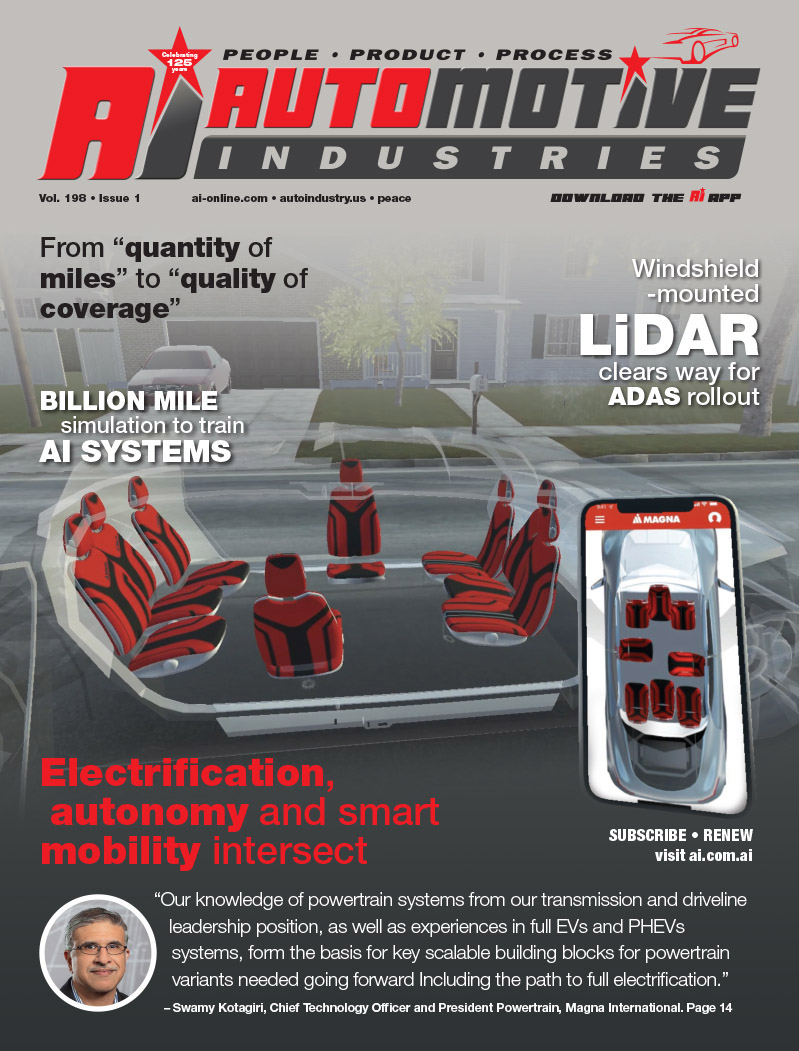
The trend by automotive manufacturers towards replacing traditional materials with lightweight options such as plastics is good news for companies such as Polyscope Polymers, a major producer of styrene maleic anhydride (SMA) copolymers and compounds.
The company’s XIRAN® brand of SMA/ABS compounds is being used in growing volumes by many of the world’s major original equipment manufacturers (OEMs). XIRAN® is being used by the automotive community due to its functionality and low shrinkage/warpage. It can withstand high temperatures, retains its shape, and is easy to use.
“Our compounds can be found in dozens of models produced by most of the major OEMs around the world. This percentage is likely to grow as the size of plastic components gets bigger – and this is where SMA-based compounds have the winning advantage,” said Peter Tackx, Director Sales and Business Development, Polyscope Polymers in an earlier interview with AI.
“The use of our plastics is an opportunity to design components with lower glass content and thin walls without losing any of the finished part properties. Less glass means a lower density and therefore a direct weight saving, less wear and tear for tooling and machinery and thus less system costs. The extreme adhesion performance allows foaming and painting without surface pretreatments,” says a company statement.
“OEMs have begun differentiating between material costs and system costs. In the constant drive to reduce costs, the industry has realized that the lowest cost materials are not necessarily the cheapest to use. Take the savings in glass reinforcing by replacing traditional plastics with XIRAN® compounds. That gives an immediate weight saving, while reducing wear on tooling and machinery. Or the fact that foam and paint can be applied directly onto SMA compounds. That saves on the system costs in terms of time, energy and materials required to prepare other materials, such as plastics and metals,” explained Tackx.
Until recently, XIRAN® compounds had the downside of creating a poor visual impact in the finished part – which has restricted their use to hidden areas. Polyscope says, however, that it has “made a major breakthrough in glass-filled XIRAN® systems by developing a solution without a major cost impact that makes the material suitable for visual areas as well.”
XIRAN® SG is the company’s glass reinforced engineering plastic for injection molding applications with high heat resistance, and is particularly suited for painted or foamed parts. Typical glass fiber reinforcement loads range from 10 to 40%. The interaction between the functional maleic anhydride groups and glass fibers produces an unmatched property profile and has heat resistance of up to 125°C or higher.
The extra rigid grades are mainly used for injection molding dashboards and also other automotive applications such as painted mirror housings, windscreen demisters, front end carriers, air intake grilles, underbody shields and sunroof frames – basically all applications where one would need good heat resistance combined with an acceptable impact profile.
Automotive Industries (AI) asked Patrick Muezers, Managing Director, Polyscope Polymers, to tell us how the company’s motto – “Fresh Thinking. Great Products” is reflected in its research and product development. Muezers: As a young and dynamic company, we are constantly looking to produce innovative materials for new applications. We are thinking out of our comfort zone into new and exciting materials. We recently used SMA in combination with PP to check its possibilities and the first commercial injection molding trial (on an instrument panel) with this SMA modified short glass PP compound was a big success (from processing, dimensions and aspect point of view).We are not only fresh thinkers when it comes to new materials, but also when it comes to new concepts, like the use of recycled ABS and SMA in our core applications.
AI: What makes your products unique in terms of automotive applications?
Muezers: XIRAN® is a functional and amorphous copolymer that can be used in many different compounds. The amorphous nature of the material results in very low shrinkage and very low warpage. Tool design is very straight forward, and injection molders can skip the prototype phase due to the highly predictable molding process. The functional groups secure a good adhesive bonding with glues and other materials (like PUR foam in an instrument panel). Also, painting and plating of XIRAN® parts is very cost-effective. There is no need for flame treatment or the use of expensive, time consuming and eco-unfriendly primers
AI: Please tell us how your company has worked on the challenges thrown up by XIRAN® (such as visual impact) and how have you overcome these shortcomings?
Muezers: Polyscope is always keen to develop new products and processes together with the experts in the field. In the case of visual appearance, we are working closely together with different companies that are active in rapid heat-cool mold devices.
AI: Do you see XIRAN® being used for more visible applications? Please give examples.
Muezers: We are seeing progress but, as always, automotive developments take a long time to materialize into actual commercial success. The need to closely work together with innovative OEM producers is also very important in this respect.
AI: What are some of the new automotive applications for XIRAN® that you can share with us?
Muezers: The newest automotive applications can be seen in large parts that require a low warpage, like big open sunroof frames or retainer rings. Also, foamed and skinned door panels are now being developed in XIRAN®. In these applications we see the added value of our XIRAN® pr oducts used at its full potential.
AI: How has Polyscope expanded its scope of business recently across different geographical regions?
Muezers: Polyscope is actively present in three key geographical regions: Europe, the Americas and Asia. We follow the Tier 1s and OEMs into the region where they want us to be present (like South Africa)
More Stories
How Modern Power Management Enhances Connected Fleet Tech
Automotive Industries (AI) Newsletter April 2025
Will Cars Function Like Smartwatches in the Future?