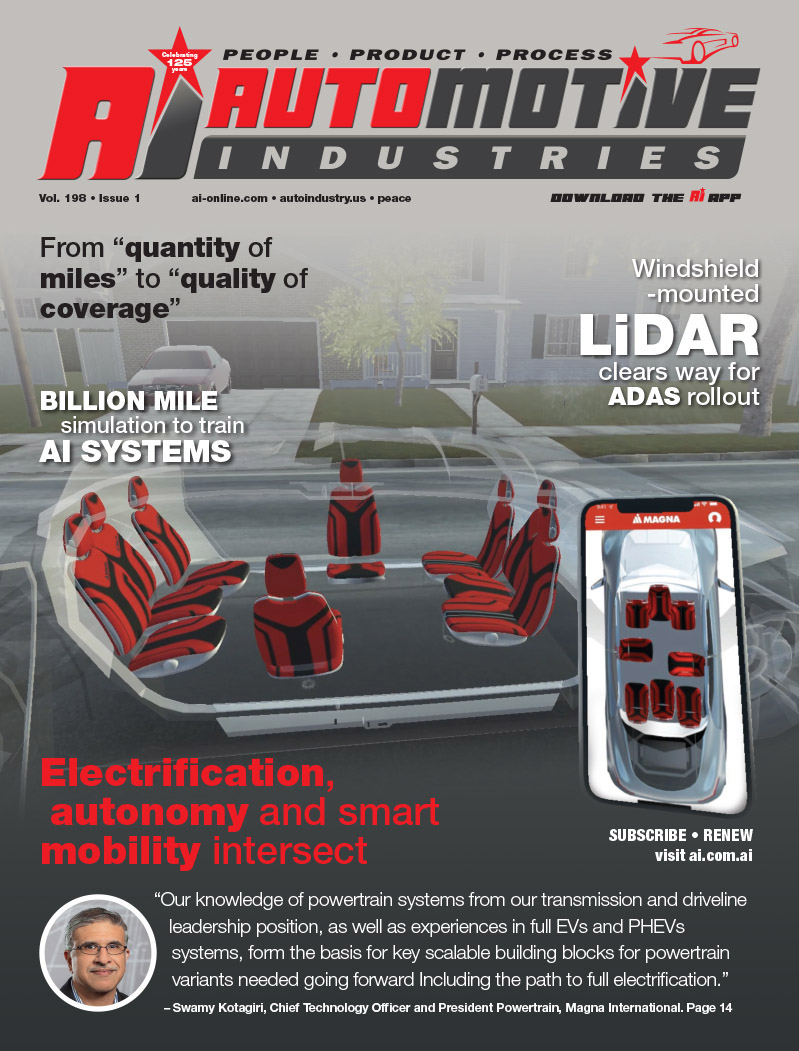
The Swiss Feintool Group is a leading technology and systems provider and a global components supplier whose major clients are companies in the automotive industry. Feintool’s four core competencies include fineblanking and forming technology, manufacturing of multifunctional precision parts, injection/insert molding technology and assembly technology. The company manufactures products for the automotive, electric tools, electrical apparatus and instruments, and telecommunications market segments.
Feintool’s total sales for 2005-2006 were CHF 501 million, up 2.8 per cent from the previous year’s CHF 487 million. Over 60 per cent of Feintool’s revenues comes from its traditional fineblanking and forming segment. This segment reported a sales increase of 4.7 per cent to CHF 319.2 million. The company attributed its growth to brisk sales of presses and to the increased development work at major car manufacturers. This has given rise to a short-term strengthening of the tool making business, and expansion of the fineblanking market segment in the long term. The newly developed Feintool HFAplus LT long-table press, featuring FFS technology (fineblanking-forming-stamping), has been well received by the market.
Fineblanking combines sheet-metal blanking and cold-forming – including bending, countersinking, semi-piercing, offsetting, coining and deep drawing. In a single process, fineblanking allows to produce parts to high standards of precision and surface quality, ready for installation with little or no post-processing. Even for complex multifunctional parts with high mechanical and dimensional requirements, fineblanking guarantees top reproducibility, excellent productivity and thus also remarkable cost advantages both for the parts themselves and in post-processing.
Feintool has been constantly developing fineblanking technology for 40 years, offering its customers an efficient service and cost advantages for an extremely wide range of metal parts. As the global market and technology leader, Feintool has developed and promoted not only the fineblanking process itself but the associated equipment and all related production processes, from parts engineering to integration in sub-assemblies.
Automotive applications are the principal domain of fineblanked parts. Examples from the power train segment include sprockets, chain links, exhaust flanges, clutch disks for automatic gearboxes, parking ratchet wheels, planetary gear carriers and many others.
Some of its automotive products include premium-quality automatic transmissions have up to 50 individual fineblanked parts. Their higher precision compared with conventionally manufactured parts makes a critical contribution to reliability and smooth, effortless shifting. The company also offers design consulting, prototyping, and just-in-time production delivery of the ready-to-install assembly.
Feintool also manufactures adjustable pedal groups consisting of several fineblanked parts. These parts are designed in a collaborative effort by the customer and its engineering department to ensure that they could be produced at the lowest possible cost ABS systems, higher engine power and demands for shorter braking distances require brake pad back plates that have challenging geometries and tight tolerances. “The special tool concepts that we have developed, and our close collaboration with leading system manufacturers, underscore Feintool’s competence as a top supplier.†In the automotive sector, over 500 customers can confirm that partnership with Feintool is key to corporate success.
Automotive Industries spoke to Christoph Trachsler, Head of Fineblanking Technology Division, Feintool Technologie AG.
AI: What in your view, is the future of the fineblanking and forming technology in the automotive industry?
The big advantages of the fineblanking and forming technology are the reduction or even complete elimination of post processes and the high precision and reliability. This helps the manufacturer to respond to the tremendous price competition and the continually growing quality specification. Feintool is also continually developing the fineblanking and forming process to enlarge the application rage. Based on this two factors we are convinced that fineblanking will continue to expand its position for high quality metallic parts for automotive applications.
AI: Please tell us a little bit about Feintool’s precision components for automated gearboxes?
Since many years Feintool is cultivating a close collaboration with different gearbox manufacturers. Therefore we are already involved in the development phase of new product series. This allows optimizing the construction for the production and weight reduction. A illustrative sample is the new 6-shift gearbox of ZF where approx. 50 fineblanking parts are used like different clutch plates, park wheel, levers, etc.
AI: How much of Feintool’s sales revenues are from the automotive segment?
The fineblanking equipment and part activities of Feinblanking makes over 80% of its revenue in the automotive industry. Since we have our own operations in all three big automotive markets, Americas, Europe and Asia we can adapt to weak market conditions in certain geographic areas.
AI: Feintool states to be the global technology leader for fineblanking and forming. Please explain how you approve this statement?
Right from the beginning when Feintool was founded 40 years ago, Mr. Bösch the founder had a strong focus on the development of the technology and not only to deliver the equipment. We run in US, Europe and Japan our own technology centers with tool shops where we develop, produce and test fineblanking tools for our own production and for our customers. Feintool has as well a long collaboration with several international well acknowledged Universities running numerous research projects. And our own fineblanking and forming plants keeps us in close contact to the daily challenges of the part manufacturers.
More Stories
Sonatus – The industry is shifting gears to software
Cybord warns of dangers of the stability illusion
HERE building trust in ADAS systems