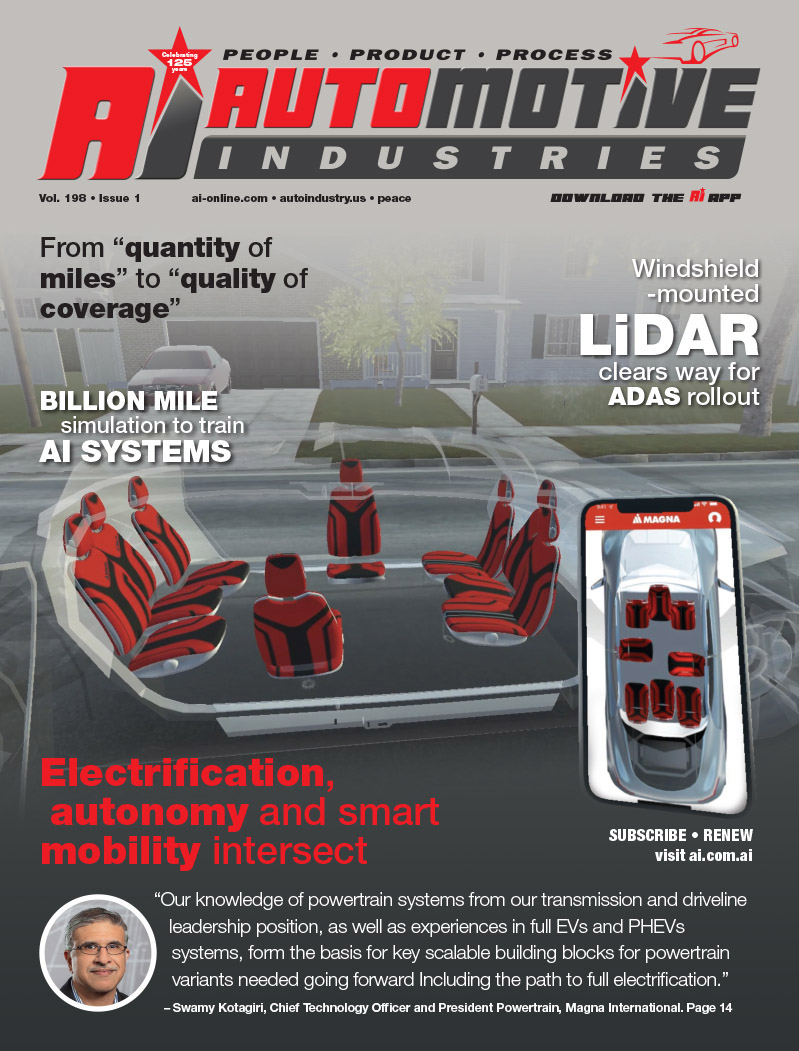
PROJECT PROSPECTUS:
With the race for increased fuel economy at the priority apex for car buyers and manufacturers worldwide, vehicle OEMs have made strong efforts to reduce weight in their products for improved mileage. The instrumental benefits of composites in this effort are increasingly being recognized as Molded Fiber Glass Companies (MFG: Ashtabula, OH) was recently awarded The Process Innovation Award at the American Composites Manufacturers Association’s (ACMA) Composites+Polycon 2009 show (Tampa, FL) for its Nano-enhanced Sheet Molded Composite (SMC) one-piece molding for an automotive Rear Trunk Assembly (tub).
Initially designed for the 2009 Pontiac Solstice Coupe, MFG’s proprietary SMC is formulated with nano-enhanced technology and FRP (fiber-reinforced polymer) to achieve structural low-density composites in a one-piece molding for the trunk compartment. Overall, the material yields a special SMC with a specific gravity of 1.5 which reduced mass, increased strength and delivered a lower cost by increasing production rate and volume while maintaining quality. The technology is also utilized in the 2009 Chevrolet Corvette Coupe and Corvette Z06.
The original one-piece composite “tub” design reduced mass and tooling costs as it replaced multiple metal stampings while providing storage, attachment points for outer body panels, hardware attachments for electrical components, and air ducts. In addition to lowering mass for improved fuel efficiency, the trunk assembly’s composite makeup is corrosion resistant − a key feature for the vehicle’s underside which is exposed to harsh environments.
With dimensions of 51 inches wide by 36 inches long and up to 24 inches deep (130 cm by 91 cm by 61 cm), the nano-SMC tubs weigh in at 9 kg each. All materials on the rear trunk assembly were the first to be tested, approved, and taken into production by General Motors.
NANO TECHNOLOGY/PROPERTIES:
MFG’s Nano-fill based SMC was developed to replace low-density, bubble-filled SMC. Overall, the Nano technology’s physical performance produced a lower density of 1.5 (6-to-8 lbs. less weight than conventional SMC) while improving the assembly’s mechanical strength by 10% versus conventional SMC. In addition to the nano material’s higher performance and reduced mass, it improves bond adhesion capabilities by 25%-30% with a 2-component adhesive over the bubble-filled SMC.
The SMC nano-technology is comprised of MFG’s proprietary process and material additives utilized from Southern Clay Products (Gonzales, Texas) called Cloisite® . These additives consist of organically modified nanometer scale, and layered magnesium aluminum silicate platelets. The silicate platelets that the additives are derived from are 1 nanometer thick and 70 – 150 nanometers across and are surface modified with an organic chemistry to allow complete dispersion into and provide miscibility with the resin. Properly dispersed, the additives have been proven to reinforce thermoset resins by enhancing flexural and tensile modulus while lowering CLTE (Coefficient of Linear Thermal Expansion).
According to Peter Emrich, MFG’s VP of Technology, “The nanoclay processing is important to material properties. The nanoclay particles look like a deck of cards that break up into individual plates (exfoliation). MFG’s process provides a stable, exfoliated paste material.”
FRP-NANO BENEFITS/RESULTS:
GM Material Engineer Kestutis Sonta noted, “The one-piece, rear compartment FRP/Nano tubs provided essential mass reduction to assist in enhancing fuel efficiency. Also, since less material was used, there was less cost as it’s typically purchased by the pound.”
Sonta also expressed plans for future vehicle programs stating, “The innovative material technology represents a successful, cost-effective, lightweight alternative to other exotic materials. We’re currently exploring future applications that would benefit from these performance properties.”
CONCLUSION:
With President Obama’s recently announced “clean energy economy” plan to raise auto gas mileage standards and cut the emission of greenhouse gases, the advantages of nanotechnology and composites present an innovative manufacturing technology that can make many products stronger, lighter, cleaner, more precise, and ultimately, more cost/fuel efficient.
MFG continues to expand the possibilities of its nano-technology process for SMC and LCM (Liquid Composite Molding) via its state-of-the-art pre-placed reinforcement technology named PRIME (Pre-Placed Positioned Reinforcement Insuring Manufacturing Excellence). Utilized for more than a year for Corvette parts, PRIME is an SMC and LCM process that uses proportional control of fiber deposition (based on tool velocity and modulated air flow) during forming to control loft and reduce energy.
MFG CORPORATE PROFILE:
Comprised of fifteen key entities, 14 in the U.S.A. and one in Mexico, Molded Fiber Glass Companies (MFG) has been a pioneering leader in optimizing resins and fiber reinforced polymer (FRP) materials and continues to build strength through focused diversity in providing superior composite material solutions worldwide. Established in 1948, MFG is a family owned and managed company distinguished for its commitment to technical superiority in composites use and manufacturing.
Each ISO Certified MFG entity is responsible for acquiring and advancing the technologies necessary to best serve its customers via continual improvement of existing processes and materials. This commitment to the advancement of reinforced plastics and composites is reflected in the diverse markets MFG serves including; wind energy, automotive, heavy truck, defense, construction, material handling and water treatment. MFG provides each market a variety of composite material systems that provide high value, high quality products and manufacturing services for associated applications.
More Stories
Automotive Industries (AI) Newsletter April 2025
Bangkok International Motor Show 2025 – The Talk of Sensuous Automotive
Earn GHG reduction values through MOL Pure Car Carrier “Book and Claim (B&C)” service