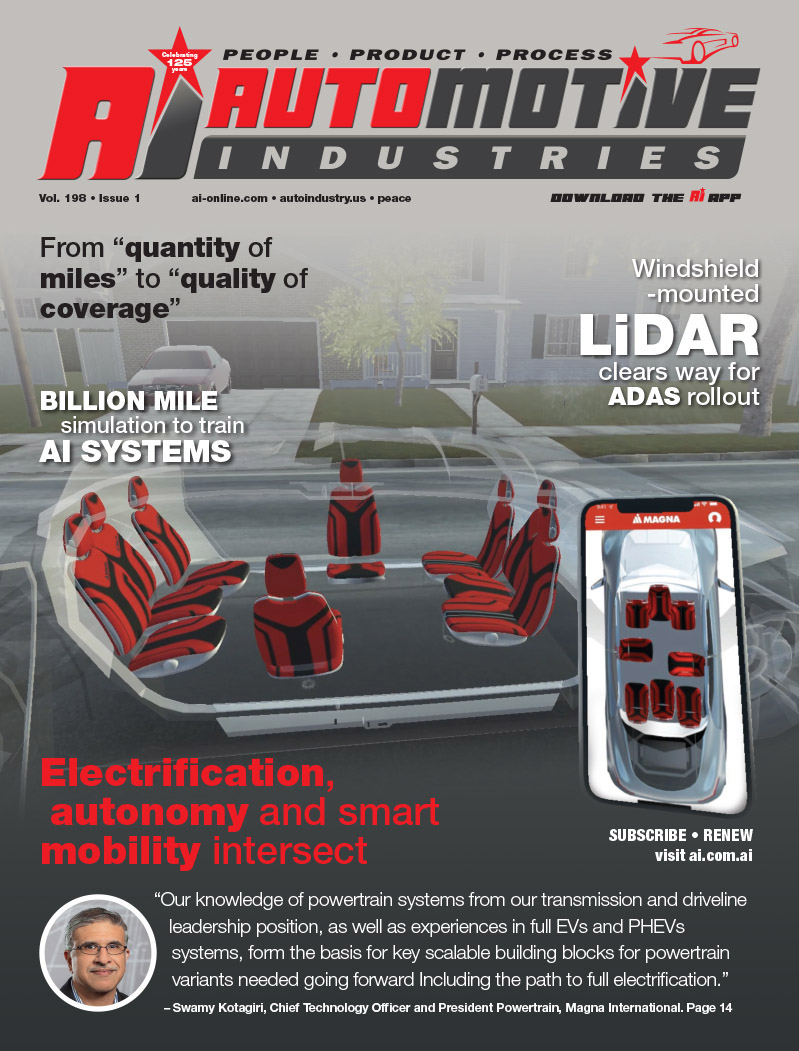
Sequencing 106 variations of encapsulated windows tackled by Dura Automotive.
![]() |
One of nine robots applies the color-specific applique to a Ford Explorer liftgate. |
Then there’s the Lawrenceburg, Tenn., glass encapsulation plant of Dura Automotive. Folks there see the glass as being exactly where they want it when they want it — to sequence exactly with the build schedule for Ford’s Louisville and St. Louis assembly plants. Lawrenceburg is said to be the largest window encapsulation plant in the world.
The plant produces sliding windows for pickup trucks, quarter windows with lights and lift gate assemblies at a volume of approximately 480,000 units per year.
The lift gate assemblies for Ford’s Explorer, Mountaineer and Aviator are produced on an In-Line Vehicle Sequence System (ILVS) that matches up exactly with Ford’s build sequence at Louisville and St. Louis. It ships between four to eight truck loads of liftgates per day to those plants.
Because of the variety of colors available on those vehicles, and the different glass tints, as well as badge specific appliqu?s, there is currently a matrix of 106 lift gate combinations that Dura builds for Ford’s SUVs. The system is capable of handling up to 200 different combinations.
Denzil Abney, director of engineer, Eddie Haygood, manufacturing engineer, Mike Roberson, process engineer, and Allison Sanders, production scheduler, all Dura employees at Lawrenceburg, explained the system to us.
Lawrenceburg provides PVC and RIM encapsulation for other customers also including Chrysler, Nissan, Honda, Subaru and GM. For the Explorer, Mountaineer and Aviator, the lift gates are all RIM encapsulations. The ILVS program was launched in February 2000 for the Explorer/Mountaineer vehicles and then later extended to the lower volume Lincoln Aviator. Lawrenceburg produces on the order of 10,000 lift gates per week for Explorer/Mountaineer versus 600-700 per week for the Aviator. There’s a separate high volume line and low volume line.
“The Aviator lift gate is supplied only to St. Louis, but the Explorer lift gate is supplied to St. Louis and Louisville,” explained Abney. “The Explorer line is a large one with one segment of it dedicated to St. Louis and another segment to Louisville.”
The basic process consists of the glass encapsulation process itself which puts a peripheral moulding on the window, attaching various parts like hinges, strikers and ball studs, and for the liftgates in question, applying a vehicle body colored plastic appliqu? with badge specific trim that runs below the window from one side of the liftgate to the other. It is put in place by a robot, tacked with hot melt and bonded with urethane. There are nine robots on the ILVS line.
![]() |
Liftgate window assemblies are ready to ship in their prescribed build order. |
“Originally, Ford was going to attach the appliqu?s at their facilities,” Abney related, “but in the development phase we saw an opportunity to save them all those headaches by doing it here.”
The ILVS is completely data driven, of course, and the data initiates from Ford in the form of 12,000 new records each morning with VIN numbers, part numbers, ship dates and destination data representing six days of sequenced building of the three vehicles at the two plants.
“I actually get a 26 week release from Ford,” scheduler Sanders told us, “but the only concrete numbers are out six days. And because we’re operating on a JIT program we’re unable to get any farther ahead comfortably than two days. So on Monday, I’m releasing scheduling for Tuesday, on Tuesday we make releases for Wednesday and so on.”
![]() |
Dura supplies JIT liftgates for the Explorer, Mercury Mountaineer and Lincoln Aviator. |
“Whenever scheduling creates a shipment with a ship date, that defines how many parts in sequence get into a rack, how many racks in sequence we can get on a truck,” explained Roberson. “That drops into an Oracle database linked to a PC on the line. It calls for the next record and then instructs a PLC what the line is going to build next.”
The ILVS sequencing only begins when the colored appliqu? is mated to a piece of glass, but after the glass has been molded and hardware attached. “When the two come together,” Haygood told us, “A born-on date is created. It’s given a bar code and a traceable number that tells us everything about the part down to the lot numbers for the primer and urethane.” That number correlates back with Ford’s “Blend” number for the part and that ties back with the VIN number of the car for which the part was manufactured.
Blend numbers are sequential on the liftgates and control the sequencing of the parts into the racks and the racks into the trucks. The Blend number can be important if parts are damaged in transit or in Ford’s plants. If asked to, Dura can replace a single liftgate, a sequenced rack of liftgates or an entire truck of sequenced liftgates.
“We have had instances where the truck carrying the product to either plant has wrecked and we just pulled up the information and rebuilt the parts,” related Roberson.
In Abney’s opinion, “When you look at our ILVS portion of it, the quality record that we have, it’s been almost flawless. We’ve only had one or two dropped numbers since the time we started. If we were to do it again, we would probably mirror it and do it exactly the same way.”
As it happens, Ford’s next generation of SUV liftgates for these vehicles does not incorporate the body colored appliqu?s. So the ILVS system is scheduled to shut down in July 2005, but until then the folks at Lawrenceville will be handling glass with class.
More Stories
End-of-Life Vehicle Management Trends in New Zealand: What’s Next?
Fleet Management Made Smarter with Diagnostics Tools
Best Wheel Size for Off-Road Adventures: What People Get Wrong