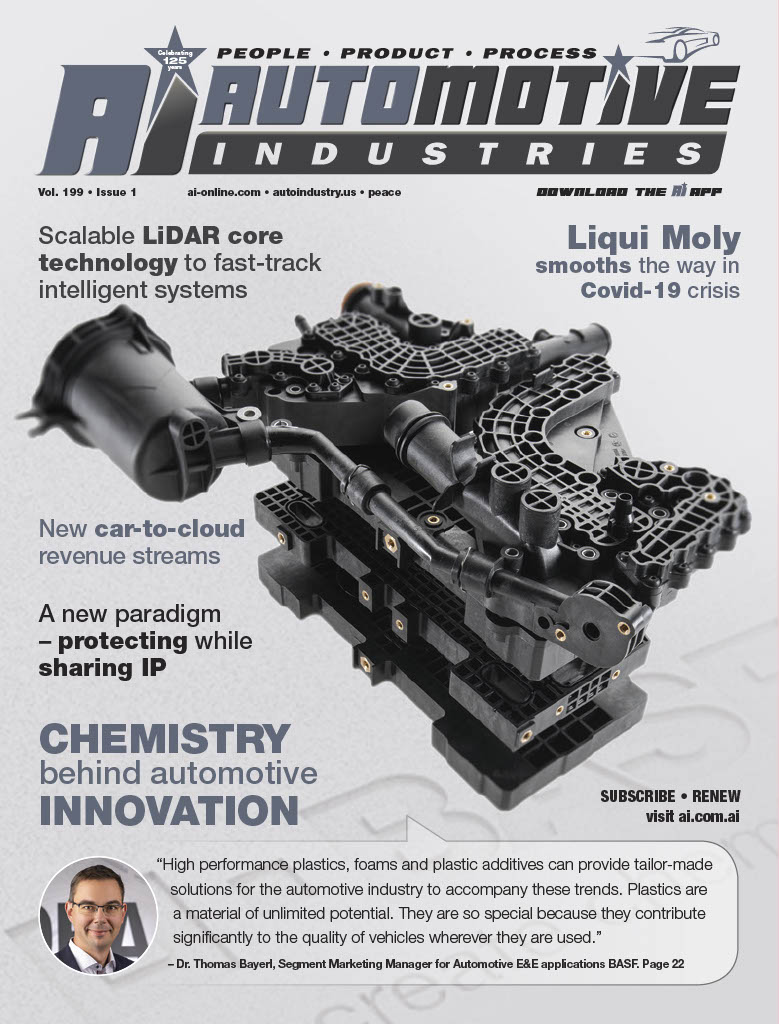
Chemistry is set to play an even greater role in the evolution of passenger and freight vehicles, with new materials being developed to help solve mobility challenges.
When it comes to passenger vehicles, the customer expects the vehicle to have an appealing exterior and interior, it must be comfortable and it must be safe. At the same time, the end of the era of cheap fossil fuels and the need to alleviate climate change call for more efficient vehicles with lower emissions. To meet these requirements, the automotive industry needs to continue to innovate. Modern vehicle components are already heavily based on chemical products and solutions. One of the leaders in the industry is BASF, which develops and supplies engineering plastics and polyurethane solutions that enable vehicles to be built more efficiently and with a lower environmental impact.
Automotive Industries (AI) asked Dr. Thomas Bayerl, Segment Marketing Manager for Automotive E&E applications BASF, how the BASF Engineering Plastics powertrain experience points the way for the next generation of automotive applications in e-mobility.
Bayerl: With an ever-increasing number of electronic components in vehicles, brought on by improved connectivity, advanced autonomy and the electrification of fleets, vehicle manufacturers must consider how these components impact automotive design and material selection. BASF engineering plastics protect vehicles’ complex technologies, to ensure accuracy and safety.
AI: What materials and solutions do you offer in the field of fuel cells?
Bayerl: The high quality and safety requirements for fuel cells place huge demands on materials. With versatile and sophisticated polyamides (Ultramid®), polybutylene terephthalates (Ultradur®), polyphthalamides (PPA), and the plastics polyoxymethylene (Ultraform®) and polyethersulfone (Ultrason®), BASF is able to keep pace with car manufacturers’ latest developments, while also setting innovative trends.
In the case of the media distribution plate in the fuel cell and the water separator unit, which is exposed to a wide variety of media through the cooling water, air and hydrogen channel, Ultramid A3EG7 EQ offers excellent resistance, while at the same time meeting all requirements regarding the purity of the material. Ultramid A3WG10 CR is a glass fiber reinforced material and very crash resistant. It is now being used as standard to manufacture the anode and cathode end plates in fuel cells.
AI: How do BASF’s automotive plastics shield against electromagnetic interference for optimal signal clarity and interference?
Bayerl: Ultramid and Ultradur grades for high-voltage housings meet high standards for flame retardance, mechanical strength, and electrical isolation. This includes solutions for electromagnetic shielding, which is an intrinsic property of metallic structures. BASF is working on processes to equip such plastic housings made of flameretardant Ultramid with a thin metal layer. The same high shielding efficiency can be obtained from this method compared to housings made of pure metal. This plastic solution allows automotive manufacturers to save weight and design space while having an alternative to standard aluminum die-cast solutions.
AI: More and more companies are creating their own electric vehicles. How can the product designers and engineers ensure that the materials used inside these vehicles have high voltage compatibility?
Bayerl: High performing materials are needed to protect the applications that power electric vehicles. To protect the integrity of sensitive electronics and overall vehicle performance, automotive plastics need high dimensional stability and should maintain mechanical behavior even in extreme climates.
New regulations and legislations are setting the standards towards e-mobility for the future. As BASF we are well prepared with a bundle of expertise and know-how and are ready to support our customers.
AI: How can automotive plastics help protect the integrity of sensitive electronics and overall vehicle performance in terms of high dimensional stability and maintaining mechanical behavior even in extreme climates?
Bayerl: For critical applications such as those in automotive electronics, long life and reliability are basic requirements. It is often the case that the average operating temperature in modern electronic components increases, for example due to the trend toward miniaturization of electronics. Components are exposed to the waste heat from the drive system to a considerable extent. Naturally, the plastic parts should be functional in all climate zones on earth, even in damp hot conditions and have to resistant to spray water and road salt. Today, the specifications for a number of plastics can be fulfilled by hydrolysis resistant modified Ultradur grades.
AI: Sensors and cameras are key components to how well a self-driving car performs on the road. What is the best way to house and protect these systems from environmental elements?
Bayerl: Like sensitive electronic components, the sensors and cameras have to withstand hot and cold temperatures in all climate zones worldwide. They have to be resistant to media like spray water, oils or road salt. To protect these applications, a hydrolysis resistant Ultradur provides the performance that is needed.
AI: As the amount of technology needed to create a more personalized interior increases, is a lighter weight, more efficient vehicle still achievable?
Bayerl: Nowadays the electric powertrain is dominated by metal applications. Replacing these metal parts with plastics makes cars with hybrid, plug-in and electric engines more efficient. A further increase in the use of plastic components has the potential to compensate for the weight of the battery, and so increase efficiency. Engineering plastics and polyurethane systems for use in components around the engine, chassis and electronic components can save about 20 to 30% weight in these applications.
AI: Once the driver is no longer responsible for actively controlling the vehicle, how will materials make the passenger experience quieter, more comfortable and enjoyable?
Bayerl: With automated driving the car interior will become an extended living room. For improvement of NVH (Noise-VibrationHarshness), which is synonymous with comfort, BASF is offering an extended customized product portfolio out of polyurethanes and engineering plastics. Depending on the application and acoustic requirements various products or even components lead to more comfort and less noise. Applications like engine hood and head liner or processes like cavity filling made with polyurethane accompany and even enabling the evolution of e-mobility within interior, chassis, future powertrains and exterior. As another example: For chassis components the microcellular PU elastomer Cellasto® within a PA housing absorbs the movements and pushes of the street and makes driving more comfortable. In addition, disturbing noises which are caused by structure or air noise, can be significantly reduced using various interior and powertrain PU solutions.
AI: What’s next for BASF?
Bayerl: Alternative powertrains, fuel efficiency, lightweight construction, emission reduction, design flexibility, driver assistance systems. These are some of the trends that are driving the industry today and tomorrow.
High performance plastics, foams and plastic additives can provide tailor-made solutions for the automotive industry to accompany these trends. Plastics are a material of unlimited potential. They are so special because they contribute significantly to the quality of vehicles wherever they are used.
Interviewed: Dr. Thomas Bayeri, Segment Marketing Manager for Automotive E&E applications BASF
More Stories
Automotive Industries (AI) Newsletter April 2025
Bangkok International Motor Show 2025 – The Talk of Sensuous Automotive
Earn GHG reduction values through MOL Pure Car Carrier “Book and Claim (B&C)” service