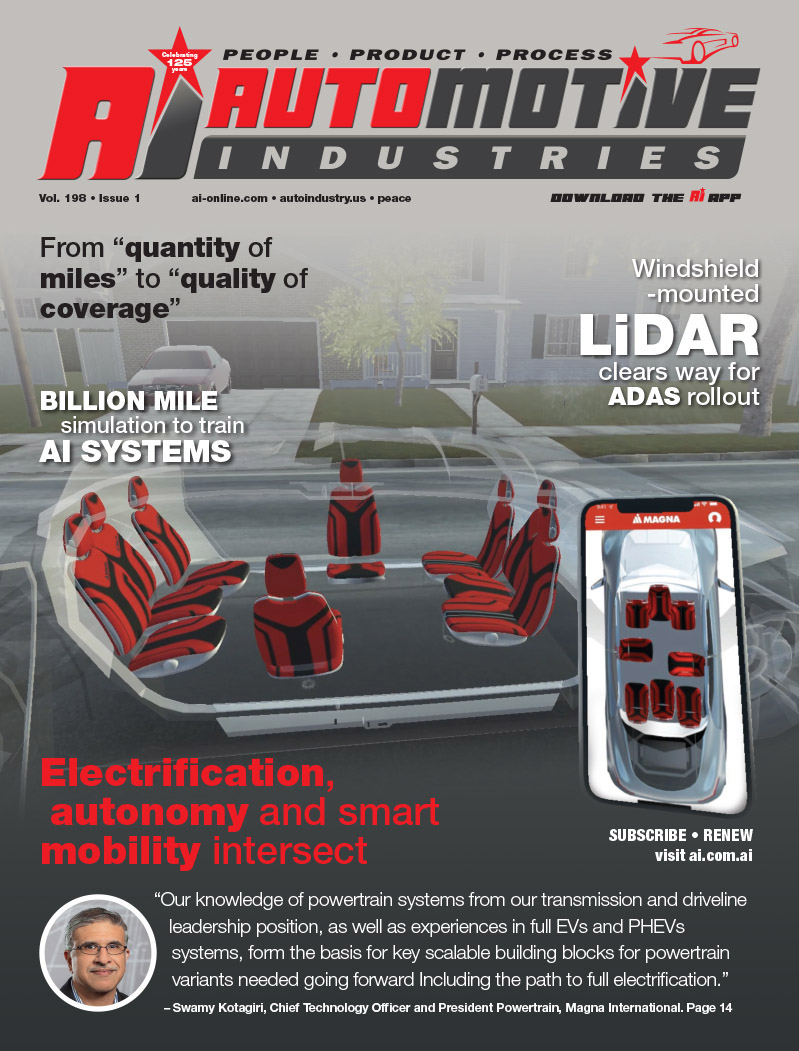
MMOG/LE is gaining popularity in the automotive industry as a recommended standard for materials and logistics to enhance collaboration and improve supplier performance. Developed by the Automotive Industry Action Group (AIAG) along with its European counterpart Odette International, MMOG/LE helps improve materials management and reduces costs for both OEMs and suppliers. This article introduces MMOG/LE as a continuous improvement tool for automotive and beyond.
Why is it the automotive industry can develop standards, but others can’t? Take, for example, Advanced Product Quality Planning (APQP), which is a framework of procedures and techniques used to develop products, particularly in auto. Additionally, automakers have been leaders in communicating with suppliers via EDI. Lean and just in time have been extended to sequenced scheduling and deliveries. Whatever the reason—the strength of the few large OEMs or the deep impact the Automotive Industry Action Group (AIAG) and the Original Equipment Suppliers Association (OESA) have in pulling these initiatives and standards together—the industry manages to implement standard processes better than any other. And now there’s another to add to the list: AMR Research finds MMOG/LE gaining traction and proving its ROI.
All about MMOG/LE
Published in 2004, the Global Materials Management Operations Guideline Logistics Evaluation (MMOG/LE) is a global standard for materials management based on agreed-upon business processes by automotive OEMs and suppliers. It includes a supplier self-assessment, identification of gaps, and appropriate action items to fill those gaps for continuous improvement. The benefits are significant:
• 85% reduction in premium freight
• 80% reduction in obsolescence costs
• 43% reduction in inventory carrying costs
• 20% reduction in data entry time
Workgroups from AIAG and Odette International developed a common set of global guidelines and a self-assessment tool that allows companies to rank their material planning and logistics performance and identify gaps for continuous improvement toward best practice within the industry. MMOG/LE assigns three levels of supply chain proficiency, with OEMs such as Chrysler, Ford, PSA Peugeot Citroen, Renault, and Volvo, requiring many of their suppliers across regions to use the tool for improved performance, albeit in different ways.
MMOG/LE comprises six chapters, with 206 criteria to determine the level of plant performance:
• Strategy and Improvement
• Work Organization
• Capacity and Production Planning
• Customer Interface
• Production and Product Control
• Supplier Interface
Who is using MMOG/LE today?
Automotive suppliers that needed to comply with OEM requirements were early adopters. For example, the above mentioned OEMs typically require MMOG/LE compliance for new, problem, and high-volume suppliers, with potential ones needing it to simply get in the door. The initiative is spreading across geographies, with Ford, Renault, and Volvo requiring it across all geographies for specified suppliers.
MMOG/LE has gained popularity in emerging markets, as suppliers see it as an opportunity to reduce risks, improve supply chain compliance, increase delivery and long-distance performance, and, most of all, become an attractive long-term partner to OEMs. Regional industry associations in Brazil, China, and Romania have also become involved.
A typical MMOG/LE engagement starts with training and building a team to do the assessment. The self-assessment and gap analysis includes completion of a comprehensive spreadsheet. A plant walk-through and interviews with functional areas confirms and validates the scores. The answer sheet enables companies to find continuous improvement opportunities and create an action plan to improve scores. Results are reviewed with senior management for prioritization, resource, and, where needed, budget allocation. Finally, the customer needs to certify the self-assessment score.
The OEMs are particularly focused on a couple areas when auditing Tier 1 suppliers:
• Management commitment
• Capacity planning
• EDI integration into ERP and automatic processing of data
• Ability to interface with Tier 2 suppliers, especially those in emerging markets
• The Improvement Plan
• Quality scores
Training is provided by AIAG, Odette, local industry groups, and QAD, an ERP provider prevalent among automotive suppliers. QAD is a participating member in MMOG/LE and, on behalf of AIAG/Odette, has provided training and assistance with audit preparation and process improvement in China, Russia, India, Poland, and the Czech Republic.
The benefits?
A midsize auto supplier in China used MMOG/LE and was able to identify some problem areas to fix, which resulted in a 50% reduction in raw material and finished goods inventory, a perfect score for delivery, decreased premium freight, and improved quality. Most importantly, it obtained new customers.
What about the OEMs? Ford has seen a 15% supplier delivery improvement, with 90% of suppliers reporting MMOG/LE level A. Communication is better, there are fewer shutdowns, and customer satisfaction has increased. Cost reductions came from lower safety stock, better floor-space use, material labeling, part tracking, and shipment loading. Chrysler has enjoyed a 54% delivery improvement, with 85% of suppliers rated level A experiencing similar benefits. Renault suppliers using MMOG/LE provide a 91% service level versus 80% from others that don’t.
MMOG/LE for other industries
With supply chain risk a top priority in global organizations, our research finds that, in order to mitigate these risks, companies are focused on improving supply chain visibility as well as looking to multi-sourcing strategies and performance-based collaborative relationships with suppliers. But many companies struggle to execute a sound supplier development program or even sustain the initiatives over a period of time.
A tool like MMOG/LE facilitates this by providing measurable objective data for supplier improvement. It’s essentially a continuous improvement tool to facilitate improving delivery performance and gaining control of processes and the supply chain. With clear benefits in reduced inventory, freight, rework, line stoppages, and lead times, it’s no wonder MMOG/LE is starting to get visibility in universities and high schools as a training tool. It’s also getting visibility in other industries, especially hospitals, construction, A&D, and chemicals.
Future articles will provide further insights into MMOG/LE. In the meantime, we would love to hear your thoughts and ideas—are you using MMOG/LE, too? Contact me at jbarrett@amrresearch.com
More Stories
How to Create the Ultimate Off-Road Vehicle Garage: A Practical Guide
How Diesel Pickups Are Outperforming Gas Trucks on Tough Jobs
Essential Steps To Help Your Vehicle Retain Value