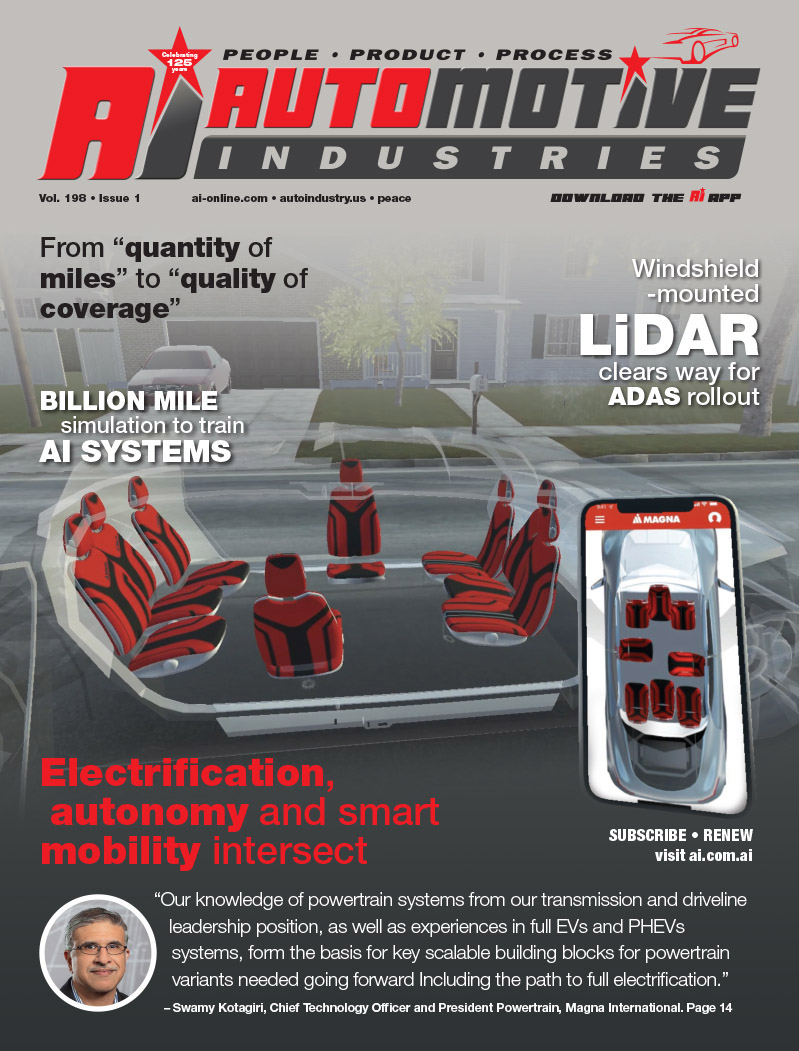
Ongoing research into advanced materials coupled with experience built up over decades means that OEMs and Tier suppliers can have products made to order.
A leading example of the capabilities of suppliers is Teknor Apex, an international custom compounder of plastics headquartered in Rhode Island, U.S.A. It has a database of more than 40,000 compound formulations, and has amassed company-wide expertise in major markets for compounds markets, including the automotive sector.
Automotive Industries (AI) asked Ger Vroomen, Senior Automotive Market Manager at Teknor Apex, how the company’s TPE and PVC divisions continue to rise to meet the challenges of the auto industry.
Vroomen: The company consistently invests in research to develop new products and help customers meet challenges arising from emerging regulations or changes in the marketplace. We enjoy long-term relationships with many customers. These relationships enable us to anticipate the changing needs of the industry.
AI: How customized are your products?
Vroomen: Instead of relying on what is already available in our product range that might provide a solution for a customer, we ask the customer to specify the re¬quirements of an application and then seek to de¬velop exactly the right compound formulation for it. A timely example of solving customer problems involves our Nylon division. There has been a worldwide shortage of polyam-ide 12, a polymer whose largest application is in fuel-handling components of automo¬biles. On behalf of a customer we formu¬lated two compounds based on polyamide 6 / 12 that provide comparable chemical resis¬tance—a critical property in fuel systems—and minimal moisture absorption. One of the new compounds is reinforced with carbon fibers, whose electrical conductivity provides antistatic properties; the other has glass fiber reinforcement, for the strength and stiff¬ness required in the bodies of fuel line connectors.
AI: Tell us a little about Teknor Apex’ expertise in the automotive sector.
Vroomen: Automotive has long been a major market for all of our many product families, and in the case of vulcanizate elastomers and nylon compounds, it has been the largest market by far. In serving automotive customers, we take a coordinated approach that embraces all of our product capabilities, as well as our worldwide network of compounding plants, engineering support centers, and testing laboratories.
AI: What makes your Sarlink® TPE’s so effective?
Vroomen: As olefin materials, Sarlink TPVs permit coextrusion and over-molding applications with rigid substrates, making possible innovative designs that save costs and weight. And as thermoplastics, they provide greater design freedom and productivity than thermoset rubber, plus the advantage of recyclability.
We have developed a new range of TPE materials for all kind of sealing system applications. These products will result in further system cost reduction in combination with robustness processing. In addition, the product engineer will enjoy more design flexibility.
Our production-grade prototype equipment enables us to run everything from a simple single-durometer extrusion to complex multi-extrusions with end-of-line finishing or corner molding, duplicating any real processing condition. By proving out concepts utilizing our time and equipment, customers can greatly reduce the launch burden for a new product.
As an example of how we work with automotive sealing customer is a the roof seal on a multi-purpose vehicle built by the Chinese OEM BYD. The company came to help save weight and reduce manufacturing cost. In a two-year cooperative program between BYD and our Sarlink team in Shanghai, we developed BYD’s first TPV seals. The seals produced from Sarlink TPV weigh 25% less, saving a total of 0.15 kg per vehicle over EPDM rubber. At the same time, the TPV seals provide the economic and environmental advantages of using a thermoplastic. Sarlink TPV has been replacing EPDM because it eliminates the labor- and energy-intensive vulcanization step required in the processing of thermoset rubber. Another important advantage is the recyclability of both process scrap and finished components.
Sarlink TPV compounds also provide outstanding rubber-like elasticity with physical properties superior to those of many commonly used TPEs for under-hood applications. These properties include excellent long term resistance to heat, automotive fluids, oils, and road grime. Typical applications are plugs and fasteners, boots and bellows, bumpers and mechanical stops, air management systems, and mechanical cable and line jackets.
AI: What are some of the features of Tekbond®?
Vroomen: The Tekbond range of TPEs for over-molding is based on a variety of proprietary chemistries, enabling Teknor Apex to provide compounds for adherence to a variety of styrenic and engineering thermoplastic substrates, such as polystyrene, ABS, polycarbonate, polycarbonate/ABS alloys, nylon, PBT, and COPE. Customers can combine elasticity and rigidity in a single part, producing innovative designs that save weight and eliminate assembly. A simple example is that of a rigid housing with a molded-in TPE gasket. I should add that two of our other broad TPE families, Monprene® and Sarlink®, include compounds that function effectively in over-molding and adhere to polyolefin substrates such as polypropylene and polyethylene.
AI: What are some of the future technologies for the automotive sector?
Vroomen: Teknor Apex is one of the few TPE compounders which has access to the relatively new OBC products. In cooperation with Dow Chemical we are exploring the use of these new TPE materials for all kinds of automotive applications. The acquisition of Sarlink from DSM provided Teknor Apex with state of the art dynamic vulcanization technology. This technology, combined with existing compounding technology combining different chemistries, has provided interesting new TPE materials for a wide variety of markets.
There are clear interests in bio based TPE materials in the automotive industry. Teknor Apex already anticipated on this and a relatively new business unit within the company is currently developing several bio based concepts. The first bio based PVC is already active in the market.
AI: How do you fulfill customers’ requirements across the globe in the shortest possible time?
Vroomen: We coordinate our efforts in all of the world’s regions. This enables us to draw on the company’s extensive automotive industry experience in Europe, the Americas, and Asia to utilize engineering support and laboratory resources in all three regions, and to manufacture any compound anywhere, providing the same formulation for a customer no matter where in the world that customer operates plants.
“Rather than sell the customer a certain type of compound because it’s the only type we offer, we can select among multiple types to ensure that what we offer is exactly the right compound for the job.”
More Stories
Is Your 70 Series Land Cruiser Underperforming? Here’s How to Unleash Its True Potential
What to Do After a Motorcycle Accident to Protect Yourself
Injured in a Motorcycle Crash? Talk to an Attorney Now