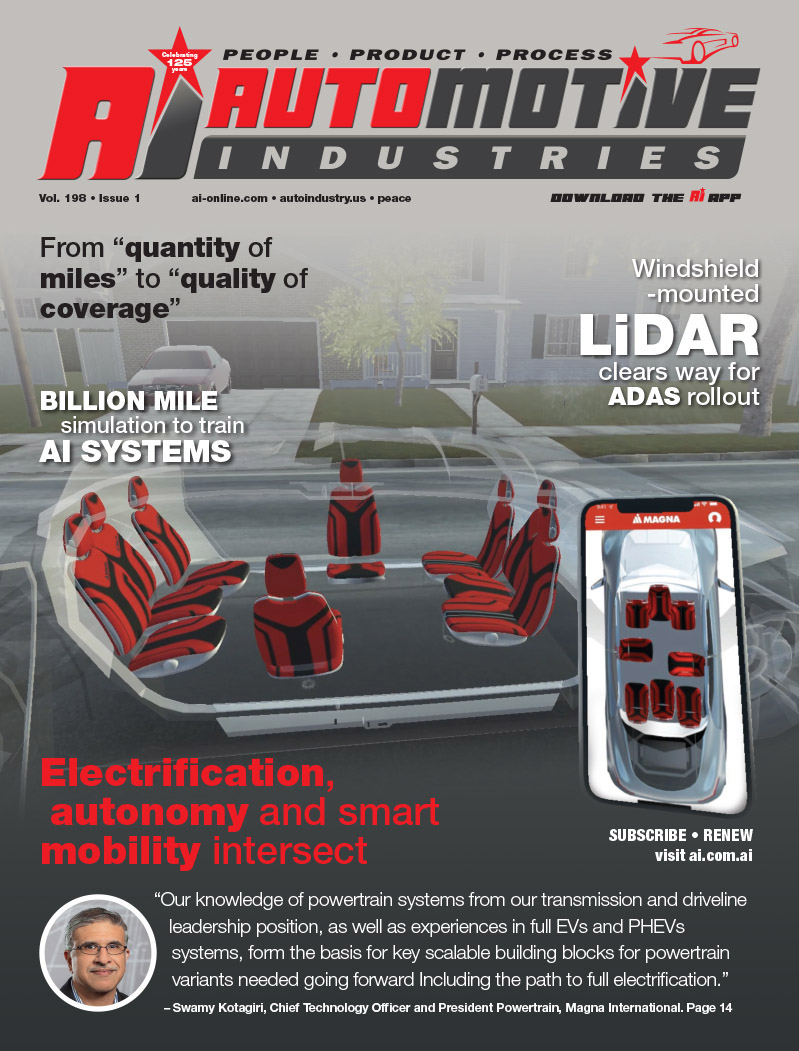
Tesla Motors is doing more than being a driving force behind the introduction of electric powertrains – it is pioneering a new approach to automotive manufacturing, according to research group IHS Technology.
IHS estimates that globally the automotive industry will account for nearly a quarter of active machine-to-machine (M2M) connections. Between 2013 and 2018, cumulative 3G and 4G module shipments for automotive will exceed 55M, a figure more than double that of any other M2M vertical market during that time span. This will drive demand for 3G and 4G technologies in the traditionally 2G-dominated M2M market, according to HIS.
The Tesla Model S is a prime illustration of both of these trends. As revealed in an IHS Tesla teardown project, the Model S is equipped with an embedded 3G HSPA+ cellular module. A physical dissection of the Model S reveals that in terms of design, components and manufacturing, these user-oriented subsystems have more in common with a tablet or smartphone than they do with a conventional automobile.
“The cost structure of the electronics, the use of large displays in the cabin, the touch-screen-based controls, the mobile microchips—everything in this design makes the Tesla experience more like a media tablet or high-end smartphone than a traditional automobile,” says Andrew Rassweiler, senior director for materials and cost benchmarking at IHS. “It’s like looking at the components from the latest mobile device from an Apple iPad or Samsung Galaxy product. When it comes to the user-facing segment of the Model S’s electronics, the company has radically departed from business-as-usual in the automotive market. This approach required a major investment in big displays and touch panels, similar to the approach Apple took when designing the iPhone and iPad.”
In another sign of Tesla’s unconventional approach, the company has undertaken its own design and engineering for the electronics. By conducting its own design in this area, Tesla not only can deliver a highly differentiated solution, but also has much more control over the costs and sourcing of parts. IHS understands that in some cases, Tesla is employing
EMS providers to build these electronic assemblies. With this model, Tesla once again is behaving more like a smartphone or tablet seller than a traditional carmaker.
An example of how Tesla performs its own custom engineering can be found in the Model S’s touch-screen controller. The large size of the touch screen requires additional electronics when compared with smaller touchscreens.
Tesla’s virtual instrument cluster is centered on a 12.3- inch diagonal 1280 x 480-resolution LCD from Japan Display, one of Apple’s iPhone 6 and 6 Plus suppliers. This is the center/core of the design and—just as in the head unit—it is the single largest cost driver. The virtual instrument cluster features the NVIDIA Visual Computing Module, an unexpected and impressive show of computing power that features a Tegra 2 processor. Considering there is also an NVIDIA Tegra 3 in the Premium Media Control Unit, this is a notable array of computing horsepower in a single automobile. While some other automakers are using the Tegra 2 in their head units, Tesla is using the chip in the instrument cluster, a less demanding application.
NVIDIA controls one of the largest shares of the value of electronic components throughout the Model S. The two Tegra processors within turnkey embedded modules command a sizable price tag. The NVIDIA visual computing module with Tegra 3 processor on board, in particular — the first time IHS has detected this part in a car — represents a high-value portion of the design.
More Stories
Automotive Industries (AI) Newsletter April 2025
GlobalLogic Pioneering Software-Defined Vehicles, AI Innovation, and Sustainable Solutions for the Future of Automotive Mobility
Cybord TCI – The Future of Manufacturing Integrity