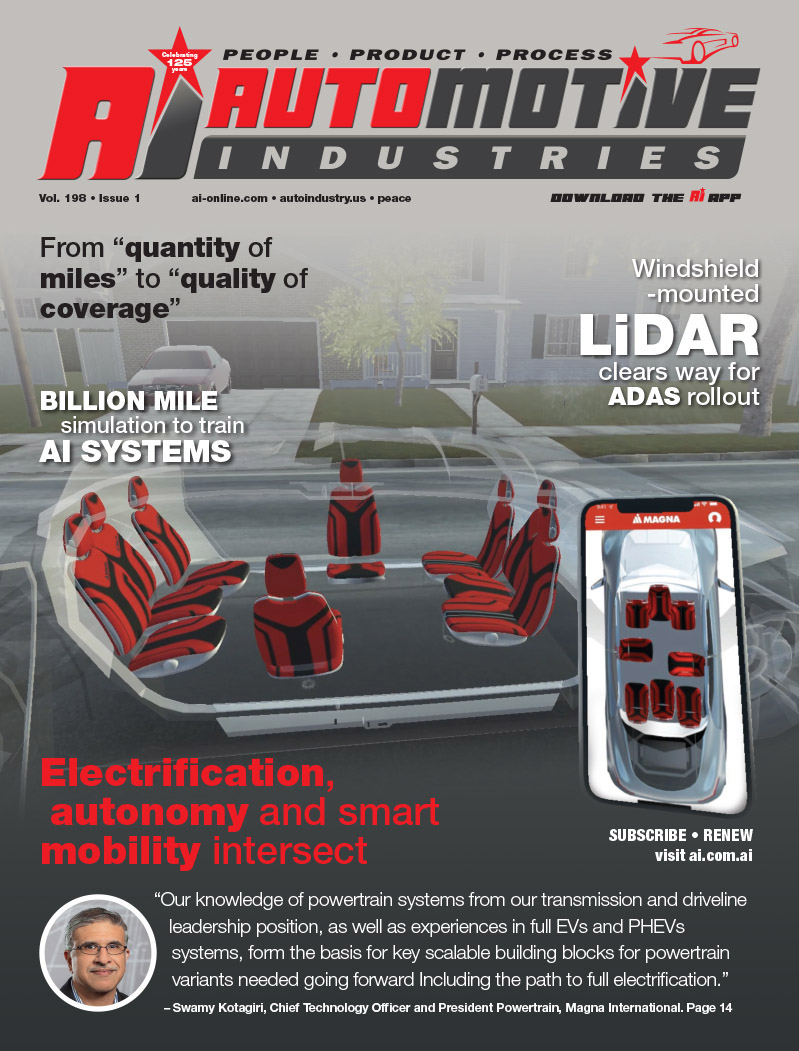
3-D printing is entering the mainstream of automotive design and manufacturing, and is fast making an impact.
“Additive manufacturing is a truly disruptive technology exploding on the manufacturing scene as leading companies are transitioning from ‘analog’ to ‘digital’ manufacturing. Additive manufacturing uses three-dimensional printing to transform engineering design files into fully functional and durable objects created from sand, metal and glass.
The technology creates products layer-by-layer. After a layer’s particles are bound by heat or chemicals, the next layer is added and the binding process is repeated. It enables geometries not previously possible to be manufactured. Full-form parts are made directly from computeraided design (CAD) data for a variety of industrial, commercial and art applications,†says global 3-D printer ExOne. ExOne opened its sixth production service center, located in Auburn, Wash., in October 2013.
The 11,600 square foot facility serves industrial customers in the Puget Sound region, offering printed sand molds and cores for foundries in the Northwestern United States corridor. Inside the ExOne production service center, machines such as the S15 printer perform additive manufacturing to create complex sand casting molds and cores printed directly from CAD data.
For the automotive industry, ExOne manufactures engine components such as cylinder heads, intake manifolds and engine blocks. Because of the additive nature of the 3-D printing process, designers are able to create innovative engines for passenger cars and race engines during the development cycle. Design changes for prototype engines can be made rapidly and efficiently – within days a designer can run full tests on an actual casting.
Mold and core segments can be integrated, reducing casting preparation time and improving casting performance. Unique rigging geometry can be added to minimize turbulence, resulting in bi-films and porosity, in the casting, says the company. According to ExOne, major global companies, including Ford, Sikorsky and Caterpillar have recognized that additive manufacturing can significantly reduce costs while offering design freedoms not previously possible, and have begun to implement the technology into their manufacturing processes.
Additive manufacturing has robust market capabilities ranging from aerospace to automotive to energy, and it is not uncommon to find 3-D printers in use at metal-working factories and in foundries alongside milling machines, presses and plastic injection molding equipment.
Companies that use additive manufacturing reduce costs, lower the risk of trial and error, and create opportunities for design innovation. A serious limitation of traditional subtractive manufacturing is that part designs are often severely compromised to accommodate the constraints of the subtractive process. The advanced 3-D manufacturing process starts with a CAD file that conveys information about how the finished product is supposed to look.
The file is sent to a printer where the product is created by the repeated laying of finely powdered material (including sand, metal and glass) and binder to gradually build the finished product. Since it works in a similar fashion to an office printer laying ink on paper, this process is often referred to as 3-D printing. The 3-D printers can create a vast range of products, including parts for use in airplanes and automobiles, replacing aging or broken industrial equipment or for precise components for medical needs.
“There are tremendous cost advantages to using additive manufacturing. There is little to no waste when creating objects through additive manufacturing, as they are precisely built by adding material layer-by-layer. In traditional manufacturing, objects are created in a subtractive manner as metals are trimmed and shaped to fit together properly. This process creates substantial waste that can be harmful to the environment. Additive manufacturing is a very energy efficient and environmentally friendly manufacturing option,†says the company.
Additive manufacturing swiftly creates product prototypes – an increasingly critical function that significantly reduces the time taken with the traditional trial-and-error process. Likewise, it can create unique or specialized metal products to replace worn or broken industrial parts. That means companies can significantly compress the time it takes to machine a replacement part. With additive manufacturing, once a CAD drawing is created, the replacement part can be printed. Headquartered near Pittsburgh in North Huntingdon, Pa., ExOne has a global footprint that includes U.S. facilities in Troy, Michigan and Houston, Texas, as well as operations in Germany, Japan and Russia.
The company was founded in 2005 as a spin-off of Extrude Hone Corporation, a supplier and developer of precision nontraditional machining processes and automated systems worldwide.
Automotive Industries asked Terry Senish, General Manager of ExOne Midwest, what are some of the innovative technologies in use at the company’s new 3-D printing facility in Auburn, Washington.
Senish: We use our printers for building sand molds and cores for casting metal directly from CAD data. The large build volume and high build rates of our machines combine to make patternless production for prototypes and small-scale production. Customers can send their CAD files and we will have built and delivered a complex part to their door within days.
AI: How much of your new facility’s output will be for automotive clients?
Senish: As this facility was just recently opened, we are still evaluating our customers’ needs in the region. Across the globe at other ExOne production service centers, we have created numerous parts and prototypes for automotive customers as well as with top manufacturers in aerospace, energy and medical segments.
AI: What are the benefits of additive manufacturing to automotive companies? Give us some examples.
Senish: Additive manufacturing is redefining the automotive design process across the globe at leading automotive companies, such as Ford, BMW and Daimler. There, ExOne systems are directly implemented into production facilities for the manufacturing of castings for vehicle engines and drive trains. ExOne’s additive manufacturing process allows designers to rapidly and efficiently create and change innovative engines during the development cycle. Recently, ExOne added iron infiltrated with bronze as a new 3-D printing material to be used as a cost-effective way to manufacture intricate automotive parts.
AI: Tell us a little about the limitations of the additive manufacturing technology and how companies like ExOne are hoping to deal with them.
Senish: While the build speeds of additive manufacturing continue to improve at a staggering rate, we are still not fully comparable to traditional methods when it comes to the speeds needed for mass production. As it currently stands, additive manufacturing is ideal for complex, short-run production, and as the technology evolves over time, you will continue to see 3-D printers more prevalently side-by-side on the manufacturing floor with traditional machines making the automobiles of the future.
AI: How popular is additive manufacturing globally? How do you see the business evolving?
Senish: The process of using additive manufacturing to produce intricate industrial parts will continue to expand globally in the coming years, and ExOne is proud to be at the forefront. As designers and manufacturers continue to embrace the additive process for creating large-scale, complex industrial parts, you will see innovation that was never before possible take place. In the past five years alone we’ve seen staggering increases in both build sizes and speed of production with similar decreases in the price to produce each unit. ExOne continues to push the limits of our processes, redefining what can be accomplished with additive manufacturing across a number of industries.
AI: What are the cost benefits of additive manufacturing – please give us some examples.
Senish: Additive manufacturing has many advantages over traditional manufacturing, including cost efficiency. Since production of the sand molds and cores derives directly from the CAD data, there is no need for the cumbersome and time intensive process of hand making a pattern. Therefore, warehousing costs can be reduced dramatically since every pattern can be stored on a USB drive rather than on shelves in a warehouse. With the design freedom, designers have the ability to create multiple iterations by editing the digital file rather than building an actual piece several times.
AI: ExOne was one of the partners in the consortium set up last year between several organizations to promote development of technologies related to additive manufacturing – how successful has it been so far?
Senish: ExOne was one of the leaders in the formation of America Makes (formerly NAMII) with so many other innovative companies, universities and organizations with the goals of education and acceleration of additive manufacturing technologies and information. The success of this group will be measured by the collaboration between all member organizations to provide resources, fund research and development projects and create a community to promote a global manufacturing competitiveness
More Stories
Cybord warns of dangers of the stability illusion
Automotive Industries interviews Bahar Sadeghi, Technical Director, Car Connectivity Consortium (CCC)
Hexagon’s MAESTRO reinvents CMM systems through digitization