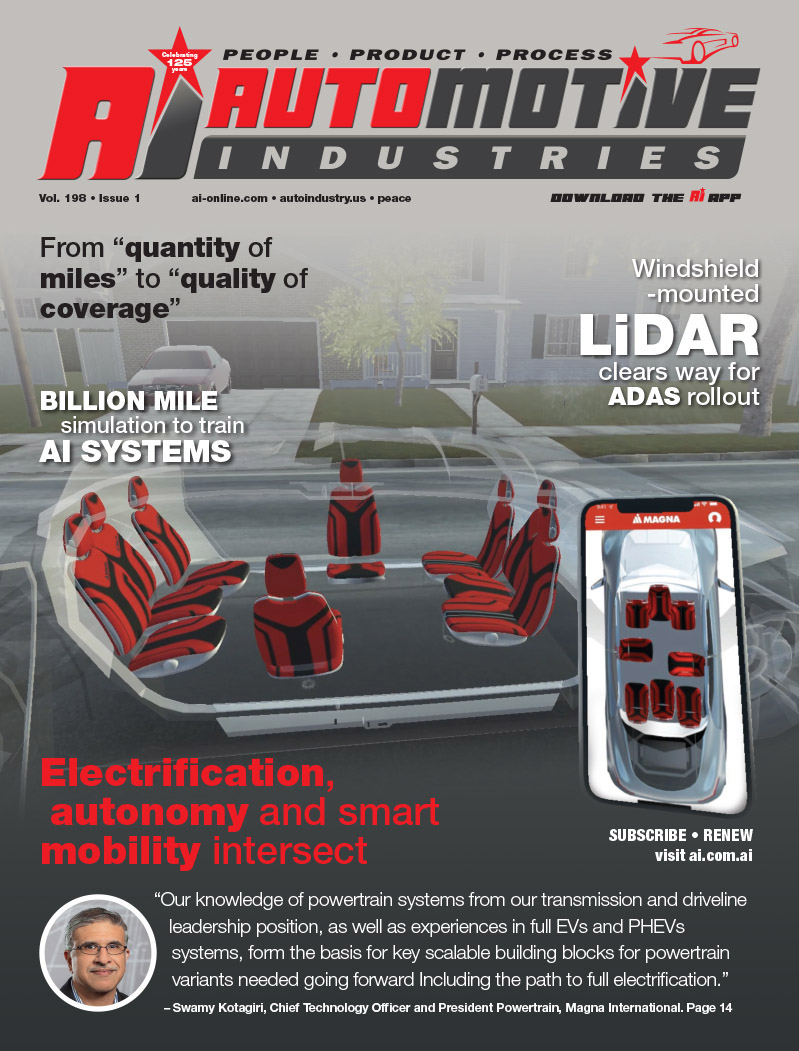
For ITT’s brake-pad factory in Barge, Italy, the drive towards producing environmentally-friendly brake pads has started with the factory processes themselves. The company has stopped scorching its friction materials using new infrared cooking technology that it developed which lowers energy consumption and generates less carbon-carrying soot.
ITT has also installed afterburners on bonding systems to eliminate the emission of traces of formaldehyde. The system also improves environmental conditions for the workers as it collects vapors that were previously being emitted during the bonding process. Power consumption has been reduced through the installation of a system which progressively reduces the supply voltage, while keeping the levels of illumination at an optimum level.
A tri-generation system recycles energy within the plant. The gas-fired plant produces virtually all the electricity needed by Barge. The heat produced by the turbines (two 3 MW units) is recovered for heating in winter and, and in summer to cool the plant (by turning the heat on a cold absorber). Peak temperatures within the plant have been reduced by five to six degrees, reducing levels of discomfort for workers. In addition to saving costs and improving productivity, the system has reduced CO2 emissions by 12,000 tons a year). The plant – the biggest producer in the ITT group – can produce more than 75 million pieces every year. ITT produces and sells about 120 million brake pads a year for car manufacturers around the world. The company sees a large portion of its manufacturing switching to pads designed to meet the demand for a new “green wave” of hybrid and electric cars.
Green aftermarket
ITT has developed “green” products free of antimony and copper specifically for the aftermarket. There is ongoing research into the development of OE materials with low amounts of copper. The objective is to define materials with less than 5% of copper by 2014. The product is being developed in partnership with a global supplier of resins and the University of …….. ?
Automotive Industries (AI) asked Pietro Buonfico, ITT Mo.Tech. VP and Global R&D Director, what progress the company was making in the development of brake pads for electric vehicles.
Buonfico: ITT Mo.Tech. has developed a special material for electric vehicles using existing platforms and projects. An example is the Renault W10 project.
AI: Are any ITT brake pads now installed (or soon to be installed) on electric/hybrid vehicles?
Buonfico: We prefer to answer with this statement: “There are currently many open projects related to electric, or hybrid vehicles and the major European car manufacturers are focusing on these new applications. ITT Motion Technologies is on their side in these future developments and the first platforms will arrive within the next two years on the market”.
Professionals within the industry will know about the projects.
AI: Are they being tested in the lab or on test tracks?
Buonfico: ITT Mo.Tech. is providing pads to some car manufacturers to develop electric and hybrid vehicles. Tests are in an experimental phase.
We are involved in a number of major projects with the likes of VW, Renault and Toyota.
AI: How does a brake pad for an electric/ hybrid car differ from one for a gas-powered car?
Buonfico: Sometimes the material is the same, and is specified as such by the customer. At other times, it is necessary to reduce noise issues, such as wire brush and creep groan through a different mix or molding process.
AI: Do they have to be quieter?
Buonfico: Due to the fact that there isn’t any engine noise, the friction material has to be as quiet as possible. Electric and hybrid cars are significantly quieter than their gasoline-powered peers because they reduce or eliminate the thousands of tiny explosions that create mechanical energy and move pistons and other parts in standard engines.
Having eliminated noise pollution under the hood, auto makers now need brake pads that work without screeching, squealing or the very common “creep groan” grinding noise that is caused by the car straining forward as the brake is released.
AI: Do they have to be lighter?
Buonfico: The weight of friction material in a vehicle is pretty low, so ITT is not asked to produce lighter pads.
AI: Do they have to be configured/powered differently?
Buonfico: The high weight on the rear axle due to the battery location means that the rear braking system has to have the same power as that on the front axle.
What are the challenges in manufacturing these new types of brake pads?
Buonfico: The biggest challenge is to find a good compromise between the same level of performance and lower noise.
AI: What is the market potential for these types of brake pads?
Buonfico: With the ever rising concerns regarding the oil prices and the impact of global warming due to rising carbon emissions, car manufacturers are investing huge amounts of money in the development of hybrid-electric and electric vehicles.
According to a recent study conducted by JPMorgan, hybrid and electric vehicle sales are already a significant portion of the market, and sales are set to grow. Last year, some 480,000 total hybrid vehicles were sold around the world, which represents less than one percent of global sales. By 2020, JPMorgan predicts that 11.28 million hybrids will be sold annually, representing over 13% of all vehicles sold. The market for brake pads will parallel this growth.
Focus on engineering products
In January, ITT Corporation announced a decision to separate its businesses into three distinct, publicly traded companies.
ITT Corporation will continue to be a diversified global manufacturer of highly engineered industrial products and high-tech solutions. Its global platform will include ITT’s current Industrial Process business, as well as its Motion Technologies, Interconnect Solutions and Control Technologies businesses, which includes the shock absorber, brake pad and other energy absorption solution businesses.
The other two companies will focus on water-related businesses, and defense and information solutions.
More Stories
Is Your 70 Series Land Cruiser Underperforming? Here’s How to Unleash Its True Potential
What to Do After a Motorcycle Accident to Protect Yourself
Injured in a Motorcycle Crash? Talk to an Attorney Now