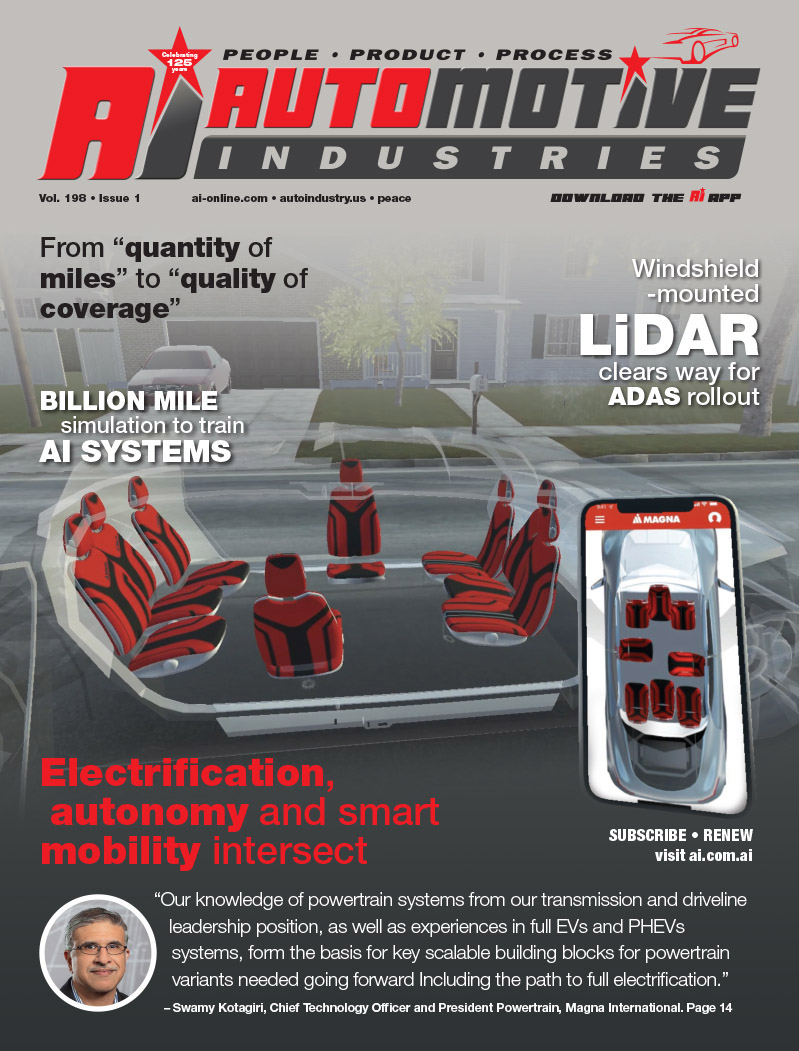
Almost since Scot John Boyd Dunlop made the first pneumatic tire in 1887 (followed by the first puncture), the search has been on for an alternative to air to fill tires.
Nevada-based Amerityre was founded in 1995 as the American tire Corporation. During its initial years, it developed and polyurethane foam tires based on the company’s proprietary polyurethane chemical formulations. Since the tires were fabricated using a closed cell polyurethane material, they could never go flat – which led to the registration of the Flatfree trademark. Today these tires are used in applications such as bicycles, wheelchairs, lawn and garden products, golf carts and commercial dollies.
In 1999 the company changed its name to Amerityre Corporation and continued development of the Flatfree technology. In 2003, it started working on polyurethane Elastothane elastomer technology. This technology allowed the development of a comprehensive line of tires and tire products based on polyurethane instead of rubber. These products include tire fill, solid tires, composite tires and pneumatic passenger vehicle tires.
People have been trying to manufacture flat free tires since the 1920’s. “Amerityre believes that it has managed to surmount the problems faced by others, such as heaviness, lack of shock absorbency, tendency to wear out quickly and excessive absorption of moisture,” says Richard A. Steinke, former-chairman and CEO.
In April 2004 Amerityre successfully completed testing to Federal Motor Safety Vehicle Standard (FMVSS) 109 with its Arcus run-flat design passenger car tire and in November 2007 successfully completed testing to the new FMVSS 139 specification.
Some of the company’s other products include Flatfree polyurethane foam tires for low speed and utility vehicle applications, environmentally friendly tire fill materials of both closed cell foam and elastomer polyurethane materials, to flat-proof rubber tires. The company also makes solid tires and composite tires as well as pneumatic tires.
Automotive Industries (AI) spoke to Gary Benninger, president and CEO of Amerityre Corporation.
AI: Tell us about the new developments with polyurethane-filled tires.
Benninger: Amerityre has developed two polyurethane tire fill materials: one is foam based while the other is an elastomer based solution. The foam, which is similar to the polyurethane foam used in our low duty cycle tires, is used for low to medium-load applications, while the elastomer is used in medium to high-load applications. The foam fill material allows users to reduce cost and weight compared to other tire fills currently in use. Amerityre’s tire fill materials have superior environmental properties when compared to most other tire fills that are in use today. All Amerityre materials can be recycled or disposed of without fear of environmental contamination. Other elastomer tire fills incorporate oils as fillers to reduce the cost of the product. These oils can cause serious environmental problems, since over time they can leach out of the fill material and damage the tire causing it to leak. Even worse, the oil filled material presents a serious disposal problem at the end of the life of the product. Some state and national governments are currently considering legislation that could ban use of the current oil filled materials due to their negative environmental impact.
AI: What impact do you think your Arcus flat-free tires will have on the tire market – how will it revolutionize the tire market?
Benninger: Additional testing by independent test laboratories has shown that the rolling resistance of the polyurethane Arcus tire is from 36% to 50% less than an equivalent rubber tire depending on the load and air pressure. This translates into an 8% to 10% improvement in vehicle fuel economy. Not only does this help reduce our dependence on foreign oil, but also reduces the amount of greenhouse gases discharged into our atmosphere. Some advantages for the consumer and the manufacturer are that it runs cooler for a longer life, its lower rolling resistance gives improved fuel economy, the single material pour reduces the possibility of separation, and it is a potential lower price due to reduced manufacturing cost. In addition when compared to a similar rubber tire, the polyurethane pneumatic car tire manufacturing process will require a lower capital investment, a lower tooling cost, less floor space , lower energy costs and lower labor costs, and will result in less scrap and waste.
AI: How much of the tire market do you think Arcus could account for?
Benninger: Amerityre believes that this technology will replace the rubber tire.
AI: What are Amerityre’s plans for the future?
Benninger: Amerityre is in discussions with potential strategic partners for the construction and installation of a pilot manufacturing facility capable of demonstrating its production capability with potential strategic partners. Our tire manufacturing technology brings significant cost reductions. Amerityre estimates that the capital investment required for a potential manufacturer to produce one polyurethane passenger car tire per minute will be less than US$10-million. This amount is one-sixth to one-eighth the cost of an equivalent rubber passenger car tire manufacturing line.
While companies are evaluating sample tires, Amerityre will focus on finishing the design and development of the manufacturing equipment required to produce the polyurethane road tire in commercial volumes. Amerityre is focused on five tire and tire product markets for its Elastothane polyurethane tire technologies.
AI: What progress have you made with auto companies for licensing of your technologies?
Benninger: The significantly lower rolling resistance of the Amerityre polyurethane car tire will allow cars equipped with such tires to achieve major fuel economy savings. Less fuel means less pollutants, including greenhouse gases and it also means less dependence on foreign oil. Who wouldn’t be interested? Currently one American automotive company as well as one major tire manufacturer are testing our tires. A number of other important companies have requested tires to test and we are fabricating these units now. Unfortunately we cannot get these units out as fast as we would like, since we are limited by our prototype production capacity.
The car companies may like the tire and want it for their vehicles. However, I don’t believe that they will be the ones that will ultimately license the technology. I believe it will be a tire company or a car parts supplier that has decided to manufacture tires, since the time to enter a new product line is when there is a major change in technology. Amerityre will partner with the car tire licensee to finalize the development of the manufacturing process and equipment for the car tire.
AI: What other innovative technologies your company is working on?
Benninger: Today Amerityre manufactures the best closed-cell polyurethane foam flat-free tires that you will find anywhere. This product is limited to applications where vehicle speed s are limited to less than 30 miles per hour. However, this market is larger than we ever imagined, since many of the vehicles used for transportation in other parts of the world never exceed these speeds. We are expanding this product line and increasing market penetration.
We have recently developed and demonstrated the manufacturing technology to make non-marking polyurethane elastomer forklift tires at the rate of one per minute and be able to achieve a selling price less than a comparable rubber tire. This is a significant achievement. We currently have several companies interested in this technology to take advantage of the manufacturing efficiencies we’ve demonstrated.
We have delivered the largest polyurethane pour machine in the world to our Chinese licensee, Quingdao Qizhou Rubber Co., Ltd., who will be using our technology and materials to retread large OTR tires. Also, we recently licensed Desert Research Technologies, of Tempe, AZ to use our technology to apply polyurethane treads to tires to be used for sand vehicles. These licenses permit others to use the technology that Amerityre developed to apply a tread material onto a new or used rubber casing.
AI: Do you see a big market for your technologies outside of the North American and European markets?
Benninger: We are being approached by people and companies from all over the world, including Europe, Asia, south America and Australia.
More Stories
Acoustic sensor systems and Fraunhofer measurement technology for in practical testing ͏
OSI Systems Receives $10 Million Order for Cargo and Vehicle Inspection Systems
Mitsubishi Electric Automotive America Launches Guardian Generation 3 Trial with Seeing Machines in North America