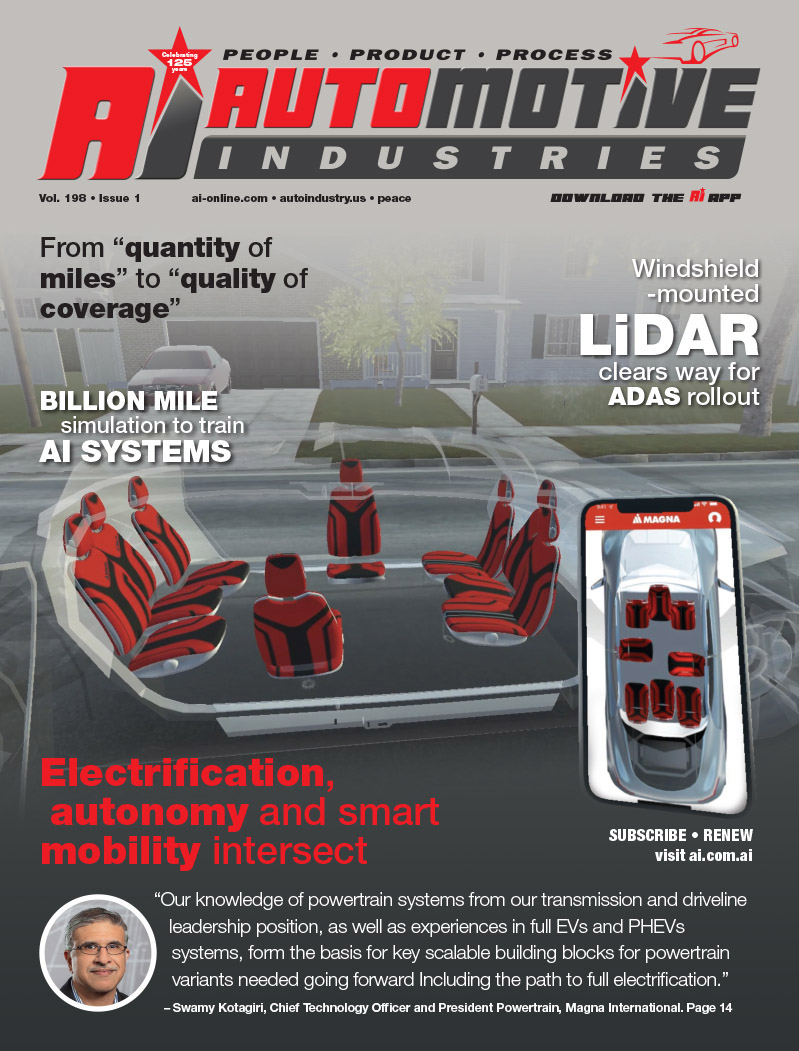
One year after helping to the launch the Global Engine Manufacturing Alliance (GEMA) in Dundee, Mich., Governor Jennifer Granholm returned, joining Chrysler Group executives, the UAW and GEMA employees to celebrate the grand opening of a second World Engine plant here.
The two state-of-the-art plants — GEMA North and GEMA South — are part of a five-factory global venture building a family of 1.8-liter, 2.0-liter and 2.4-liter engines jointly developed by DaimlerChrysler, Hyundai Motor Company and Mitsubishi Motors Corporation. When all five plants are fully operational, the combined project will be the largest engine manufacturing operation in the world. Annual production will reach 1.8 million units, including production sites in Asan and Hwasung, South Korea, and Shiga, Japan.
“Michigan is the global center for automotive innovation and excellence, and these engine plants show what can happen when state and local government support business to make our state competitive,” said Governor Jennifer M. Granholm. “My economic plan calls for investment in our workers and our schools to ensure that our workforce remains the best in the world so that we can continue to attract new automotive, alternative energy, life sciences and homeland defense businesses.”
GEMA represents a whole new business model for engine development — one that leverages the combined capabilities of its partners and economies of scale in order to generate breakthrough improvement.
“At the Global Engine Manufacturing Alliance, we’ve put the manufacturing processes in place to build four-cylinder engines that deliver exceptional performance, fuel efficiency, reliability and refinement,” said Chrysler Group Executive Vice President – Manufacturing Frank Ewasyshyn. “It’s no secret: the World Engine is the right product at the right time.”
Premium World Engine Features
The significant savings achieved in design, purchasing and manufacturing are going back into the product itself in the form of technology and refinement. Features such as variable valve timing, high-pressure die-cast aluminum engine block, forged-steel crankshaft and select-fit pistons, tappets and bearings are not typically found in entry-level, four-cylinder vehicles.
Engineers from DaimlerChrysler, Hyundai Motor Company and Mitsubishi Motors Corporation have used global volume bundling cost savings from the Global Engine Manufacturing Alliance to give customers valuable benefits. The World Engine is loaded with premium features including:
* Die-cast aluminum engine block
* Aluminum cylinder heads
* Intake manifold with flow-control valves
* Dual variable valve timing
* Direct-acting mechanical bucket tappet valve train
* Select fit pistons, bearings and tappets
* Isolated valve cover
* Damped oil pan
* Balance shaft module with integrated oil pump
To meet high DaimlerChrysler standards for sound quality and minimal noise, vibration and harshness (NVH), even in entry-level vehicles, Chrysler Group engineers took several unique measures. An isolated valve cover and a damped oil pan reduce sound at the top and bottom of the engine. A variety of select-fit parts minimize NVH. Engine idle smoothness is improved through the dual VVT technology and the flow control valve manifold.
In addition to these unique attributes, these engines will deliver world- class quality and durability. For example, through the involvement of all three automakers, durability testing for the World Engine exceeded 16 million customer equivalent miles.
Fuel economy is a key factor in the four-cylinder market, and the Chrysler Group continues to find ways to offer better performance in this area. These engines are targeted to raise the efficiency by five percent over the engines they displace. These technologies also enable the engine to meet the ultra- clean ULEV II emissions standards.
GEMA President Bruce Coventry credits the alliance’s practice of focusing exclusively on its core business as a key element in GEMA’s efficient operation.
“Our expertise and value to the customer is in the designing, high- precision machining and assembling of engine blocks, cranks and heads,” Coventry said. “This project will allow DaimlerChrysler to realize annual savings of $100 million and attain a leading position in the market for the world’s best four-cylinder engines. The Global Engine Manufacturing Alliance enables us to fully benefit from our strategic partnerships and achieve maximum economies of scale.”
GEMA bargaining-unit employees are represented by United Auto Workers Local 723, Monroe, Mich.; Region 1A.
Ground-breaking for the combined 1.2-million-square-foot, co-located plants began in April 2003.
Global Engine Manufacturing Alliance Joint Venture
The World Engine was co-developed under a joint venture between DaimlerChrysler, Hyundai Motor Company and Mitsubishi Motors for the Global Engine Manufacturing Alliance.
While Hyundai had the lead design responsibility for the base engine, the Chrysler Group and Mitsubishi made significant engineering contributions to the design. Through the involvement of all three automakers, durability testing for the World Engine exceeded 16 million customer equivalent miles. Additionally, partners have shared best practices and lessons learned from past and current experiences, resulting in improved refinement, quality and durability.
Chrysler Group engineering led the development of key technologies that will give its customers high-value benefits in cost-efficient engines. These technologies include intake manifold control valves, Dual Variable Valve Timing (VVT), both launching in the U.S. first in Chrysler Group versions of the World Engine.
By optimizing the partners’ strengths, global economies of scale and the latest practices in flexible teams and machines, GEMA aims to set a new benchmark in engine plant productivity.
GEMA and the Community
The Global Engine Manufacturing Alliance and the DaimlerChrysler Corporation Fund are contributors to the Dundee community, and support area activities including the Dundee Firefighters Association, the Dundee Food Service Fund, the Dundee Veterans Memorial, the Mayfly Music Festival and the River Raisin Jazz Festival in nearby Monroe.
At full volume, the Global Engine Manufacturing Alliance is expected to employ between 500 and 600, including hourly, salary and partner employees. Hiring will continue at a steady pace for the next 14 months.
Throughout Michigan, DaimlerChrysler employs 40,000, pays more than $3.9 billion in annual wages and provides more than $249 million in taxable income to the state.
Since 2003, the Company has invested $2.2 billion in its Southeast Michigan manufacturing operations.
DaimlerChrysler facilities in Southeast Michigan include the Chelsea Proving Grounds, Conner Avenue Assembly Plant, DaimlerChrysler Transport, Detroit Axle, Global Engine Manufacturing Alliance, Jefferson North Assembly Plant, Mack Engine Plants I and II, Mopar Parts World Headquarters, Mt. Elliott Tool and Die, National Parts Distribution Centers (3), Plymouth Road Office Complex, Quality Engineering Center, Sterling Heights Assembly Plant, Sterling Heights Stamping Plant, Sterling Heights Vehicle Test Center, Trenton Engine Plant, Warren Stamping Plant, Warren Truck Assembly Plant and the General Motors, DaimlerChrysler and BMW Hybrid Development Center.
More Stories
How Modern Power Management Enhances Connected Fleet Tech
Automotive Industries interviews Bahar Sadeghi, Technical Director, Car Connectivity Consortium (CCC)
Avery Dennison PSA tapes support rapid evolution of EV batteries