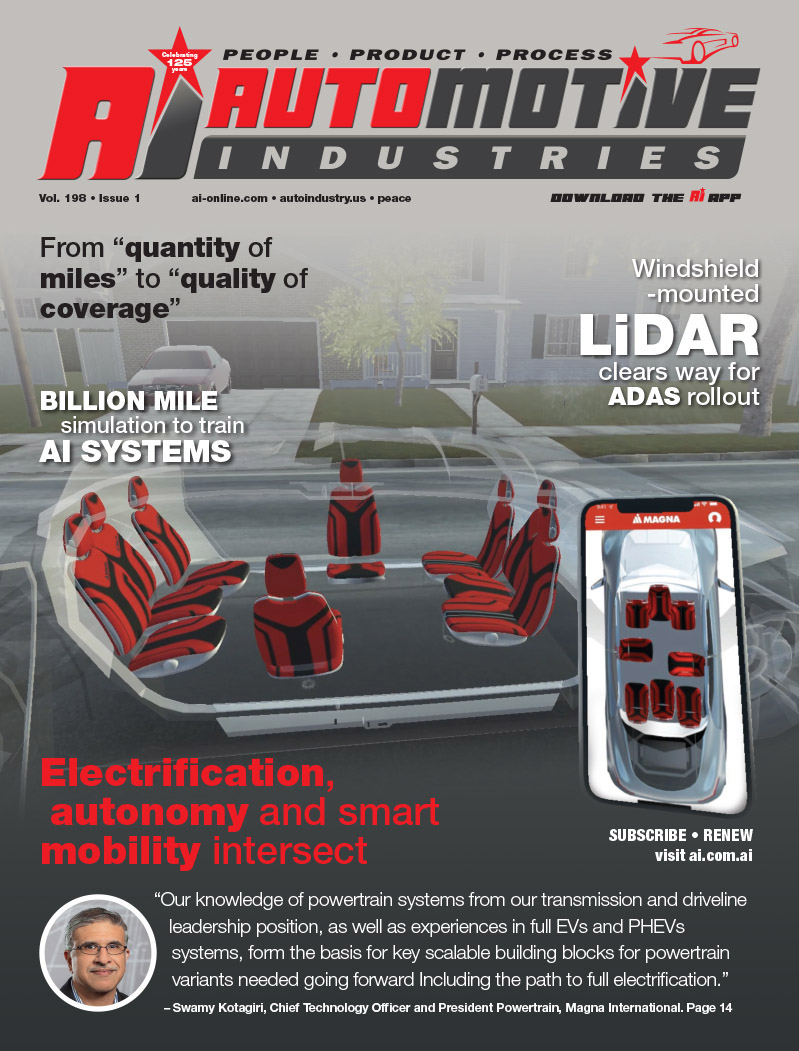
While editing the articles in this edition and speaking to some of the technology and thought leaders in the industry, I was struck once again by level of technology and innovation that goes into a modern motor car.
Yes, the industry has always been innovative, but the level of technology was such that as a youngster I could strip an engine, put in new rings and pistons, put it back together and my friend could continue driving the car (a VW Beetle) for thousands more miles. Or, in the days of points, use a bit of water paper to smooth the contacts to get me through the month until I could afford to replace them.
At about the same time – which was not so long ago – technological breakthroughs came in the form of pointless ignition, and the use of aluminum mostly to reduce corrosion, but also to save weight on some of the more up-market vehicles. It was only in the early 1980’s that we saw the first computers under the hoods of mass market vehicles. And, as colleague Andrew Jackson points out, it was not that long ago that a skilled mechanic could work on most vehicles, only having to send them out for specialist work on the electrics. OEMs protected their dealers by introducing special tools which ensured that hobbyists and independent mechanics could not turn strategically chosen bolts and screws. Ways were found around that, of course. Today’s equivalent are the computer fundis who develop tools and software needed to essentially hack into the computer systems that control most of today’s vehicles, but I digress.
Highly taxed fuel in Europe meant research and development on the Continent focused largely on delivering more horsepower from smaller engines and improving consumption. In the US, thanks to California, the focus was on emissions. In the process, transmissions went from three or four-speed to five-speed, and the industry started replacing heavy steel with lighter materials. None of this was leading edge stuff. You did not routinely find the best and brightest engineers and scientists knocking on the doors of the motor industry.
All of that has changed. In virtually every field, the industry is pushing the envelope of science and design. Plastic, in its many different forms (mostly not called “plastic”), is lighter, stronger, more malleable, and easier to recycle than ever before. Chemists are working with auto engineers to push the boundaries of performance and design ever further. We are even seeing grams shaved off the weight of upholstery fabrics in order to save weight. They are working in a crowded field. Suppliers of traditional metals have not left the building, and they too are exploring what today are the outer limits of particle structure.
Then we come to the heart of the vehicle – the power train. A relatively new entrant in this field is the Information Technology (IT) industry. It brings with it the ground-breaking thinking that made cellphones connect the world, and which has subsequently turned them into highly sophisticated mobile information hubs. Here is an industry unencumbered with legacy thinking. Why should a car not be able to plan ahead to determine what mix of battery and combustion power it is going to need to get to a destination? Previously we thought that was the driver or navigator’s job.
Fine-tuning the energy to drive the vehicle forward is another exciting field. Break-throughs are being made in battery technology, biofuels, and the efficiency of the more conventional gas-fired engine. As important is the support structure required to manage and deliver millions of Watts of power to electric vehicles, to transport gas and biofuels, and to manage traffic. Again, these breakthroughs are being made by a new generation of innovators who enjoy unprecedented support from the OEMs, governments and civil society. On their shoulders rests the responsibly of keeping the world moving in an environmentally and economically sustainable way.
More Stories
Acoustic sensor systems and Fraunhofer measurement technology for in practical testing ͏
OSI Systems Receives $10 Million Order for Cargo and Vehicle Inspection Systems
Mitsubishi Electric Automotive America Launches Guardian Generation 3 Trial with Seeing Machines in North America