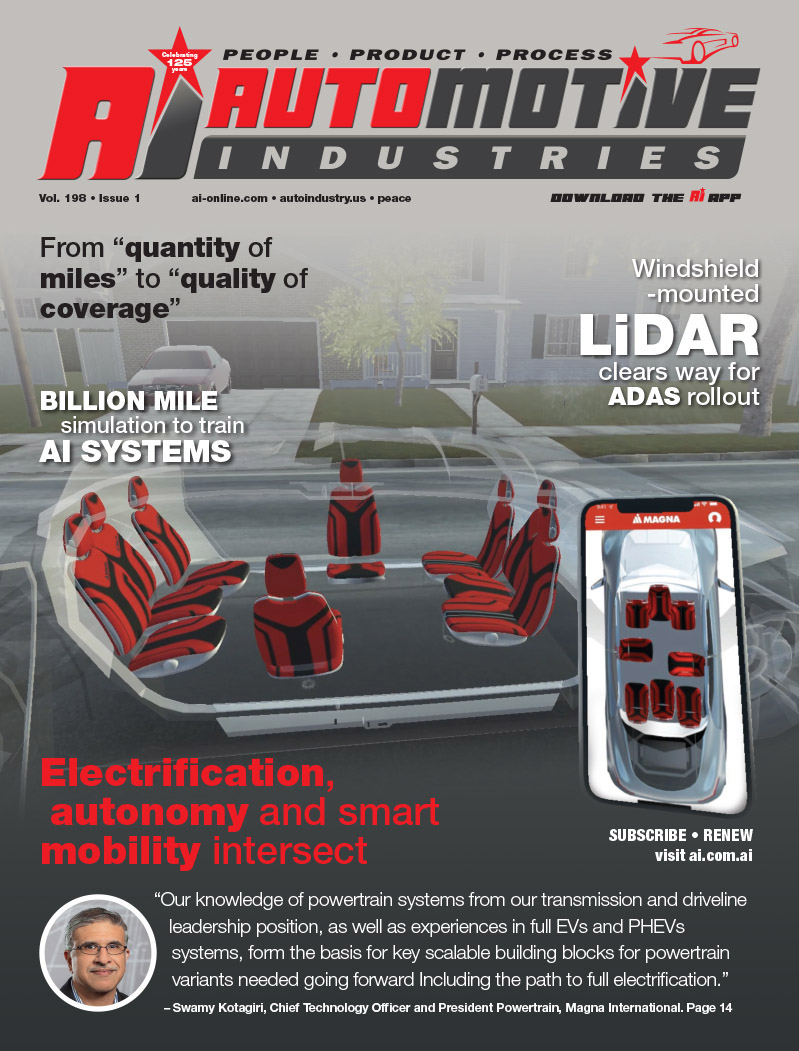
An internationally recognized automotive accessory supplier, New Zealand-based Best Bars, sets a sound example of just how important quality assurance and customer satisfaction are when it comes to succeeding in the competitive business world.
Best Bars manufactures, imports, exports, and distributes an extensive range of automotive products, including towbars, towing accessories, nudgebars, sportsbars, protection bars, running boards, ladder racks, and more. With an elite business-partner roster made up of leading automotive distributors, and a broad export market, Best Bars relies on precision and accuracy in order to uphold the company’s high standards of efficiency and productivity in the motor industry.
Established in 1982, Best Bars attributes its decades of success in large part to its sincere dedication to customer satisfaction. Continuous innovation in terms of operation and design, coupled with a focus on overall quality, has allowed the company to emerge as a leader in its field.
Best Bars identified the need to improve the process of assembling “fit kits,” or packages of nuts, bolts, fasteners, and plastic accessories that are included with customer orders to complete the assembly process with their vehicles. At the time, Best Bars had been using a manual process which required staff members to physically count 200 or more fit kits per day, some of which contained more than 50 individual parts. Naturally, human error would allow for mistakes in the fit kits, which in turn could have serious safety implications for the end user. For instance, when assembling a towbar fit kit, including the wrong fastener could cause the towbar to eventually malfunction during use.
“It is imperative that a customer receiving our products receives a 100 percent correct and quality-checked fitting kit,” said Stephen de Kriek, CEO of Best Bars. “When completing a product installation, there is nothing more frustrating to a customer than having one or two nuts or bolts missing.”
System of Scales Provides Needed Solution
Best Bars decided to incorporate an advanced counting system, comprised of several sophisticated scales integrated with specially designed software linked to a fit kit database. During fit kit packaging, the software would recall the particular combination of parts from the database and automatically set up the scale network to complete the job. In the end, the counting system was finalized with more than 10 scales that are networked together and link to the product database. Ideally, this system would eliminate error, increase efficiency, and improve fit kit quality and customer satisfaction.
Upon designing the needed software specification, the company tested and compared a number of scales, eventually deciding on the OHAUS Scout® Pro.
“Several scale companies were asked to provide hardware recommendations and pricing,” said Andy Cashen, Managing Director of Ansutek Commercial ltd., OHAUS’ New Zealand distributor, describing the intricate process of designing the new counting system. “We nominated the OHAUS hardware as the best hardware to be utilized in the weighing platform.”
Cashen explained that the OHAUS Scout Pro, with features including USB communication ability, proved to be the ideal weighing device for interacting with the software. He found that based on features, reliability, connectivity, and user simplicity, the OHAUS Scout Pro was a leader in its market.
The OHAUS Scout Pro offered the convenience, portability, and unique set of features that Best Bars needed to improve its assembly process. Aside from the mentioned USB interface accessory, the OHAUS Scout Pro features advanced precision and durability, making it ideal for Best Bars’ industrial environment. A range of capacities and readabilities allowed Best Bars to customize their plan and integrate the scales with their specially designed software.
Productivity, Quality, and Satisfaction Increase
Upon initiating the integrated counting system more than two years ago, Best Bars has seen a number of improvements in the overall function of fit kit assembly.
“We identified this as an area through which we could offer our clients an advantage over our competition,” de Kriek said in reference to the updated counting system. “We were very pleased with the result. We now very seldom, if at all, receive notification of a fit kit issue.”
The integration of a better parts-counting system using the OHAUS Scout Pro has improved Best Bars’ processes, profitability and customer satisfaction. Improvements to one key part of the company’s assembly process have yielded strong returns.
Headquartered in Pine Brook, N.J., OHAUS Corporation manufactures an extensive line of high-precision electronic and mechanical balances and scales that meet the demands of virtually any weighing need. The company is a global leader in the laboratory, industrial, and education channels as well as a host of specialty markets, including the food preparation, pharmacy and jewelry industries. An ISO 9001:2008 manufacturer, OHAUS products are precise, reliable and affordable, and are backed by industry-leading customer support. For additional information, contact OHAUS Corporation at 973-377-9000, or visit the Web site at www.OHAUS.com
More Stories
How to Create the Ultimate Off-Road Vehicle Garage: A Practical Guide
How Diesel Pickups Are Outperforming Gas Trucks on Tough Jobs
Essential Steps To Help Your Vehicle Retain Value