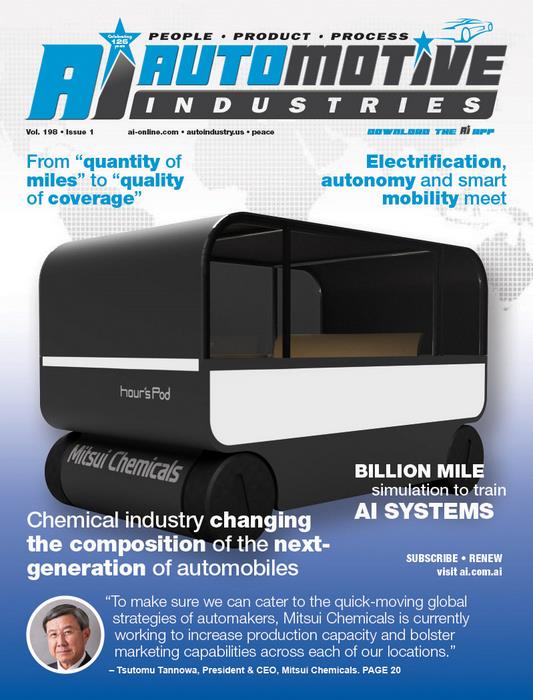
As automotive OEMs look to meet increasingly stringent regulatory demands that require a higher level of environmentally sustainable vehicles by reducing their weight, polypropylene (PP) is becoming a material of choice. This is especially true for parts that do not require paint processing, such as bumpers and instrument panels.
In response to the growing demand Mitsui Chemicals and its group company Prime Polymer co-announced in May 2018 that it would set up its first European PP compound production facility. Mitsui Prime Advanced Composites Europe is based in the Netherlands, and is scheduled to start operations in June 2020. Mitsui Chemicals Group currently operates eight production bases around the world (Japan, the U.S., Mexico, Europe, Thailand, China, India and Brazil) and has five research bases (Japan, the U.S., Europe, Thailand and China).
Mitsui Chemicals increased its automotive technology base through the January 2018 acquisition of vehicle designer and mold maker, ARRK Corporation for 30 billion yen. The two companies have committed to put each other’s technologies to use for achieving continued growth in the global market. ARRK will utilize the diverse range of Mitsui Chemicals products and materials technologies in carrying out design, prototyping and analytical activities. Meanwhile, Mitsui Chemicals will use the strengths of ARRK to broaden the range of business domains for its own products and services, strengthen its ability to market and offer solutions in the mobility domain and reach further commercialization.
Automotive Industries (AI) asked Tsutomu Tannowa, President & CEO, Mitsui Chemicals, how the company has realigned itself over the past few years. Tannowa: First of all, it was important to consider how materials can contribute to the CASE (Connected, Autonomous, Shared, Electric) and MaaS (mobility as a service) set of trends, which represent the mobility needs of the future. Looking at connectivity, for example, Mitsui Chemicals is developing sensing and semiconductor materials.
As autonomous driving continues to make its presence felt the industry will have a growing need for lenses and other optical materials, as well as for the coatings used on these. In addition, we’re going to see a significant shift in the approach to making cars comfortable, which will drive changes to the kinds of lighting and displays in cars. We are re-evaluating the materials we offer to the market for these applications. And then changes in powertrains are going to put greater emphasis on complex countermeasures to noise. One constant in the industry is the improvement of fuel efficiency – in other words, lightweighting solutions. Our work here includes an eight-base global system for PP compounds.
To make sure we can cater to the quick-moving global strategies of automakers, Mitsui Chemicals is currently working to increase production capacity and bolster marketing capabilities across each of our locations. We’ve recently received strong feedback for design qualities that enable not only lightweighting but also complex designs and a move away from painting. MOSTRON™-L, a long glass fiber reinforced plastic is already beginning to replace metals in automotive rear doors, and we are increasing production capacity globally. Elsewhere, we’ve been expanding capacity for the likes of MITSUI EPT™ – a high-quality synthetic rubber made using a proprietary metallocene catalyst – and ADMER™, an adhesive resin able to help with both lightweighting and freedom of design for gasoline tanks. We’ve also paved a path going forward for MILASTOMER™ – a lightweight and luxurious material for automotive interior surfaces – by establishing a system of nine bases around the world. A new grade which offers an attractive uncoated appearance is finding increased adoption in airbag covers. Mitsui Chemicals provides a range of other materials to the auto sector.
Examples are our TAFMER™ elastomer modifier, urethane materials that are used in seat cushions and soundproofing, as well as coating materials that help to improve vehicle design. Then we help to reduce weight through a range of carbon fiber composite materials, including carbon fiber sheet molding compounds and UD (unidirectional) tapes. These include AURUM™, a thermoplastic engineering plastic, which is seeing increasing use around engines; ARLEN™, a modified polyamide 6T material used underneath bonnets; and LUCANT™, a lubricant for gear oil applications that serves to boost fuel efficiency. POLYMETAC™, a technology for the integration of metals and resins, is being adopted for water-cooled lithium-ion module parts by European OEMs for their 2019 model ranges.
AI: How will your first European production plant help boost business in the region? Tannowa: Having a European base is a crucial part of supplying to European OEMs. While Mitsui Chemicals has had sales operations in Europe for some time, the continent has traditionally made up only a very low proportion of sales in our broader global business. But by establishing a research base in 2014, we’ve made ground in strengthening our relationships with European OEMs. This has given us a better understanding of solutions in the field, and the expectation is that our products will be increasingly adopted by the various European OEMs going forward. Our initial plans are centered on the Netherlands, where we hope to begin operations in 2020 with a production capacity of 30 kilotons per year. But we intend to expand our regional capacity as required. By integrating production, sales and research – and setting up a system to supply European OEMs with lightweighting solutions – we hope to steadily expand our European business.
AI: How has your acquisition of ARRK helped boost Mitsui Chemical’s position as an automotive supplier? Tannowa: As a global development assistance company, ARRK is able to work on the design, analysis, molding and prototyping of vehicles, and has a system that allows it to support a customer’s product development from the concept stage. Mitsui Chemicals’ ideal for OEM work then is a setup in which we work right from the material stage to provide the solutions required by OEMs. Integrating ARRK with Mitsui Chemicals will therefore tie into improved marketability in the area of lightweighting as the industry continues its trend toward resin-based auto parts.
The move works from ARRK’s perspective as well, allowing it to provide development support services that have high added value going all the way through to materials. It’s also worth noting that ARRK sees 60% of its business coming from Europe – much of this from subsidiary P+Z Engineering – and is deeply involved in supporting the development of prominent OEMs in the region.
At JEC 2019 we leveraged the technological synergies of both companies, producing a mock-up to use for exhibition. In creating the “hour’s Pod” concept car, we’ve marketed the potential for a range of auto parts to switch over to resin. The hour’s Pod serves to market the potential uses of thermoplastic UD tape that has gone through various production methods; lightweighting by way of the polymetac technology for metal–resin integration; and new concept seats that contribute to comfort, among other things. If Mitsui Chemicals were alone, it would have been difficult to come up with a concept car on this sort of scale. But by joining forces with ARRK, I feel that we’ve been able to significantly alter the way in which we communicate, and that we’ll see a major boost to our client-oriented capabilities going forward.
The rise of autonomous driving is bringing a new turning point in both the automotive world and widespread notions of what a car is. As all sorts of things mingle with technology, conventional notions and models are being overturned. But then the chemical industry’s always been at the intersection of such innovations – and so we’ll continue to watch for signs of change while providing solutions for the mobility of the future
More Stories
Is Your 70 Series Land Cruiser Underperforming? Here’s How to Unleash Its True Potential
What to Do After a Motorcycle Accident to Protect Yourself
Injured in a Motorcycle Crash? Talk to an Attorney Now