoplastics for the transportation, consumer products, and industrial markets. It produces reinforced and specially modified compounds of nylon 6, 6/6, 6/10, and 6/12 under the Chemlon® brand. Founded in 1965, Chem Polymer was acquired by Teknor Apex in 2004. TEKNOR APEX COMPANY is a privately held firm with seven business units and 2,000 employees. It is headquartered in Pawtucket, Rhode Island, U.S.A., manufactures at 12 locations in the U.S. and overseas, and sells in 86 countries, serving markets in the plastics and chemical industries. Visit www.teknorapex.com
More Stories
Is Your 70 Series Land Cruiser Underperforming? Here’s How to Unleash Its True Potential
What to Do After a Motorcycle Accident to Protect Yourself
Injured in a Motorcycle Crash? Talk to an Attorney Now