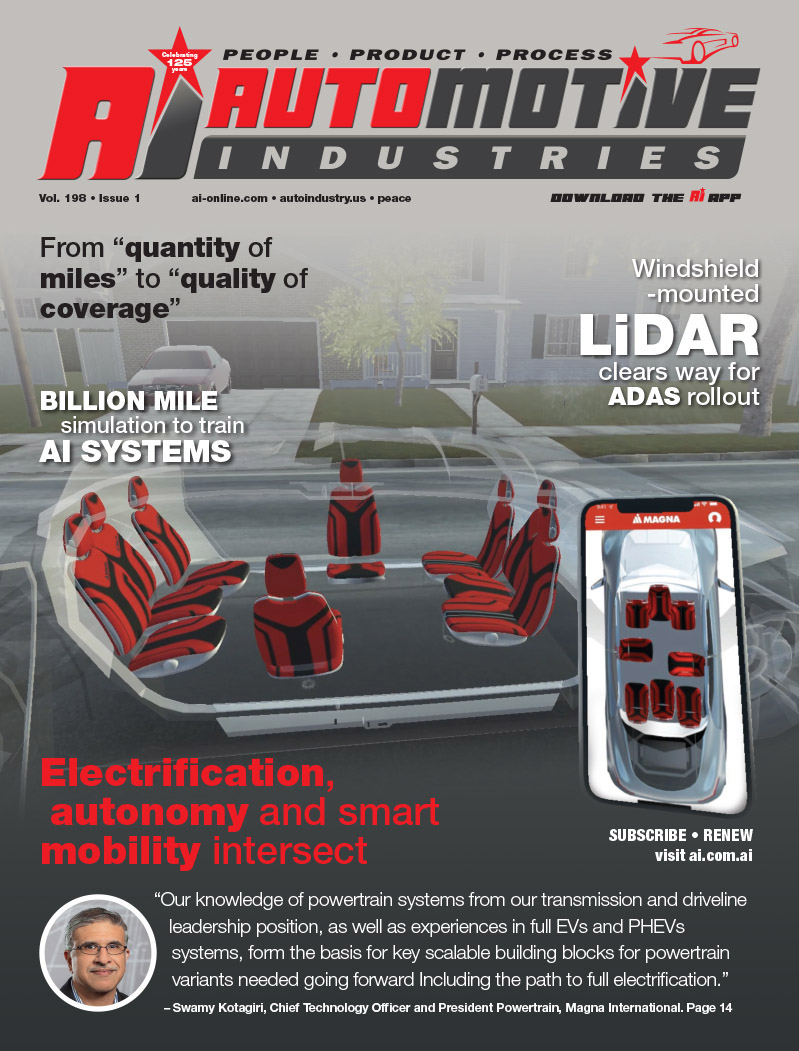
Fuel consumption testing equipment needs to provide accurate information in an increasingly complex environment, with the introduction of biofuels and new generations of diesel.
Established in 2003 to meet high demand for in-depth fuel consumption measurement expertise Reliable Solutions or ReSol is keeping pace with the changes needs of the market-place. Re-Sol has introduced the RS438-200 Diesel Flow Measurement System as part of its RS400 Mobile Fuel System family. The system is designed to cover a wide range of diesel and bio-diesel applications. The fuel measurement sensor is based on the Coriolis principle. A preheating circuit assures that engines with little recirculation flow can reach required fuel temperature after a very short time. The integrated vapor separator can be switched from open to closed loop mode to accommodate best transient behavior and best vapor separation.
AC pumps are selected to assure long durability. The outlet pump is VFD controlled. Options include a variety of interfaces (Ethernet, AK, CAN) and also stainless steel regulators and solenoid valves. The system can be packaged with and without enclosure.
The company says that its RS400 Mobile Fuel Systems adds flexibility while improving measurement capabilities for test cell fuel consumption measuring. By mounting the measurement system on mobile stands, test engineers are no longer locked into wall mounted “one-size-fits-all” measuring systems. Now with an RS400 Mobile Fuel System the fuel system can be moved between test cells. This allows the ability to have fuel systems specifically designed for different testing, such as fuel type or measurement range. It also allows greater flexibility in test cell scheduling. Having the system very close to the engine means fuel lines are shorter, reducing the volume of fuel in the measurement lines. This improves the accuracy of the measurement while also improving the ability to control fuel temperatures.
A case study on the company website, showcases how a large engine manufacturer’s system in its emissions certification lab was creating delays in the test schedule and increasing costs due to unscheduled downtime. Between 30 – 40% of the cell downtime was due to the fuel measurement system, resulting in an average of 10% monthly downtime. With the cells booked at 100% and non-flexible deadlines, this caused a cascading effect on costs and scheduling.
Peter Kaub, President of Re-Sol, met with the emissions testing team and worked with them to provide the right solution for their testing needs. According to the Manager for the test cell, “ReSol definitely went above and beyond to keep us up and running”. Since the installation of the Re-Sol fuel measurement system in December of 2009, the customer has not had a single day of downtime related to the fuel measurement system, recovering up to $80,000 in annual billable cost for the test cells. Along with these savings is the reduction in overtime and disruptions of the schedule, according to the website. ReSol works with a variety of diesel powertrain testing applications and industries. It has extensive experience in the gasoline engine testing industry. Typical applications for gasoline are single cylinder engines, direct injection, returnless fuel injection systems, ethanol, and electric hybrid engines. The company also works with the off-road mobile industries, including, snowmobiles. Its range covers military fuels, oil, and transmission fluids. Fuels include biodiesel, gasolines and ethanol blends JP8 and E85.
Automotive Industries asked Peter Kaub, President and Founder of Re-Sol, what makes the Re-Sol RS438-200 Diesel Flow Measurement System an important addition to the company’s RS400 mobile fuel system family. Kaub: There was a need for a system to cover large heavy duty engines with a good vapor separation without losing response time
AI: What are some of the features that make it different from other fuel measurement testing systems available? Kaub: The RS438-200 combines the ability to switch from a closed loop system for fastest response time and smaller engines to open loop system for very large engines where vapor is returned to the fuel flow measurement system. It has also an engine supply pump, which is controlled by a variable frequency drive (VFD). Making this system mobile allows the customer to move it between test cells. AI: What are some of the breakthroughs Re-Sol has made in gasoline engine testing and how has the industry reacted to these? Kaub: Re-Sol has been working on systems for gasoline engines, especially where there is significant ethanol content, for many years. The fact that these engines do not have a fuel return from the engine back to the tank allowed us to optimize the system with a minimum number of components downstream of the flow meter. This resulted in an excellent low flow capability for engine idle studies. All these systems have an electronic pressure control. Newer developments are covering GDI (Gasoline Direct Injection) applications. Customers are demanding pressures up to 50MPa. This is often needed for single cylinder research, where the high pressure pump is not mounted on the engine.
AI: Give us some examples of auto companies that have/ are using your testing systems and the cost savings they have made. Kaub: Re-Sol’s solutions can be found at every major automotive manufacturer here in the US. This is true also for the component suppliers, which have to analyze how much their component is influencing the fuel consumption of the vehicle. That includes manufacturers of radiators. Due to the reliability and mobility of the systems, the downtime of each test cell was reduced. If components do break, Re-Sol’s customer support team aims to get the customer back on line within a day. Another cost reduction for a customer was the introduction of the family of calibration carts, which come in a variety of configurations.
AI: What differentiates the customer experience with Re-Sol – how does your company work alongside your automotive customers? Kaub: Re-Sol is putting a major emphasis on fast response to customer’s need. This goes beyond the regular office hours. This is also true for the calibration service, which Re-Sol is offering since its ISO17025 accreditation. This service includes on-site support. AI: How has your previous experience in the industry influenced the way you run your company? Kaub: I have been involved in the fuel flow measurement field since 1984. During the course of the time I realized that it is not only important to have an excellent flow meter, but also packaging it to suit the customer’s need. This includes data interfacing. To get it right, the company and designers need to be connected with the customer from the time he recognizes the need for the solution until the time the system is signed off. Re-Sol also assists with the writing of system specifications.
AI: What are some of the differentiators when testing alternative fuels and how has Re-Sol had to change strategy in this field? Kaub: Alternate fuels mostly require equipment to be corrosion resistant, and to have seals which are compatible with the different type of fuels. If you talk about gaseous fuels like CNG or even LPG, then a completely different product line had to be developed. Re-Sol has also delivered systems and components for these applications.
More Stories
What You Should Know Before Filing a Car Accident Claim
Injured in a Car Accident in St. Louis? Here’s What to Do Next
Historic Sportscar Racing (HSR) and Goodyear Announce Multi-Year Partnership