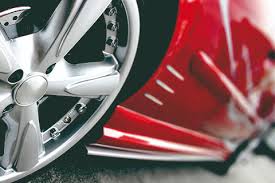
Additive manufacturing has emerged as one of the fastestdeveloping disruptive technologies in modern times. “In a few years, it has gone from being an exotic plaything for crazy inventors and well-funded research laboratories, all the way to a major disruptive technology that could well turn industrial manufacturing upside-down,” says Patrick Duis, Segment Leader Transportation Additive Manufacturing, Royal DSM. A “global 3D printing ecosystem” is being built through the establishment of a growing number of strategic partnerships between companies involved in all aspects of additive manufacturing (AM). “We believe that by working together closely with partners across the 3D printing value chain is the best way to continuously push the boundaries of additive manufacturing. “The AM ecosystem is growing bigger every day, giving our customers access to the best of all worlds in terms of materials, printing equipment, software, etc.
Together, we are making Manufacture Tomorrow a reality,” said Hugo da Silva, Vice President of Additive Manufacturing at the Dutch global science-based major Royal DSM. “DSM will continue to broaden the range of its material solutions to give our customers the largest choice of printing technologies and materials to best suit their applications. This is why we are building on our SLA, FFF and recently launched powder materials, and are entering into the pellet and DLP technologies. These innovative materials take us one step closer to unlocking the full potential of additive manufacturing,” he said. In May 2019 DSM announced a partnership with Adaptive3D, the premium additive manufacturing polymer resin supplier. DSM will help produce, distribute and sell Adaptive3D’s newest product, Soft ToughRubber™, a new 3D printable photopolymer.
The new material allows manufacturers to explore applications in medical models and consumer products such as audio earbuds and footwear. The partnership will guarantee the availability of the new material in production volumes worldwide, according to a joint statement. “This partnership allows us to combine DSM’s global supply chain and strong relationships in key markets with Adaptive3D’s proprietary material innovations. Yet another example of how DSM’s commitment to build a global additive manufacturing ecosystem offers original equipment manufacturers (OEMs) across the globe access to cutting-edge materials,” says Noud Steffens, Market Development Director Additive Manufacturing at DSM. “Aside from new applications in consumer products and medical models, Soft ToughRubber™ adds to the materials available for manufacturers looking for sustainable options”, added Walter Voit, founder and CEO of Adaptive3D Technologies.
“Thanks to additive manufacturing we are able to reduce material waste in parts production. DLP printing uses light instead of heat to cure materials, leading to dramatically lower energy consumption and a lower carbon footprint.” DSM says the companies will continue working together closely to explore new applications and develop materials. They will focus on and co-develop materials that enable next-generation soft, flexible and elastic solutions. These will create new possibilities for innovative applications in footwear, textiles, automotive and electronic appliances, amongst others. As such, both consumers and producers stand to benefit from the improved and highperformance materials developed by DSM and Adaptive3D. DSM invested in Adaptive3D Technologies earlier in 2019, and now partners with the company to sell, distribute and produce Soft ToughRubber™, Adaptive3D’s new material. Soft ToughRubber™ will enable innovation in anatomical medical models as well as in wearable electronics or consumer products such as audio earbuds. The material combines the feel and mechanical properties of silicone with the resolution and surface finish that Digital Light Processing® (DLP®) printing provides.
“In the future, we could well see AM being integrated into hybrid work stations with multi-axis robots, equipped with automatic tool change systems that allow them to switch between yet more AM technologies like fused granulate fabrication (FGF – also known as direct printing with pellets) and continuous fiber feeding, to milling, to thermoplastic composite tape laying, making one-off parts to personal order that it would have been impossible to make just a short while ago. For several years, for example, DSM has been working with Toyota Motorsport GmbH (TMG) on development and production of SL parts for TMG’s limited series of GT86 CS-V3 consumer racing cars. AM is a cost-effective solution, as TMG can print the parts instead of hand-making them with composites on machined tools,” says Duis. Partnerships are part of DSM’s wider strategy of boosting its strengths in the additive manufacturing sector. In May 2019 it launched an all-inclusive 3D printing solution called the TriCollective – the first of its kind. For a monthly fee, the TriCollective offers DSM’s customers a leased printer (in collaboration with financial partner CHG), access to its wide range of world leading materials, as well as expert guidance in choosing the right technology and materials for specific application purposes. The new solution will initially focus on long-term lease options for stereolithography printers, but will over time include other technologies and short-term trials.
Another partner DSM is collaborating with is the Dutch-based CEAD, a supplier of 3D-printing equipment focusing on largescale, highly filled polymer printing. Together, the two companies will explore FGF (fused granulate fabrication) technologies and materials to develop new applications in tooling and end-use parts, says a company release.
“By expanding our offering to FGF materials DSM gives manufacturers across the globe maximal flexibility in choosing the material and technology that best suits their desired applications. FGF technology allows us to use highly filled polymers that increase the thermal, mechanical needs and the performance of our application and thus takes us closer to injection molded parts,” said Patrick Duis, Segment Leader Transportation Additive Manufacturing at DSM. Together, DSM and CEAD will combine their experience in 3D-printing technology and materials to explore innovative application purposes in tooling and end-use parts aimed at the automotive, marine and infrastructure industries.
They will work together to create new materials, update CEAD’s printer and improve both companies’ processes, he said. DSM has acquired a CEAD robotic printer, initially for R&D purposes. From September it will be available for commercial projects via a service partner. The system features the novel extruder system from CEAD and is placed on a 6-axis robotic arm from Comau and with control software from Siemens. The machine is also equipped with a milling center and scanning unit for post-processing the parts directly on the machine. With this equipment, CEAD and DSM will be able to create material profiles optimized for FGF printing. By adding material, process and machine know-how, DSM believes it will be able to unlock the full potential of the FGF printing technology, increasing material and manufacturing options for customers. The cooperation also opens the door to advanced processes like adding continuous fiber combined with highly filled polymers to create applications that would not be possible without this technology.
“The relationship between the 3D-printing technology and the materials that are used in the process, are key. Through this collaboration with DSM and their understanding of the materials, we are able to fully leverage the technology to its full potential”, said Maarten Logtenberg, CEO of CEAD. CEAD is a technology supplier of 3D-printing equipment, and sits on the frontier of large-scale additive manufacturing. DSM recently also announced a new partnership with Origin, the San Francisco-based pioneer in Open Additive Manufacturing.
The first DSM material optimized for Origin’s printer, Somos® PerFORM HW, was on display in DSM’s booth at RAPID+TCT 2019. The material shares the advantages of Somos PerFORM for those looking to explore applications such as aerodynamic or rapid tooling.
More Stories
Automotive Industries (AI) Newsletter April 2025
GlobalLogic Pioneering Software-Defined Vehicles, AI Innovation, and Sustainable Solutions for the Future of Automotive Mobility
Cybord TCI – The Future of Manufacturing Integrity