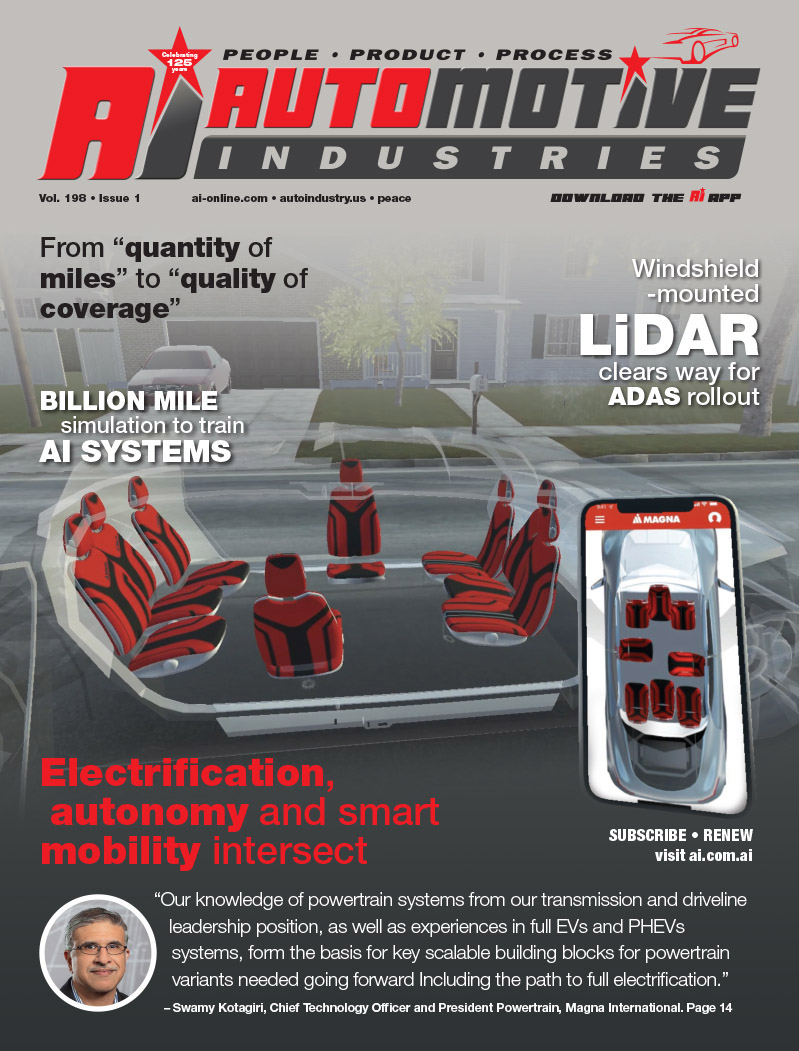
A pair of sixes and a 500 hp V-10 add up to a winning hand for BMW powertrain.
BMW has introduced three new engines, all to appear first in the 5- series range. First was the R6, a 3.0-L gasoline inline six that promised to be the first of a new generation; next a highly impressive “variable turbocharger” 3.0L diesel inline six; and finally the power unit for the new M5 sports sedan, a 5.0L V-10.
![]() |
At low revs (fig.1) the intake air flows through the large turbocharger (without effect) before it is compressed in the small turbocharger. As engine speed rises, the big turbocharger cuts in to pre-compress the intake air (fig.2). The air is then compressed with a high compression ratio by the small turbocharger. Only the large turbocharger is active at high revs (fig.3). At 4,500 rpm the power unit produced its maximum output of 272 hp. When the engine speeds reach the high end of the rev range (fig.4), the exhaust gas stream is only partly routed through the turbocharger. |
That is the reason for the biggest change in the new gasoline six, which boasts a bedplate, cylinder head cover and crankcase cast largely in magnesium alloy. Such alloys have a density roughly 30 percent less than the aluminum alloy previously used in most BMW engines. On the debit side, no one has yet developed a treatment or alloy of magnesium similar to the various ways of using aluminum alloy cylinder bores without ferrous liners, nor of reducing magnesium’s incompatibility with water.
That is why the crankcase-cum-cylinder block is a breakthrough technology in casting, being a mix of magnesium alloy and aluminum alloy. Hyper-eutectic silicon aluminum alloy is used in the form of a cast insert clothed — by casting the one within the other — in magnesium alloy. The insert contains cylinder bores, specially honed to marginally lower the surface aluminum, leaving the hard silicon in contact with piston and rings — a technique used by BMW and others for some years now. The top end of what are effectively aluminum liners carry the studs for cylinder head clamping. The insert also carries all the internal coolant passages, lost-wax-cast into the insert using polystyrene foam capable of producing relatively small diameter holes the length of the block. Its bottom end forms the upper half of the main bearing housings, emerging from the magnesium alloy to end at the crankshaft center line. The lower bearing housings are formed in sintered steel, cast into the magnesium alloy bedplate. Further weight is lost in the use of hydroformed camshafts.
On the power and efficiency improvement side, the R6 uses a second generation of BMW’s Valvetronic valve operating system, which takes the maximum working speed to 7,000 rpm, while avoiding the need for throttle butterfly valves for improved volumetric efficiency, said to raise fuel efficiency by 10 percent. The water pump claims to be a world first in production car engines, being electrically powered instead of engine-driven. Con-ventional pumps consume up to 2kW; maximum demand for the electric pump is 200 watts, and it is not always needed, for example during warm-up from cold.
Alternatively, it can be switched on when the engine is idle, to heat the car interior. This means only one ancillary belt drive. Fruits of all this are an engine weighing 355 pounds according to BMW’s measurement method, with a maximum power of 255 hp at 6,500 rpm, maximum torque of 221 lb.ft. constant between 2,500 and 4,000 rpm, and fuel consumption down by 12 percent.
Those power and torque figures for the gasoline 3.0L compare interestingly with the corresponding ones for the same capacity, if turbocharged, new inline six diesel engine. This produces 268 hp at 4,400 rpm, and 391 lb.ft. of torque at 1,500 rpm to substantiate BMW’s claim that this is “the most sporting diesel of all time.” They also point out that 268 hp from 183.6 cu.in. corresponds to 89.5 hp/L, the highest specific power output of any production car turbo-diesel.
How does it achieve such figures? Supercharging by means of an exhaust-driven centrifugal turbocharger has long been the essential method for allowing modern direct injection diesels, with, in unblown form, their up to 55 percent lower specific output, to rival gasoline engines. In Europe, there are V-6 diesels with two turbochargers, one to each cylinder bank. On the new BMW 3.0L inline 6-cylinder diesel, the Steyr-based BMW Diesel Competence Center in Austria uses two turbochargers, one small, one large, compressing air into the fourvalves- per-cylinder engine via an air-to-air intercooler. Both turbos are supplied by Garrett, the smaller blower’s lower rotor inertia and volume meaning, of course, that it responds more quickly and works at high boost for lower engine speed, while a large turbo delivers higher boost at higher exhaust flows for top-end power and torque.
Therefore, the two turbochargers are mounted on remarkable examples of interwoven aluminum alloy and iron casting, respectively forming the blower part of the inlet manifold and the turbine part of the exhaust. At low engine speeds, air passes through the large blower and is compressed in the small one, so that 95 percent of maximum torque is available from 1,500 rpm. The role of the large turbine increases with increasing speed, so that it pre-compresses to a swelling extent, maximum torque occurring at 2,000 rpm. At high engine rpm, the big blower obviously dominates.
From the exhaust viewpoint, the small turbine is upstream of the large one; gas can by-pass either turbine. From the inlet aspect, matters are reversed, with the big turbocharger upstream of the small one; air always passes through the large blower, but can largely by-pass the small one. All of this is controlled by three electro-pneumatic disc valves; the working of these is best understood from the four schematic diagrams.
![]() |
BMW’s new 3.0L inline 6- cylinder gasoline engine (above) has bedplate, cylinder head cover and crankcase cast largely in magnesium alloy. Such alloys have a density roughly 30 percent less than the aluminum alloy previously used in most BMW engines. |
![]() |
Finally, journalists were introduced to the new 5.0L V-10 M5 engine. This is a relatively conventional four-valves-per-cylinder design, albeit that it claims to be the first V-10 in a production car, and boasts a very highly specific power output of exactly 100 hp/L — 500 hp at 7,750 rpm for a 304.5 cu.in. swept volume derived from a markedly over-square 92 x 75.2 mm bore and stroke.
With a 90 degree bank angle, offset at crankshaft center height by 17 mm, the cylinder block is again a low-pressure gravity die casting in hyper-eutectic aluminum silicon alloy (17 percent silicon) with iron-coated pistons running direct on the machined faces of the precipitated silicon of the aluminum alloy bores. A racing-engine-style aluminum alloy bedplate has grey cast-iron inserts to act as supports for the 60 mm diameter by 28.2 mm wide main bearings. Pairs of connecting rods run on the five crank pins, which are offset at 72 degrees. Bores are spaced at 98 mm centers, keeping overall crankshaft, and therefore engine length, down as much as possible.
Although power control is conventional, with individual throttle butterflies for each cylinder, both inlet and exhaust camshafts are variably timed using BMW’s bi-VANOS system. The engine meets both Euro 4 and U.S. LEV2 emissions demands. This is helped by the highly sophisticated engine control unit, which has three 32-bit microprocessors and “ten times the memory capacity of the previous V-8 M5 engine.” The lubrication system recognizes that the M5 is capable of very high cornering rates, so it is a “semi-dry sump” design, with four oil pumps, and the sump itself designed to never run dry, to avoid any possibility of oil starvation. Given the unit’s maximum speed — 8,000 rpm — conventional audio-type knock detectors were not fast enough, so the engine uses ionic current detection via its spark plugs to provide fast enough individual knock detection for each cylinder.
To transmit all this power to the rear wheels, BMW has collaborated with German transmission specialists, Getrag, to design a remarkable seven-speed helical spur gear sequential automatic gearbox with a torque capacity of 405 lb.ft. to cope with the engine’s 384 lb.ft. of torque at 6,100 rpm. This can be left to its own devices, or “manually” shifted, according to driver mood. Its electronic control allows the provision of a “climbing assistant,” with which, coupled to brake control summoned by a prod of the brake pedal, the car simplifies hill starts by holding automatically until the driver accelerates away.
![]() |
The 5.0L V-10 will power the new M5. |
![]() | ![]() |
The 3.0L twin-turbo diesel uses a unique small and big turbo set-up to produce 268 hp from 183.6 cu.in., which equals 89.5 hp/L, the highest specific power output of any production car turbo-diesel. |
More Stories
End-of-Life Vehicle Management Trends in New Zealand: What’s Next?
Fleet Management Made Smarter with Diagnostics Tools
Best Wheel Size for Off-Road Adventures: What People Get Wrong