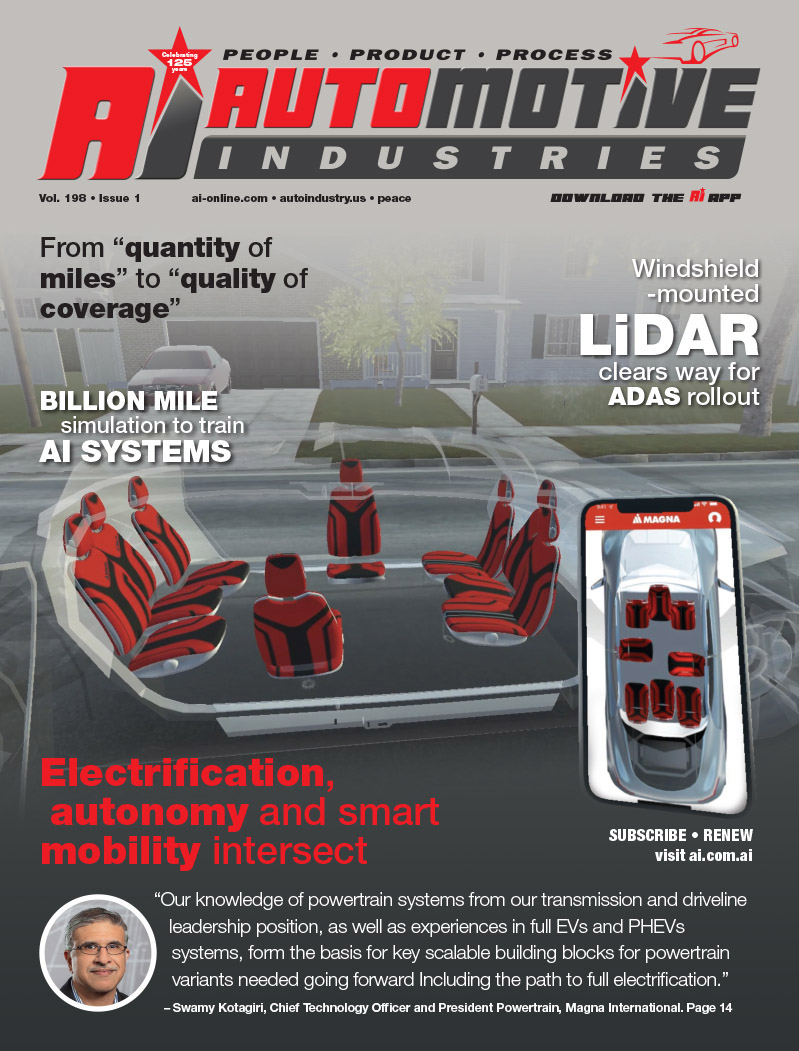
Henkel Corporation recently announced a new line of Autophoretic(R) Coating Chemicals (ACC) will be utilized by Parts Finishing Group (PFG) at their manufacturing facility in Chesterfield, Mich. The line contains ACC(R) 915, Henkel’s high-performance, durable, and heat-resistant product known as the “smart solution” because it reduces the number and complexity of stages involved in painting parts. PFG’s ACC(R) 915 is the largest line of its kind in North America.
The ACC(R) 915 lines at PFG can clean, rinse, coat and cure 16 loads of large and complex steel structural parts per hour. Furthermore, ACC(R) 915 is capable of coating complex mechanical assembly parts like engine cradles, control arms and trailer hitches. The line also features an optional acid pickling tank that cleans inorganics from parts. In addition, the product coats any ferrous metal it comes in contact with which enables companies like PFG to process a wider variety of complex geometries. ACC(R) 915 offers additional advantages, including:
* Does not coat non ferrous surfaces
* Maintains integrity when a part is treated twice
* Prevents “bridging” of hinges or bolt threads
* Delivers excellent corrosion resistance
* Provides superior edge corrosion protection
“Henkel values its partnership with PFG and is honored they chose to utilize ACC(R) 915 at their new facility,” said Chuck Schilling, director, Autophoretic(R) Coatings, Henkel. “Henkel hopes to maintain its trusted relationship with PFG and looks forward to future business opportunities.”
ACC(R) 915 was globally launched in 2003 and since then has received approvals at all major OEMs, meeting the material performance specifications for coatings. Several customers and OEM specifiers have already expressed interest to run parts on the line and to qualify ACC(R) 915 for use on large automotive components as well.
“Given the dramatic increase in commodity metal prices, Autophoretic(R) paint represents a more cost-stable and environmentally-safe option. Henkel’s new line of ACC(R) 915 is the solution to replace former methods for coating and plating,” said David Kalb, vice president, PFG. “The ability to reliably coat assemblies gives PFG an advantage in the industry. The process is very robust and provides outstanding first time quality.”
In addition to ACC(R) 915, PFG utilizes many Henkel metal pretreatment and adhesive products at its 12 production facilities in North America. Design production capacity is expected to reach 20 million square-feet of automotive components per year.
Henkel is the market leader in adhesives, sealants and surface treatments to the transportation industry. Backed by extensive design capabilities, a broad product range, specific application knowledge and technical expertise, the company delivers solutions to all segments of automotive development — automotive body, interior, chassis, electronics and powertrain production. Through powerful brands like Loctite(R), Teroson(R), Autophoretic(R), Bonderite(R), Frekote(R) and Multan(TM), Henkel provides significant economic and environmental advantages for today’s vehicles, making them safer, more comfortable and extending vehicle value.
More Stories
Venti Technologies Wins Multiple Pinnacle Awards for Innovation and Achievement in Technology
Launch of AltaScient.ai: New horizons for Risk and Sustainability Analytics
Expert Tips on Detailing a Car