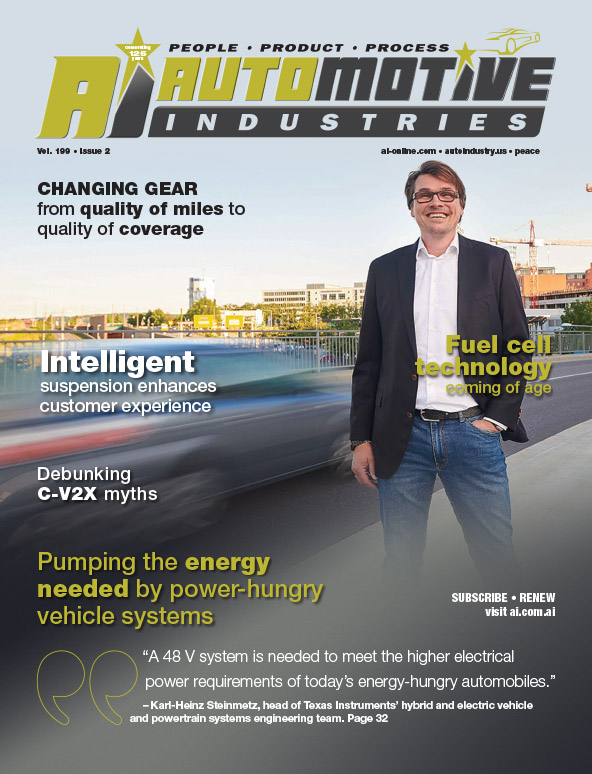
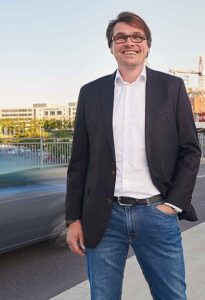
Just as the requirements of vehicle electrical systems outgrew what 6 Volt batteries could provide from the 1950s on, today’s 12 V systems are putting the brake on innovations that will improve the in-car experience, reduce emissions and increase safety.
Dashboards consisting of a mechanical speedometer and rev counter are now touchpads which open a world of connected appenabled multimedia infotainment systems. Mechanical distributors and carburetors have been replaced by energy-consuming engine control units linked to multiple sensors and actuators.
Electronic driver assistance systems are no longer reserved for premium models. Reverse sensors and cameras, tracking, adaptive speed control, automatic windscreen wipers and lights, emergency braking and blind spot monitoring are available through a number of classes. Making cars easier, and sometimes more fun to drive, are electronic power steering, electronic transmissions, electric turbochargers, traction control, and active roll stabilization. They combine to make increasing demands on vehicle electric systems.
Automotive Industries (AI) asked Karl-Heinz Steinmetz, head of Texas Instruments’ Hybrid and Electric Vehicle and Powertrain Systems Engineering Team, how the company is helping OEMs to meet the challenges of enhanced driver experiences, improved safety and lower emissions.
Steinmetz: Worldwide emissions regulations have made vehicle electrification a leading trend. To that end, we are helping our customers design reliable HEV/EV systems that boost efficiency and increase power density while meeting the industry’s vehicle safety requirements. Our products and systems expertise enable the highest monitoring and control accuracy, and efficiently transfer power and data for 48-V and higher voltage systems, while meeting functional safety standards.
At the same time, we’re progressing driver-assist systems that make driving safer through automation with the highest degree of accuracy, reliability and security. We’re also reimagining the in-vehicle experience by enhancing and personalizing advanced infotainment systems, body electronics and lighting with systems that enable optimal load driving and achieve the high thermal and size efficiency, while significantly reducing EMI.
AI: What are the practical benefits [of 48V] for OEMs and their customers?
Steinmetz: In addition to reducing harmful fuel emissions and increasing fuel economy, the increase in power offered by a 48-volt electrical system answers growing consumer demands for cars with high-tech infotainment, convenience and assistive driver-safety features. Fuel efficiency savings of as much as 20% are touted by some manufacturers of 48-volt electrical systems. And a possible 30% reduction in carbon dioxide may be achieved by 2025.
Benefits of 48V systems include:
- Gain efficiency by lowering carbon output and costs while increasing drive range
- Manage power loads of the heating and cooling systems and automated driving computers
- Replace lead-acid batteries with lithium-based batteries.
From a passenger comfort perspective, a growing number of manufacturers are fitting infrared heating panels that directly warm up passengers without wasting power heating up the remainder of the car — similar to putting on another layer of clothing to stay warm instead of turning the thermostat higher. The challenge with infrared heating panels is they require around 500 watts of power per seat, putting substantial strain on a 12-volt electrical system. This is not the case with a 48-volt system.
For vehicles with higher levels of autonomy and driver-assist features, the amount of energy needed by the onboard computers to analyze and act on data from sensors and cameras far exceeds the capability of today’s 12-volt electrical systems. Each onboard computer is expected to consume around one to two kilowatts of electrical power, which would eat up the power of a 12-volt system.
Whether future autonomous cars are hybrids or fully electric, they will need a 48-volt system to absorb such power-hungry loads.
AI: Will 48-volt systems replace 12V systems any time soon?
Steinmetz: A 12-volt electrical system delivers around 300 amperes of continuous power and about 600 amperes at peak, barely enough to power the standard starter, infotainment, semiautonomous safety features and braking, much less to handle the traction motor of a hybrid vehicle. A step change was needed.
Auto brands are rolling out mild hybrids with stop-start technology that enables the engine to momentarily shut off as the car coasts, brakes or stops before quickly restarting and is powered in part by the new system. Makers of lower-end mild hybrid vehicles are set to follow their lead this year.
The versatility of 48V shows promise because it is compact, power dense and lightweight. A 48V rail adds additional power along with the 12-V battery in combustion-engine systems to add torque to the drivetrain that enables some limited electric driving such as parking or coasting down the road. In hybrids and electric vehicles, it can help power the HVAC unit or electronic control units.
Some systems will be powered by a two-rail system with high voltage rail plus 12V or 48V while others will move to a three-rail system with high voltage plus 12V and 48V.
There’s plenty of debate on whether OEMs will adopt a 48V system now or if they will go straight to fully electric. We’re seeing it as a step-change, but whether our customers are designing a micro hybrid or an EV, we can help them at any level. A 48V system is needed to meet the higher electrical power requirements of today’s energy-hungry automobiles. The increased power also makes internal combustion engines operate more efficiently to help manufacturers meet emission regulations more quickly.
AI: What is a combo-box architecture?
Steinmetz: A combo-box architecture is an integration of multiple applications like on-board charger, DC/DC converter and traction inverter into a single box. Integrating powertrain endequipment components enables you to achieve:
- Improved power density
- Increased reliability
- Optimized cost
- A simpler design and assembly, with the ability to standardize and modularize.
AI: Can wireless technology improve car design and manufacturing (wireless BMS)?
Steinmetz: Battery management systems are evolving. Wired BMS is the standard today, but innovations are in progress to replace wired, daisy-chain connections with a secure, wireless protocol. Wired battery management systems are tried, true and not going anywhere soon, but wireless BMS are the next evolution. In fact, with Strategy Analytics estimating 36 million EVs on the road by 2026, wireless BMS offer promising ways to make vehicles more efficient and reliable – features that appeal to both original equipment manufacturers and consumers.
Removing cabling provides many advantages including reducing weight, providing a more compact design and reducing the maintenance that’s typically involved with the wiring harness. Collectively, this improves power density and boosts reliability and efficiency.
Although wireless communication is already replacing cables in various applications, one critical point to consider is the reliability of the wireless link and network. Two of the main variables you can use to quantify reliability are packet error rate and the probability of successfully sending a message between a transmitter and a receiver. This probability should be 99.999% or greater with a packet error rate of 10-6.
In terms of passenger safety, a wireless BMS should accurately monitor conditions and respond quickly, reliably and safely if a hazardous event is detected to mitigate danger or destruction.
Ideally, the system should meet requirements up to Automotive Safety Integrity Level D, which is the highest functional safety goal defined by the International Organization for Standardization 26262 road vehicle standard.
More Stories
Professional vs. DIY Tinting: What You Should Know
New updated edition of “PXIMate” reference guide for T&M engineers available from Pickering Interfaces
5 Mistakes That Can Ruin Your Car Accident Claim