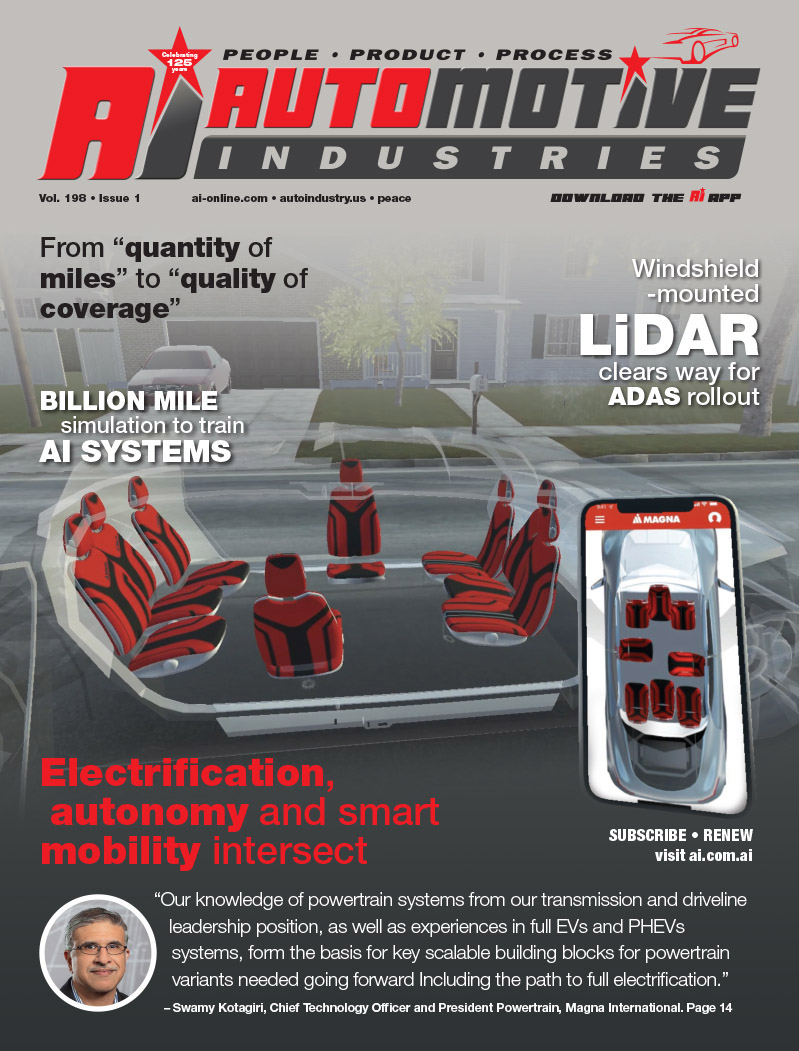
Whether for ground vehicles, planes, or satellites, lighter is better-and often required-not only for fuel efficiency but also for tactical mobility.
No matter what the vehicle, every extra ounce of weight requires more fuel-which is costly, adds more weight, and may be difficult to supply in remote locations. Excess weight can even threaten a vehicle’s viability, whether for tactical objectives such as airborne transport to a drop zone, for launch out of Earth’s orbit, or for commercial or consumer adoption.
To meet the challenge of reducing vehicle weight, engineers are tackling the problem in an unexpected way. With an innovative fastener technology, they’re eliminating the weight and complexity of secondary locking features in military, aerospace, and consumer vehicles, including a prototype of the Joint Light Tactical Vehicle (JLTV), a family of next generation military vehicles still in development.
The JLTV, for instance, which is designed to offer the U.S. Army and Marine Corps. better light tactical vehicle payload, protection, performance, and fuel efficiency, must be light enough to be transported by helicopter or C-130 aircraft. Despite the shock and vibration of off-road driving and battlefield conditions, it must remain reliable.
Why Fasteners?
Fasteners may not be the first place engineers look to reduce vehicle weight, but the typical car has about 15,000 fasteners and most military and aerospace vehicles have even more.
While not every fastener has a nut, bolt, and locking feature, critical joints often use lock washers, lock wires, cotter pins, brackets, or other secondary locking features, which cumulatively add a significant amount of weight and complexity. The problem is that when a fastener loses its clamp load, it no longer does its job and safety, recall, or warranty issues occur. Locking devices are commonly added to retain clamp load, but do not always hold up under shock, vibration, or temperature extremes.
An overdesign ‘belt and suspenders’ mentality has prevailed, for instance, in automotive design where putting 8 bolts on an exhaust manifold is common when 4 might do. This has led to big, heavy, fuel inefficient cars.
To reduce vehicle weight, assure joint integrity in critical areas, and prevent safety, warranty, or recall issues, vehicle engineers are finding a solution in an innovative fastener called Spiralock. For instance, by eliminating the need for secondary locking features such as lock washers, lock wires, cotter pins, and brackets in the JLTV prototype with a fastener like Spiralock’s, potential weight savings could be in the 20 to 40 lbs. range or more per vehicle.
A chassis on a typical military vehicle is held together with about 200 7/8″ bolts, nuts, and lock washers. Eliminating the need for the 7/8″ lock washer, which weighs about 0.065 lbs. each, could reduce weight by about 13 lbs. per vehicle. That’s for just one size of fastener. There could be dozens of fastener types and sizes per vehicle that could safely eliminate their secondary locking features with the use of Spiralock.
Traditional locking fasteners do not address a basic design problem with the standard 60-degree thread form: that the gap between the crest of the male and female threads can lead to vibration-induced thread loosening. Stress concentration and fatigue at the first few engaged threads is also a problem, along with an increased probability of shear, especially in soft metals, due to its tendency toward axial loading. Temperature extremes can also expand or contract surfaces and materials, potentially compromising joint integrity.
Engineers, however, have successfully attacked these challenges while reducing component weight and enabling re-usability with the innovative Spiralock locking fastener. This re-engineered thread form adds a unique 30-degree wedge ramp at the root of the thread which mates with standard 60-degree male thread fasteners.
The wedge ramp allows the bolt to spin freely relative to female threads until clamp load is applied. The crests of the standard male thread form are then drawn tightly against the wedge ramp, eliminating radial clearances and creating a continuous spiral line contact along the entire length of the thread engagement. This continuous line contact spreads the clamp force more evenly over all engaged threads, improving resistance to vibrational loosening, axial-torsional loading, joint fatigue, and temperature extremes.
The Spiralock locking fastener has been validated in published test studies at leading institutions including MIT, the Goddard Space Flight Center, Lawrence Livermore National Laboratory, and British Aerospace. It has been used in extreme fastening applications with virtually no chance of recall: from the main engines of NASA’s Space Shuttle; to the Saturn Cassini orbiter and Titan Huygens probe; to medical implants, artificial limbs, and heart pumps.
“The Spiralock fastener’s ability to retain clamp load under extreme shock, vibration, and temperature with less weight, complexity, and maintenance makes it a natural choice for military, aerospace, and consumer vehicles,” says Ray Genick, Director of New Business Development and former VP of Engineering at Emhart Teknologies, a leader in the design and creation of unique assembly technologies. “It retains clamp load even with dissimilar exotic materials, such as composites and titanium, which is important in reducing vehicle weight.”
Weight savings also come from reducing fastener size or number with an equal or better safety margin compared to fasteners with the standard 60-degree thread form, according to Arlindo Marques, Director of Global Engineering for Spiralock.
“The key is Spiralock’s full contact along the entire engaged length of the thread,” says Marques. “This reduces thread galling, or microwelding, especially in the heat-resistant nickel alloys becoming important in automotive. It enables fastener reusability up to 50 times, simplifying installation and maintenance. And it makes the thread form self-centering, which improves performance and eases the balancing of high-RPM diesel and turbo systems.”
For military/aerospace-related applications, the locking fastener is used by industry leaders such as Oshkosh Truck, BAE, Boeing, Honeywell, NASA, Raytheon, Rocketdyne, Hamilton Sundstrand, and the US military. The uses range from aircraft cockpit instruments and actuator devices to missile and Space Shuttle engines, as well as clamps for circuit boards and generator cables.
In automotive, the locking fastener is used in applications ranging from ring gears, torque converters, and chassis assembly to exhaust manifold joints and axle, turbine, or transmission housings. For diesel engine applications, it has been adopted by Caterpillar and Mack Trucks.
Spiralock, which is part of Emhart Teknologies, a leader in applied fastener technology, is used for design challenges in a wide range of industries including military/aerospace, automotive, heavy truck, construction, rail, oil drilling, agriculture, medical, and food processing. Production changeovers to the fastener are typically quick and seamless, often requiring just an exchange of traditional nuts, wire inserts or simply drilling out and re-tapping existing parts stock that have unreliable standard tapped holes.
More Stories
Is Your 70 Series Land Cruiser Underperforming? Here’s How to Unleash Its True Potential
What to Do After a Motorcycle Accident to Protect Yourself
Injured in a Motorcycle Crash? Talk to an Attorney Now