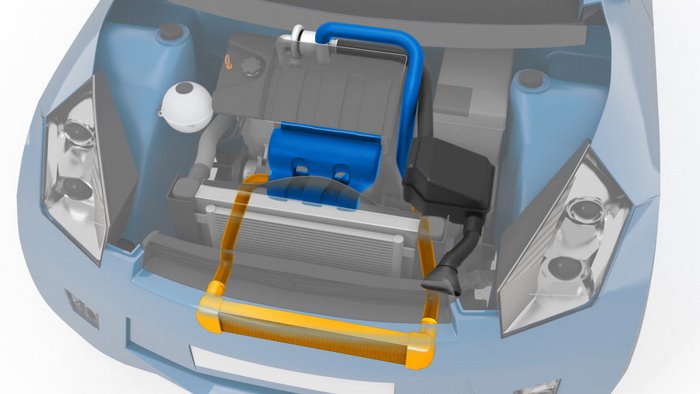
Intake manifolds with integrated charge air coolers increase engine responsiveness, because air volume is reduced by over 40 percent. Further the integration cuts over 20 percent parts, weight and costs. Failure probability is shrinking also. Tightness, even air distribution, temperature and bursting pressure durability as well as different heat elongation of metal and plastic turned out to be a big challenge for Röchling Automotive´s engineering and manufacturing.
Integrating the heat exchanger into the intake manifold cuts package and air volume of the intake air duct by over 40 percent. This improves engine agility considerably. “You can feel that the engines have more punch. This is due to the shorter intake duct. Some kind of lag has always been characteristic for turbo charging by exhaust gas. This is almost entirely eliminated now. Besides air volume there are also cost, weight and parts count, which are reduced by over 20 percent each,” explains Marco Barbolini, product manager at Röchling Automotive. “After all the charge air tube is shortened by over 50 percent on the hot side. On the cold side it is skipped totally. As well as the connectors. As far as the charge air cooler is concerned the headers on both sides are obsolete. Therefore, a bunch of quite expensive parts is eliminated. With better driving dynamics and engine efficiency on the upside. Nevertheless, realisation was a challenge. But in the meantime this double pack is regarded to have proven feasibility, competitiveness and reliability.”
Assembling plastics and metal is always critical in the bonding area, especially if it has to be absolutely tight. The seating of the heat exchanger has to be exactly plane in order to stay tight at highest pressures. During cooling of the moulded part tensions can be caused by direction and distribution of enforcing fibres as well as by uneven temperature levels. This triggers warpage and in the end not precisely plane parts surfaces. “You need comprehensive know how in mould flow simulation, tool construction and injection moulding machine control to meet the minimum tolerances demanded for this parts planarity,” explains Ludwig Huber, engineering director at Röchling Automotive.
Even air distribution is optimized with powerful CFD software when an intake manifold is designed. Computational Fluid Dynamics processing is yet manifoldly more complex with a n integrated heat exchanger than for a simple intake manifol! d. At th e same time the request for balanced air distribution is even higher. It is not only about even air volume but also even air temperature for each cylinder. No matter which temperature prevails in ambient air, engine and coolant.
The high temperatures are on par with high pressures, yet both of them are not steady, but varying according to changing engine power output. Röchling Automotive´s engineers simulated the dynamic loads with elaborate processing models for the intake manifold as well as for the heat exchanger. Pressure change tests proved the design. “At the and of the day, we had verified all extreme scenarios. Without weight penalty,” Barbolini remembers. “This shows how much you can achieve with intelligent geometry. At each point enforcement and thinning follow as accurately as possible the load vectors there. Exactly as in nature, for example in birds bones.”
The rapidly changing ambient and operating conditions add to the stress of the plastic ho using and the aluminium heat exchanger due to their different, material specific heat elongation. “We compensate for the distinct elongation coefficients largely with an air gap,” says Barbolini. “Yet, the problem remains on the contact areas. After this has also turned out to be feasible, the trend towards this basic design is gaining momentum everywhere. This was a real breakthrough.”
More Stories
How Modern Power Management Enhances Connected Fleet Tech
Automotive Industries interviews Bahar Sadeghi, Technical Director, Car Connectivity Consortium (CCC)
Avery Dennison PSA tapes support rapid evolution of EV batteries