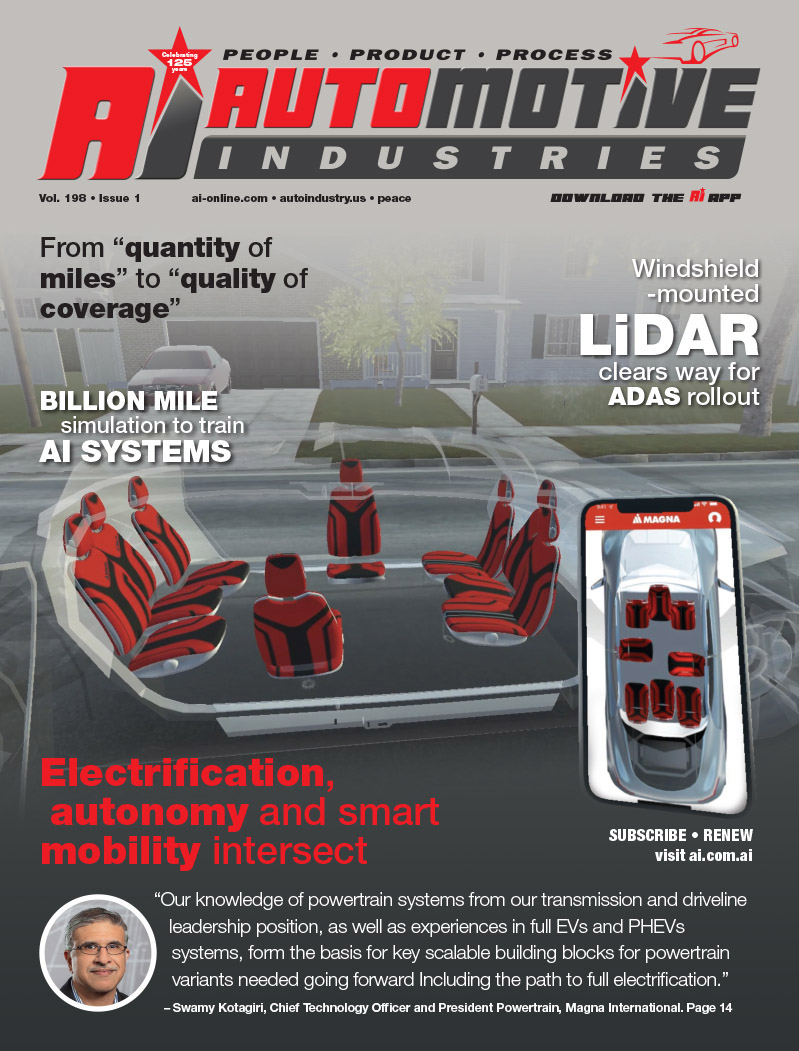
Breakthroughs in polymer technology are helping engineers to improve fuel consumption and decrease emissions by reducing friction in the drivetrain and weight throughout the vehicle.
One of newest products, Stanyl® HGR1, was showcased by DSM Engineering Plastics at the SAE World Congress 2016, which was held in Detroit in April. Until now, the industry standard for timing chain wear faces has been Stanyl TW341, but for new engines Stanyl HGR1 is being selected because it provides better friction performance, and therefore lower fuel consumption and CO2 emissions, according to the company.
Stanyl resin is widely used in engine and other under-hood components because of its ability to withstand extremely demanding conditions, which include high continuous use temperatures, high loads, harsh chemical environment, and heavy vibrations.
In 2015, DSM strengthened its portfolio through the formation of a joint venture with NHU for the development and manufacturing of high performance plastics
compounds based on polyphenylene sulphide (PPS) and marketed under the name Xytron™. The Netherlands headquartered-DSM operates more than 200 facilities around the world, including 40 US- based facilities and two Indiana-based facilities in Evansville and Frankfort.
Automotive Industries (AI) asked Satish Kantebet, Automotive Sales Segment Manager at DSM Engineering Plastics how much more plastics can contribute to the “lightweighting”of cars.
Kantebet: Plastics are only scratching the surface when it comes to harsh environments such as the engine and transmission where a significant amount of steel and aluminum continue to occupy space. High-performance DSM Engineering Plastics such as Stanyl PA46 are being specified in areas such as integrated air intake manifolds, timing chain guides and charge air coolers that are being given consideration as the material of choice for OEMs as they look to reduce weight and meet stringent future CAFE standards imposed by governments. Until we reach a point of 100% plastic penetration in an automobile, DSM will continue to innovate and develop products and technologies that surprise and delight our direct customers (Tier 1s) and their customers (Global OEMs).
AI: Tell us about the heat-resistant qualities of Stanyl and why this is important?
Kantebet: Stanyl PA46 is well known in the industry for its friction reduction capabilities in timing chain systems, but is now also recognized in the automotive thermoplastics community as introducing the world’s first high heat plastic air intake manifold (PAIM) with an integrated charge air cooler. The product is known as Stanyl Diablo and is able to operate at a continuous use temperature of 220 degrees C to a peak of 250 degrees C, and withstand pulses of high internal pressure. The Diablo Grade OCD2100 is 40% glass fiber reinforced and has a specially developed and patented heat stabilizer. These types of manifolds have only typically been produced in metal. However the auto manufacturers have demanded a plastic solution in order to reduce weight and maximize design efficiencies. The Stanyl family of polyamides has significantly better high temperature performance than standard polyamides.
AI: What were some of the highlights from DSM at the SAE World Congress?
Kantebet: DSM offers one of the largest portfolios of high-performance plastics in the industry. At SAE World Congress, DSM showcased their material solutions and applications responding to the industry needs such as improved fuel economy and CO2 reduction.
- Metal to plastic / weight reduction (e.g. engine covers, oil pans, cylinder head covers, front & rear engine covers)
- Air management / turbo (e.g. ducts, integrated air intake manifolds, charge air cooler end caps)
- Gears for precision control & next generation technologies (e.g. exhaust gas recirculation, waste gate actuation, electronic throttle control, electronic parking break, etc.)
- And Stanyl PA46, which was greeted with much interest from the industry
AI: What role have DSM products played in vehicles – for example, in everything from gear boxes to rear view mirrors?
Kantebet: DSM is a major developer and global supplier of polyamide engineering plastics with a portfolio that includes Akulon® PA6 and PA66, Stanyl® PA46, Stanyl® ForTii™, and EcoPaXX®, a bio-based polyamide that is certified carbon neutral from cradle to grave. In addition DSM supplies Xytron™ PPS and thermoplastic polyesters Arnite® PBT and PET, and Arnitel® TPC for engineering applications. These materials are used in applications and products all over the world by the automotive industry. Many applications today such as Stanyl Gears within Turbo Actuation and Steering Systems, Akulon PA6 in Driver and Passenger Air Bag Canisters, Arnite PET in Brake Booster Valve Bodies, Arnitel TPC for Steering System Boots and Bellow and PA66 in Structural Oil Pans are just a fraction of the deep portfolio of applications that DSM provides to its customers.
AI asked John Jurecko, Automotive Business Development Manager at DSM Engineering Plastics – Americas what was included in DSM’s product portfolio at the 2016 SAE World Congress.
Jurecko: Expanding our product portfolio allows for a material neutral approach to many applications in engine covers, actuation (gear systems), and turbo / air induction. For example, DSM offers both flexible and rigid materials to cover the entire temperature range of turbo ducts, CAC (charged air cooler) end caps, AIMs, and resonators. DSM is also very active with actuation that enables more precise control of the engine, thus improving efficiency. In addition, a tremendous amount of weight (and cost) can be taken out of the vehicle by utilizing DSM’s metal to plastic program management service for large parts like oil sumps, cylinder head covers, and front and rear engine covers, especially when integrated features are incorporated into the part. Of course, there’s also all the DSM plastic parts inside the engine and transmission such as bearing cages and timing chain wear faces that reduce friction, thus improving efficiency and fuel economy.
AI: What additional uses are being identified for the Stanyl polyamide?
Jurecko: The Stanyl product line is being advanced in many application areas due to its very good wear and friction properties combined with very high operating temperature and good mechanicals. This makes Stanyl ideal for under-hood parts exposed to friction such as actuation / gear systems, starter and engine balancer gears, bearing cages, timing chain wear faces, and dampening elements.
AI: Tell us about the role played by Stanyl PA46 in the new turbocharged gasoline engines designed by Quadrant Creative Molding & Systems.
Jurecko: Stanyl PA46 was selected for this engine application because of demanding performance requirements for a low friction and very durable resin. AI: What are some features of Stanyl HGR1 and HGR2?
Jurecko: Stanyl HGR1 and HGR2 represent the latest developments from DSM Engineering Plastics and provide the best wear and friction performance available today for timing chain system wear faces. When compared to prior Stanyl grades, the HGR1 and HGR2 provide reduced friction benefit that OEMs and Tier suppliers have validated as improving fuel economy by up to 1 mile per gallon.
More Stories
Venti Technologies Wins Multiple Pinnacle Awards for Innovation and Achievement in Technology
Launch of AltaScient.ai: New horizons for Risk and Sustainability Analytics
Expert Tips on Detailing a Car