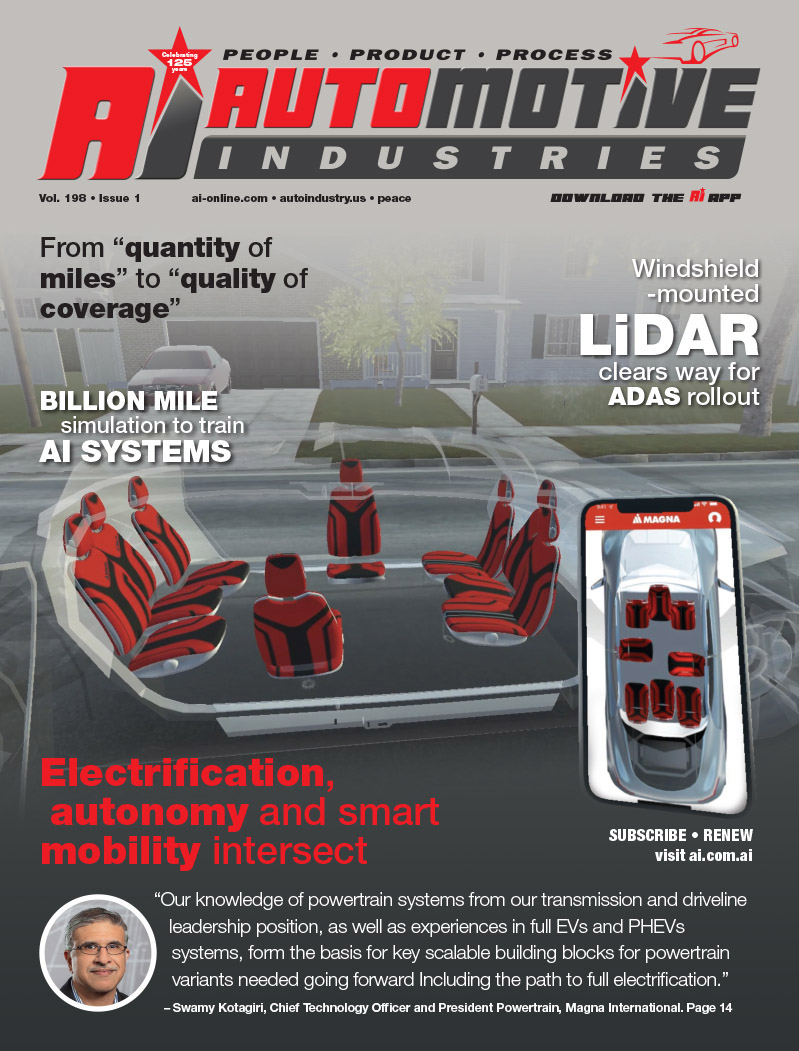
Fierce competition among material suppliers is nothing but good for auto builders and consumers. The industry is certainly in a state of flux with respect to consumer buying trends, safety and fuel economy objectives, global versus regional platforms, powerplants and more. I’m 100 percent sure I prefer this state of flux to stagnation.
The battle royal for material supremacy tends to outstrip the automakers ability to absorb it all. Whether you are looking at reinforced plastic, aluminum, magnesium or steel, mechanical properties are moving targets and developments in finishing processes keep opening up new application opportunities. There are new materials in the wings just waiting for some design team with the boldness to put them to use.
With this year’s materials issue, we delve into this and take the pulse of each sector and look from several perspectives at new applications and trends.
True, what’s exhilarating to one person is frustrating to another, so when one considers the vast and growing array of advanced automotive engineering materials it can either look pretty baffling or extremely bounteous. I go with the latter.
These are not times for the timid so the basic choice is strap it on or take a back seat. It’s more and more agreed upon that the best opportunities for cost savings lie in more cleverly bringing advanced and mundane material systems together and eliminating parts and processes along the way. And there’s absolutely nothing mundane about that.
It isn’t so much that a particular material is chosen but the way it is applied that matters. It doesn’t have to be exotic to be good.
Everyone seems dizzy with joy over GMs new Epsilon platform and yet the body-in-white (BIW) is all steel, and 41 percent of it the low carbon variety — although that percentage will shrink as the platform evolves and matures.
The manager of the Malibu version of the platform, Michael Weber, thinks that if he were beginning a new design today that he could use as much as 80 percent high strength steels of different types and that considerable cost and weight could be trimmed from the BIW by rigorously applying a minimum thickness strategy and also reducing the number of parts.
Not only are the choices greater and the materials improved today versus even five years ago, but the CAD, CAE and CAM application tools for putting them in place have improved in leaps and bounds. There are very few constants in this complicated process of making the right choices.
Stripped to the essence, however, cost and weight and safety continue to form the triumvirate of objectives in the materials selection game. And their importance is pretty evenly distributed. But that’s about the only thing that hasn’t changed.
More Stories
End-of-Life Vehicle Management Trends in New Zealand: What’s Next?
Fleet Management Made Smarter with Diagnostics Tools
Best Wheel Size for Off-Road Adventures: What People Get Wrong