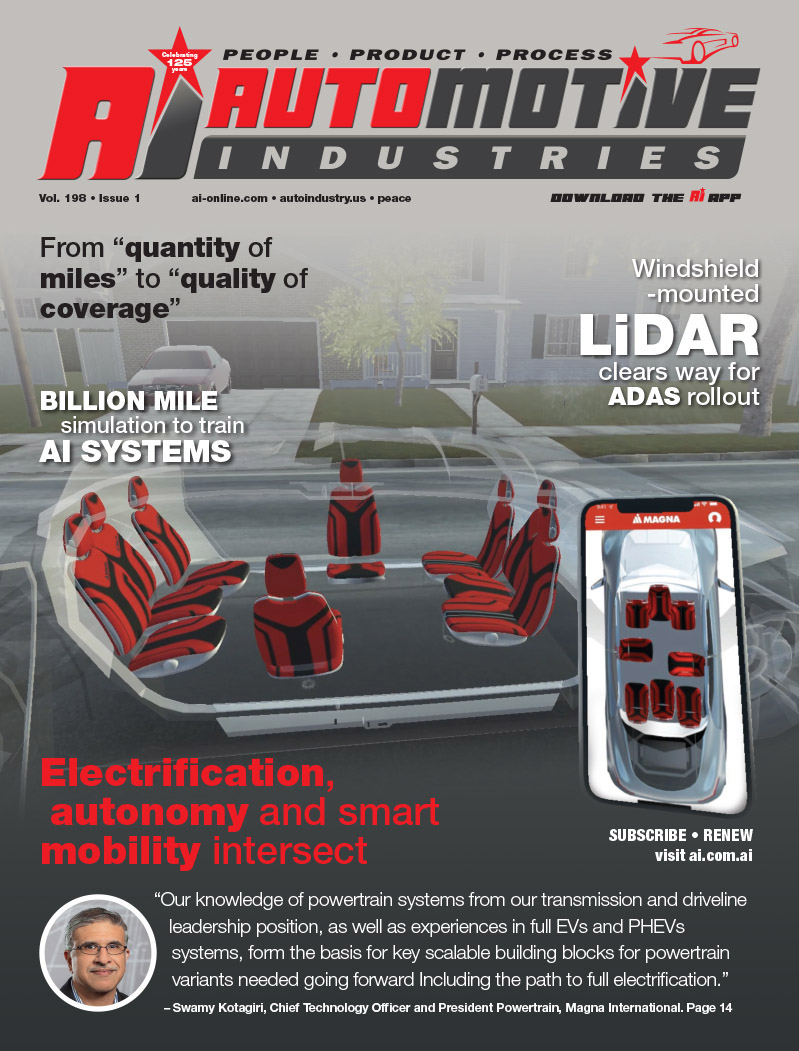
A newly-developed range of high heat, low color distortion and low emission additives for thermoplastics has been developed to meet ever-stricter regulations, together with greater customer expectations.
The range was developed by South Korean firm Songwon Industrial, which produces polyvinyl chloride, polyurethane, polyester diol, antioxidant, alkyl phenol, biphenol, flocculants, super-absorbent polymer, agrochemical, tin intermediary, and other products. Songwon has manufacturing facilities in Ulsan, South Korea, where it started producing additives for the PVC industry in the mid 1960’s and antioxidants for the polymer industry in the mid 1980’s.
Songwon says market demands for improved performance and durability in end-use applications have driven the requirements for total service life and average operating temperature to new levels. Existing systems based on phenolic antioxidants and thioesters are in danger of not meeting more stringent requirements that are being introduced. There is already a need for materials such as filled or unfilled Polypropylene (PP), which are typically injection molded in thicker wall sections, to offer longer life cycles. Environmental, Health and Safety standards have also become stricter, with a key focus on the reduction of emissions.
“Songwon has created a significant win-win solution. We outperform current industry standards by more than 50%, and are able to meet these standards with reduced additive loadings. This, in turn, generates the additional benefits of low color distortion – often a problem when higher loadings are required. Lower loadings have a direct and positive effect on emissions,” says Klaus Keck, manager global applications and technical service community at Songwon.
Songwon has steadily been increasing its global presence and capacity. In 2010, the company announced the expansion of its antioxidant capacity from 55,000 tons to 70,000 tons a year.
This will be on stream from August 2011. The expansion is the result of the consolidation of the Songnox 1076 production into Songwon’s new fully backward integrated Maeam plant. “In 2006 we made a commitment to customers to drive reliability of supply and competitiveness through economies of scale and backward integration from a state of the art facility. Maeam was dedicated to producing key antioxidants, with critical intermediates fully integrated into the manufacturing process. In 2009, we took backward integration a step further by investing in an isobutylene plant based on proprietary technology. In order to enhance our competiveness and to consolidate our position as partner of choice for the polymer industry, we have now decided to integrate the production of Songnox 1076 into Maeam. This will create the best possible manufacturing platform for this product in line with our strategy to maximize backward integration and economies of scale. We believe that Maeam is now the biggest plant in the world dedicated to key anitoxidants based on a fully integrated manufacturing process,” says Jongho Park, chairman and CEO of Songwon Industrial.
Songwon has also been extending its global product range to include Hindered Amine Light Stabilizers (HALS), Benzotriazole UV Light Absorbers, and key niche antioxidants to serve specific application needs. Globally, the company has increased its presence by establishing subsidiaries in other countries. Songwon International has been operational from July 1, 2006 covering EMEA and Americas. Songwon China, a wholly owned subsidiary of Songwon Industrial, and based in Hong Kong, is the investment arm into an increasing number of Songwon entities in China. Songwon Shanghai Trading is the main operational company.
Songwon Baifu Chemical is a joint venture with Tangshan Baifu Chemical to manufacture and sell thioester antioxidants. It will have a fully backward integrated capacity of 6,000 tons. A full analytical laboratory is being built in Shanghai, and will be operational by the end of 2011.
“We are very pleased with the progress we have made in China in such a short time. The commitment we made to customers in China has been recognized and we are being rewarded by growth and long term business commitments. This is driving the need for extended services, such as the analytical laboratory, and the extension of our product range. Songwon Baifu will be influential in China and will provide world class thioester antioxidant products to our other key regions. We are also establishing long term relationships with home based suppliers to ensure a secure stream of raw materials, intermediates and finished products that meet our high standards and competitive market position,” said Park.
Automotive Industries (AI) asked Dieter Morath, executive vice president sales, and member of the Songwong International Group Executive Committee, what new applications for thermoplastics in motor vehicles are now possible with the development of the new range of additives?
Morath: Over the medium term, the requirements for more durability of PP parts in automotive plastics engineering will continue to rise – in under the hood applications in particular. The new Songwon High Heat OPS Range offers our customers a complete toolbox for designing tailor-made solutiosn to meet the requirements of longer service life and/or durability under harsh conditions. Sophisticated automotive plastic parts may well be replaced by PP as the performance standards increase.
The range of products also addresses the goal of the automotive industry to reduce the overall level of volatile organic compounds. The new Songwon High Efficiency OPS Range on the one hand, aims at base stabilization packages already up-streams allowing lowered concentration levels in e.g. PP resins through more efficient stabilization packages. On the other hand this new range offers also concepts for compounding applications respectively formulations targeting lowered emissions of VOC and/or smell/odor during service life.
UV Packages
In addition Songwon does also offer new stabilization concepts for achieving superior UV protection, both for exterior and interior automotive PP applications. The new Songwon UV OPS range have been designed in particular for protection of surface properties like gloss and surface crazing under severe weathering conditions, when containing fillers, or other additives like flame retardants etc.
Recycling
Songwon offers complete process and stabilization knowhow to the entire recycling value chain that systematically collects and rework plastic waste streams, and by adding tailored Songwon Recycling OPS Range finally, up-grade a former waste stream to a new automotive PP compound with remarkable durability close to prime materials.
AI: How does Songwon work with OEMs to develop new components?
Morath: To define projects and solutions for next generation cars matching future demands with recycling industry to achieve close to prime quality performances / material properties and support set up of quality assurance due to variability of secondary polymer streams
work with compounding companies integrated and external to solve issues related to requirements not covered by the big polymer producers
AI: What other new products and applications are in the pipe-line?
Morath: Carbon fiber sheet technologies for automotive light weight engineering
This is foreseen as a future mega trend in automotive car body engineering and production. It addresses the need for continuous reduction of weight and consequently CO2 emissions re. consumption of petrol. On the other hand this is a long way to go when considering the current process cost re. operating cycle cost compared with the today’s state-of –the-art steel and aluminum based manufacturing. But we as Songwon believe that the development path forward again, only become shaped together with the polymer additives industry.
We work on new solutions together with the resins producers to make these necessary process & quality innovations happen.
Light –weight materials
In order to achieve weight reduction, the (wall) thickness of parts gets less to a point where (rigid) foam replaces complete solid parts. As thinner parts in general have a lower service life than thicker parts (oxygen migration) and additionally the complex foaming processes exclude “traditional” stabilization packages, new stabilizer solutions must be developed in order for this trend to be implement-able.
E-Mobility
This is another mega trend we may anticipate for the automotive design & engineering process with plastics. For certain car series the E-Mobility Century might change the requirements under the hood completely because the classical combustion engine will become phased out over time – either partly, or in combination with an electric motor, or with other alternative engines, or even completely. At the same time the need for light weight engineering will become accelerated and only be achieved with plastics. In other words: The demand for plastics engineering in automotive will again become accelerated! And only with the essential specialty chemicals called antioxidants. Count on Songwon!
AI: What are your strategies in Asia, the Americas and Europe with regards to the automotive market?
Morath: We are a global player, and in our dealings with global players we have learned that the fundamental drivers are the same everywhere. We monitor trends and issues, and proactively find solutions.
More Stories
Venti Technologies Wins Multiple Pinnacle Awards for Innovation and Achievement in Technology
Launch of AltaScient.ai: New horizons for Risk and Sustainability Analytics
Expert Tips on Detailing a Car