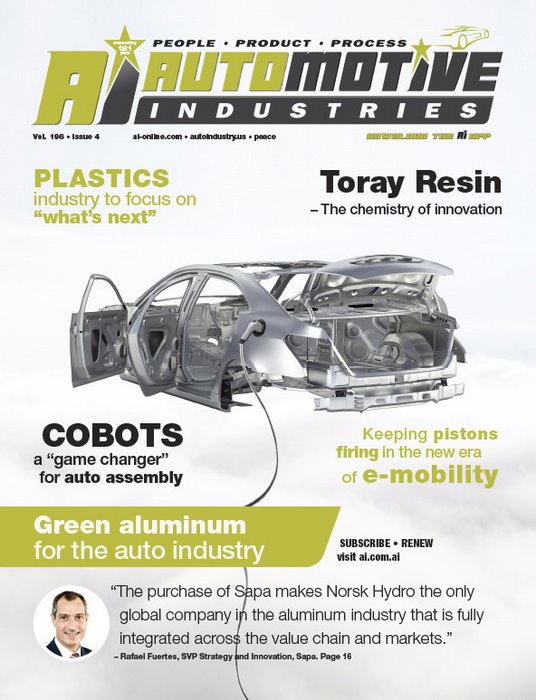
Europe is to retain its leadership as a producer of aluminum using green energy through the acquisition by Norsk Hydro of Sapa.
“Today symbolizes the start of our exciting journey as the leading force within the global aluminum industry, fully integrated from bauxite to end-user products and with the best-possible platform for further growth and optionality, innovation and product development, and sustainability and responsibility,” said President and CEO Svein Richard Brandtzæg in October after the acquisition had been approved by competition authorities in a number of countries.
As Hydro’s new Extruded Solutions business division, Sapa will continue to operate with the business units Extrusion Europe, Extrusion North America, Precision Tubing and Building Systems. The unit has 22,400 employees and a presence in around 40 countries.
Automotive Industries (AI) asked Rafael Fuertes, SVP Strategy and Innovation, Hydro Extruded Solutions what prompted Hydro to acquire Sapa.
Fuertes: In 2013 Hydro extrusions was merged with Sapa (owned by Orkla). At the time there was an agreement between the shareholders for a 50-50 joint venture with the option to either go to the market or look at it again in three years. Measured by the results, the joint venture was a success. We’ve completed the restructuring, delivered synergies ahead of plan, and adopted a new strategy which adds more value as measured against volume. The first step was to restructure the business in Europe, the second to increase the volume and then we focused much more on added value.
So, after the company’s very good results there was some discussion between Hydro and Orkla and Hydro decided to buy 50% of the shares.Sapa Enterprise is valued at NOK 27 billion (US$35 billion). Sapa is now a new business area in Hydro, named Extruded Solutions. The combination makes Norsk Hydro the only global company in the aluminum industry that is fully integrated across the value chain and markets, and gives Hydro unparalleled strength in technology, R&D, innovation and product development, as well as an unmatched product and service offering to the benefit of more than 30,000 customers throughout the world.
From bauxite to aluminum products, Extruded Solutions has very strong R&D with more than 1,000 engineers spread all over the world with two R & D centers in Sweden and in Detroit working very hard on alloy development.
AI: How do you see the future in terms of growth capabilities?
Fuertes: The acquisition provides Hydro with the capability and freedom to grow in the most attractive areas of aluminum. First of all Hydro has a very strong financial muscle. They see an opportunity of mainly developing new business. The marriage between the two companies is very good.
We are looking to achieve synergies of NOK 200 million (US$25 million) per year, mainly related to remelt and recycling as well as further strengthening the sustainable solutions for the future low-carbon economy, but the main drive of the integration is the strategic impact.
AI: In terms of sustainable solutions, what do you and Hydro offer?
Fuertes: As part of our strategy for innovation and sustainability we’ve introduced a number of innovations over the past two years. For the next three years our main effort will focus on sustainability. As a start we are sourcing green metal from Hydro. All the metal produced in Norway is processed using hydro power. Then Hydro has probably the best technology in sorting to separate the different alloys before casting. One of the problems we have in recycling is to extract different materials such as aluminum, chrome, rubber and zinc, as well as the alloys.
Let me give you an example: 95% of the aluminum content of the car is recycled, after being collected from the dealers. But there are many alloys, and most of the scrap goes to China. Over 1,000,000 tons of scrap is imported into China every year. This is not just metal – it is energy as primary aluminum production is highly energy intensive. Now with Hydro we are able to keep this metal in Europe, and we are able to provide the local market with recycled solutions. Our motto is: “Infinite solutions: responsible operations and sustainable solutions for the future low-carbon economy”.
AI: Let’s talk about electric vehicles getting lighter. What are you providing on the aluminum extrusion technology side?
Fuertes: Aluminum content in the car is growing. We are providing a lot of metal to Tier 1s and OEMs, not only for crash management components. The advantage of aluminum is of course that is lighter and it absorbs the impact and energy in the crash much better than other materials. Another trend we see is that the OEMs are moving to aluminum for car frames. We are one of the main suppliers for Ford, and are Q1 Certified.
Coming back to e-mobility. The main weight in the car is the battery, and one of the key components in the car is the battery box. In the first models this battery box just contained the battery, but now the box is becoming part of the vehicle structure. Aluminum is the ideal material for a box which is integrated into the frame.
AI: What are the challenges and advantages with multi materials in terms of lightweight, safety, design?
Fuertes: In the past we were able to achieve the strength property with 7000-series alloys. Now we achieve the same properties with 6000-series alloys. The advantages in the manufacturing cycle are that the alloys offer better extrusion and finishing properties.
But, even if you have the right alloy, you are not going to achieve the desired properties if the extrusion process is not properly controlled. You need specific temperatures and a controlled cooling cycle. It has to be a combination of the right alloy with the right process parameters. This is particularly true for crash management components where you need not only strength, but also elasticity.
More Stories
What You Should Know Before Filing a Car Accident Claim
Injured in a Car Accident in St. Louis? Here’s What to Do Next
Historic Sportscar Racing (HSR) and Goodyear Announce Multi-Year Partnership