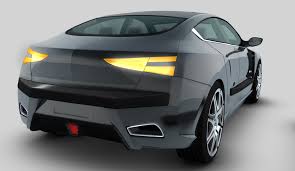
New rear lamp housings for vehicles can now have an even greater aesthetic appeal and performance thanks to material and processing innovations from Ichikoh Japan and INEOS Styrolution. These innovations are the results of a new laser welding technique developed by Ichikoh and a unique styrenic polymer solution from INEOS Styrolution. Ichikoh manufactures the part using a specific black colored Novodur HH-112 developed from INEOS Styrolution’s high-heat acrylonitrile butadiene styrene (ABS) product line. This polymer is ideal for Ichikoh’s newly developed laser welding process as it offers a good appearance at the welding areas of the plastic parts when compared with other polymers. Overall, the new material and laser welding process have a significant impact on the design and production process of the rear lamp housing, lending the hybrid an even sleeker look and helping to reduce total production costs. This new technology was introduced into the Japanese market in November 2015. Novodur HH-112 is now available globally from INEOS Styrolution.
Key points:
— Ensuring aesthetics and greater design flexibility through new laser
welding process: Ichikoh Japan wanted a processing solution that could
achieve good appearance at the welding areas on plastic parts. However,
this would be impossible to achieve with conventional welding techniques
such as hot plating or vibration welding due to complicated part designs
and shapes. For this reason, a new laser welding technique was utilized
for the rear lamp housing to facilitate more design freedom and achieve
the required surface appearance. In addition, this new laser welding
technique also has the potential to generate more stability and higher
mechanical strength at welded areas compared to conventional welding
methods.
— The right material solution to drive design innovation and performance:
The challenge with most black or dark colored polymers is the materials’
high sensitivity to laser beam, resulting in uneven surfaces at the
welding area when a laser beam is applied. As such, Ichikoh sought to
find a polymer solution that would not only optimize the process to
achieve suitable laser welding conditions but would also adhere to the
substrate and most importantly, a great looking finished product.
Ichikoh partnered with INEOS Styrolution to select the right styrenic
polymer for the application. Working in collaborative innovation, INEOS
Styrolution custom developed Novodur HH-112, a high-heat ABS specialty
styrenic grade that would offer the performance and aesthetic qualities
they require. This marks the first time an ABS resin has been used for a
black color laser welded application.In the end, the leading Japanese
car manufacturer was pleased with the vastly improved part appearance at
the welding area. The new process and polymer solution also helped the
car manufacturer improve the quality of their cars design.
— Novodur HH-112 now globally available: Novodur high-heat ABS grades meet
stringent stability requirements for thermally stressed components.
Novodur high heat is the material of choice for numerous heat-resistant
applications, like rear lamp housings, radiator and front grilles, as
well as exterior trims. The new Novodur HH-112 product is now available
globally from INEOS Styrolution.
Plant Engineering Division, Ichikoh Japan: “This is the first time black colored high-heat ABS is being used for a laser welding application. We are aware of the tough challenge we had given to Styrolution to achieve our target based on market requirements. We are confident that Styrolution’s Novodur HH-112 will prove to be a game changer for laser welded parts in the future.”
SungBeom Park, Asia Pacific Lead, Automotive, INEOS Styrolution: “It is our corporate DNA to always look for the best solutions for our customers, combining costs saving, technical performances and processing. The new laser welding method developed by Ichikoh Japan is unique and will set a standard for car manufacturing in the future. It is a privilege to be able to work with a leader in automotive innovation like Ichikoh Japan.”
About INEOS Styrolution
INEOS Styrolution is the leading, global styrenics supplier with a focus on styrene monomer, polystyrene, ABS Standard and styrenic specialties. With world-class production facilities and more than 85 years of experience, INEOS Styrolution helps its customers succeed by offering the best possible solution, designed to give them a competitive edge in their markets. The company provides styrenic applications for many everyday products across a broad range of industries, including automotive, electronics, household, construction, healthcare, toys/sports/leisure, and packaging. In 2015, sales were at 5 billion euros. INEOS Styrolution employs approximately 3,100 people and operates 15 production sites in nine countries.
More information: www.ineos-styrolution.com
More Stories
How Modern Power Management Enhances Connected Fleet Tech
Automotive Industries (AI) Newsletter April 2025
Bangkok International Motor Show 2025 – The Talk of Sensuous Automotive