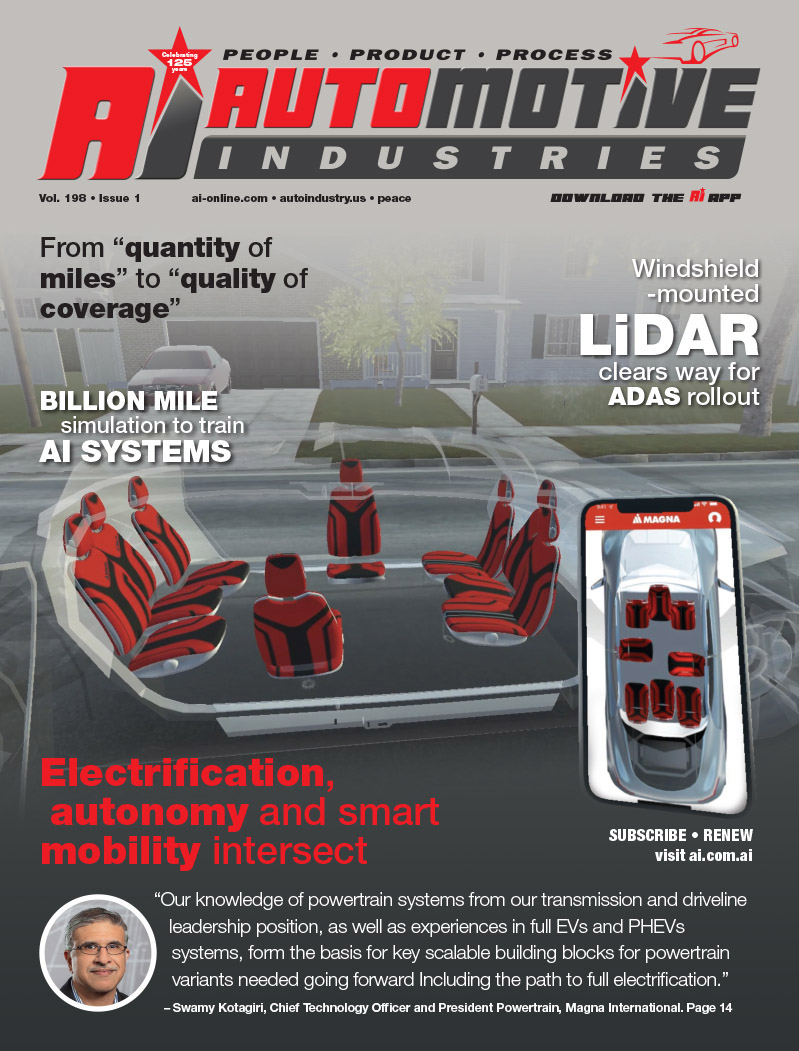
With auto sales down as much as 40 percent, it can feel to some like the industry is coming apart. But a “revolution in fasteners” may soon help bridge the gap to greener vehicles, while increasing sales and lowering recall and warranty rates.
“We’re at the beginning of a fastener revolution in automotive,” says Ray Genick, Director of New Business Development and former VP of Engineering at Emhart
Teknologies, a leader in the design and creation of unique assembly technologies. “It’s being driven not only by a need to lower recall and warranty costs, but also to raise fuel efficiency while reducing weight and environmental impact.”
A new report, which profiles Emhart Teknologies and other industry leaders, forecasts a growing automotive fastener market to reach $12.2 billion by 2012.
“Automotive fasteners assume high significance owing to the increasingly complex nature of vehicular designs, which is expected to necessitate stronger, improved and durable fasteners,” states a news release for “Automotive Fasteners: A Global Strategic Business Report,” published by Global Industry Analysts, Inc., one of the world’s largest market research publishers.
Failure of fasteners is one of the leading causes of vehicle recall in North America and Europe, and improved fastener technology will be part of the solution, according to a release for the report.
The typical threaded joint, produced by a standard nut and bolt, has existed since the 19th century and is no longer adequate for many of the 21st century problems the automotive industry is facing, such as the need for greener vehicles.
The problem is that when a fastener loses its clamp load, it no longer does its job and safety, recall, or warranty issues occur. Locking devices from wires and washers to chemical and drypatch adhesives are commonly added to retain clamp load. While adding weight and complexity, however, these methods do not always hold up under shock, vibration, or temperature extremes.
An overdesign ‘belt and suspenders’ mentality in automotive design has prevailed, for instance, putting 8 bolts on an exhaust manifold when 4 might do. This has led to big, heavy, fuel inefficient cars that consumers will increasingly turn from in today’s cost, energy, and environmentally conscious climate.
While green technology beckons, much of it still isn’t ready for prime time.
Hybrid cars, which pair a traditional gas engine with advanced electronics, are gaining acceptance but are still too costly for many consumers. All-electric vehicles are hampered by battery cost, battery life, and inadequate electrical grids. Fuel cells, which release energy converting hydrogen to water, remain in development and lack a reliable means of distributing hydrogen fuel.
One green technology, however, is already proving itself.
“Of all the fuel-saving technologies, clean diesel is the one that’s most ready to go right out of the box. Diesels already dominate some European markets….” states a recent BusinessWeek article titled “Get Ready for Less Boring Green Cars.” Clean diesel burns
low-sulfur diesel fuel in direct-injection engines.
“Clean diesel will be the bridge technology to all-electric and fuel cell powered vehicles,” agrees Genick of Emhart Teknologies. “Compared to conventional gas engines of equivalent displacement, its engine torque is 35-40 percent higher, its fuel mileage almost double in smaller engines, and its emissions much less.”
But clean diesel puts added strain on fasteners due to its added torque in the drivetrain and added heat and vibration in the turbocharged powertrain and chassis.
To assure joint integrity in these critical areas while preventing safety, warranty, or recall issues, automotive engineers are finding a solution in an innovative fastener called Spiralock.
Traditional locking fasteners do not address a basic design problem with the standard 60-degree thread form: that the gap between the crest of the male and female threads can lead to vibration-induced thread loosening. Stress concentration and fatigue at the first few engaged threads is also a problem, along with an increased probability of shear, especially in soft metals, due to its tendency toward axial loading. Temperature extremes can also expand or contract surfaces and materials, potentially compromising joint integrity.
Engineers, however, have successfully attacked these challenges while reducing component weight and enabling re-usability with the innovative Spiralock locking fastener. This re-engineered thread form adds a unique 30-degree wedge ramp at the root of the thread which mates with standard 60-degree male thread fasteners.
The wedge ramp allows the bolt to spin freely relative to female threads until clamp load is applied. The crests of the standard male thread form are then drawn tightly against the wedge ramp, eliminating radial clearances and creating a continuous spiral line contact along the entire length of the thread engagement. This continuous line contact spreads the clamp force more evenly over all engaged threads, improving resistance to vibrational loosening, axial-torsional loading, joint fatigue, and temperature extremes.
The Spiralock locking fastener has been validated in published test studies at leading institutions including MIT, the Goddard Space Flight Center, Lawrence Livermore National Laboratory, and British Aerospace. It has been used in extreme fastening applications with virtually no chance of recall: from the main engines of NASA’s Space Shuttle; to the Saturn Cassini orbiter and Titan Huygens probe; to medical implants, artificial limbs, and heart pumps.
“The Spiralock fastener’s ability to retain clamp load under extreme shock, vibration, and temperature with less weight, complexity, and maintenance makes it a natural choice for automotive, especially clean diesel,” says Genick. “It retains clamp load even with dissimilar exotic materials, such as composites and titanium, which is important in reducing vehicle weight.”
Weight savings also come from reducing fastener size or number with an equal or better safety margin compared to fasteners with the standard 60-degree thread form, according to Arlindo Marques, Director of Global Engineering for Spiralock.
“The key is Spiralock’s full contact along the entire engaged length of the thread,”
says Marques. “This reduces thread galling, or microwelding, especially in the heat-resistant nickel alloys becoming important in automotive. It enables fastener reusability up to 50 times, simplifying installation and maintenance. And it makes the thread form self-centering, which improves performance and eases the balancing of high-RPM diesel and turbo systems.”
In automotive, the locking fastener is already used in applications ranging from ring gears, torque converters, and chassis assembly to exhaust manifold joints and axle, turbine, or transmission housings. For diesel engine applications, it has been adopted by Caterpillar and Mack Trucks.
“We brought Spiralock into the Emhart family because we believe there’s so much potential in automotive,” says Genick. “While the industry is challenged, there’s opportunity to accelerate out of the downturn with more powerful, higher mileage, lower emission, clean diesel technology. Innovative fastener technology like Spiralock can help the industry make the transition, while helping to lower recall and warranty rates.”
Emhart Teknologies, known for total vehicle innovation in the auto industry, is involved in everything from vehicle exterior trim through the powertrain and suspension. It owns Spiralock, which is used for design challenges in a wide range of industries including automotive, heavy truck, aerospace/military, medical, food processing, agriculture, construction, rail, and oil drilling. Production changeovers to the fastener are typically quick and seamless, often requiring just an exchange of traditional nuts, wire inserts or simply drilling out and re-tapping existing parts stock that have unreliable standard tapped holes.
For detailed test data, including comparative graphic loading characteristics or photoelastic analysis/load vector comparison animation, visit Spiralock at www.spiralock.com; email slinfo@spiralock.com; call (800) 521-2688; fax (248) 543-1403; or write to Spiralock at Madison Tech Center, PO Box 71629, Madison Heights, MI 48071.
More Stories
SikaBaffle® technology helps customers build lighter, stronger, safer, quieter and greener vehicles
How Modern Power Management Enhances Connected Fleet Tech
Automotive Industries (AI) Newsletter April 2025