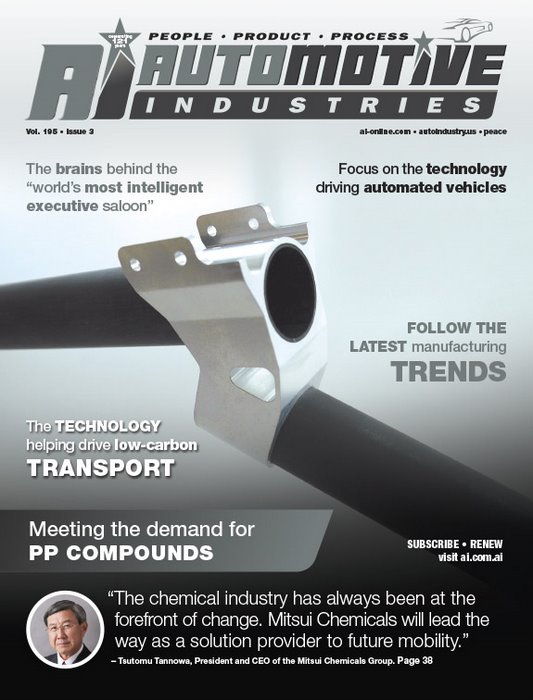
The percentage of polypropylene (PP) compounds in vehicles is growing as automotive OEMs strive to meet increasingly stringent regulatory demands by reducing weight. Although plastic accounts for around 10% (or approximately 100kg) of an automobile’s total weight, it comprises 70% of the 30,000 parts in automobiles. In response to this growth, Mitsui Chemicals and group company Prime Polymer are increasing the production of automotive grade PP compounds at plants in the United States, Mexico and India by 5%. This will increase the group’s production capacity from one million to 1.05 million tons a year, and make it the world’s top provider of automotive PP compounds in the 2017 fiscal year.
In 1912, Mitsui Chemicals became the first group in Japan to produce raw material for chemical fertilizers from coal gas byproducts. In 1958, it built Japan’s first petrochemical complex. Today it has a manufacturing network of 145 companies in 27 countries. With a share of around 60%, the group is the leading supplier of PP compounds to the automobile sector in Japan, and ranks second globally. The Mitsui Chemicals Group also holds a 30% share of the U.S. automobile manufacturing market. It has eight global production sites (Japan, USA, Mexico, Europe, Thailand, China, India, and Brazil) and PP compound R&D facilities in Japan, USA, Europe, Thailand, and China. Prime Polymer, which is a polyethylene and PP joint venture between Mitsui Chemicals and Idemitsu, is the leading Japanese PP supplier to the automotive industry. Mitsui Chemicals is also adding three production lines in the United States and Mexico through its affiliate Advanced Composites. The company is strengthening its presence in Europe by opening a new R&D center.
Automotive Industries (AI) asked Tsutomu Tannowa, President and CEO of the Mitsui Chemicals Group, how the group supports OEMs.
Tannowa: The automotive industry is looking to save weight alongside improving safety, comfort, and design solutions. To meet these needs the Mitsui Chemicals Group has established eight bases in major world markets to respond speedily to meet the requirements of global automobile manufacturers for the PP compounds needed to reduce automobile weight and actualize complicated designs. We have increased our production capacity and problem solving capabilities at these bases to support our clients. Not only PP compounds, our possibilities as a solution provider are infinite. We have a performance-driven, high quality synthetic rubber, Mitsui EPT™, developed from our proprietary metallocene catalyst technology.
We have an outstanding adhesive resin ADMER™, which contributes to weight reduction and provides design freedom for fuel tanks. MILASTOMER™, a superior quality automotive interior material, TAFMER™, an elastomer modifier, and our high performance urethane raw materials which are used in seat cushions and as sound-absorbing material, are all part of our performance-driven selection.
All of these materials help make automobiles more attractive and more comfortable. Our coating raw materials contribute to better designs for automobiles and our CarbonFiber-SMC helps to reduce the weight of structural parts. AURUM™, an engineering thermoplastic, is widely used in and around engines. ARLEN™ is a modified polyamide 6T, which is comparable to super engineering plastics for under the hood applications. LUCANT™ is a gear oil additive which helps to improve fuel efficiency. Our group company, Kyowa Industrial, is well known for its large-scale molding technology. We will capitalize on our strengths by bolstering our ability to grasp next-generation needs and provide new solutions which use our knowhow to create a value chain from resins, design, flow analysis, and molding. By fully using our Group’s strengths, we will be better able to make proposals and help accelerate development of our customers.
AI: What are the most recent developments?
Tannowa: We have started the full-scale introduction of our bonding and composite technology, POLYMETAC™ which is the metal and resin integral molding of various materials without using adhesives. Until recently there was no standard to evaluate strength of heterogeneous adhesion. With the establishment of an ISO standard, we will be able to advance and expand deployment of the application.
POLYMETAC™ technology was adopted in frames of Unmanned Arial Vehicles (UAVs) to cut weight. By taking advantage of our CAE technology and designing the parts, we were able to achieve more rigidity while cutting down on weight and the number of components. These efforts help boast UAVs flight distance by 40%. In addition, we established a heat resistant lens grade for automotive lens applications to respond to future “smart” automobile needs by using our APEL™ technology which already has a high global market share in smartphone camera lenses. We have also established a New Robot Materials Division where we provide innovative solutions to the robot industry through development of new products by capitalizing on group material, molding, and analysis technologies.
AI: What are the benefits to the auto industry of Mitsui Chemicals & SKC Polyurethanes joining forces in July 2015?
Tannowa: We now have global strategic bases for urethane system products and our integrated system – which starts with raw materials – will serve to bolster our ability to meet the needs of our customers. By leveraging the strengths of the two companies we are able to provide even better and more comfortable solutions for automotive interiors. Since the establishment of our joint venture, we have developed a new base in Mexico and are studying the feasibility of future expansion of our strategic sites. Additionally, we are enhancing our production sites for raw materials to reinforce our high value-added polyurethane system products and operations. Our bio-polyol plant in India started operations in January 2016. This will accelerate our global expansion of environmentally-friendly seat cushion materials using bio-polyols made from non-edible plants. In Korea, we decided to enhance capacity of VOC reduction facilities at our polyol plant and enhance capacity of our MDI plant from 250 thousand tons per annum (KTA) to 350 KTA.
AI: What do you see as the main challenges for Mitsui Chemicals over the next few years, and how are you addressing them?
Tannowa: The chemical industry is closely linked with various sectors which are behind social change. For example, the lithium ion battery (LIB) is playing a major role in the development of the electric vehicle. Mitsui Chemicals has the first material which prevents thermal runaway, a major safety concern of large LIBs. Our STOBA™ reduces the risk of fire in LIBs. This breakthrough product continues to contribute greatly in the expansion of the EV market. The automobile needs lighter materials, improved safety, greater comfort, and better design. It is important that we continue to meet the needs of our customers and consumers. For this, we must bolster our ability to provide fresh value by a cross-organizational approach to make the most of our materials. As seen by the introduction of autonomous vehicles, the concept of the automobile itself may have come to a major turning point. The chemical industry has always been at the forefront of change. Mitsui Chemicals will lead the way as a solution provider to future mobility.
More Stories
What You Should Know Before Filing a Car Accident Claim
Injured in a Car Accident in St. Louis? Here’s What to Do Next
Historic Sportscar Racing (HSR) and Goodyear Announce Multi-Year Partnership