
Automobile design has turned a full circle – around 1885 electric vied with internal combustion-driven vehicles for market share. An electric vehicle held the world speed record until 1900 (46,47km/h by Andrew L Riker). In 1900,38% of cars on the road were electric, and 40% were powered by steam.
Now it would seem that the days of the liquid-fueled internal combustion engine as king of the road are numbered. Patented in 1794 by Robert Steel, it took another hundred years, until 1885, for Karl Benz to market the first practical automobile to
be powered by an internal combustion engine. The next evolution was triggered in 1963, when the United States introduced the first automobile emissions standards.
This sparked a revolution in powertrain design thinking, with the focus shifting from pure horsepower to efficiency.
Standards have since been tightened around the world, with the European Economic Community in 1977 becoming the last major industrialized market to enact emission restrictions. China, India and most other relatively newly industrialized countries around the world have followed suit.
Today’s focus on electric powertrains is being driven by emissions standards which are tightening around the globe. The main challenge – as it was in 1900 – is range. Advances are being made in battery technology, but even more rapid perhaps is the development of lightweight materials. Weight is a determinant of ange. Put simply, the higher the power to weight ratio, the farther the vehicle will travel.
Automotive Industries (AI) asked Francis Defoor, Global Market Segment Leader Transportation, Hexion Inc., to share some of the recent breakthroughs in composite design.
Defoor: Thermoset composite materials based on epoxy, phenolic or polyester resins have been used for many years in passenger cars in suspension components, structural parts and body components such as roofs and liftgates.
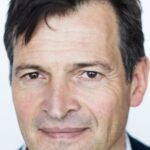
Segment Leader Transportation,
Hexion Specialty Chemicals.
With the automotive industry moving to the electrification of the powertrain, there are new exciting opportunities emerging for composites. We see a renewed interest in lightweight solutions to extend the driving autonomy.
Specifically, for the higher end segments, composites provide unique solutions for the protection of the Li-ion batteries, and combine ballistic impact resistance and fire resistance. In the meantime, the industrialization of composite materials has continued and today the important milestone of a built rate of more than one million parts per year has been accomplished with epoxy composites.
Looking at the other sectors, enormous growth of composites in the wind industry has been made possible by the cost-effective production of wind blades with a blade length of up to 100 meter having dynamic fatigue properties that withstand the natural elements for decades in on-shore as well as off-shore conditions. In aerospace the fuselage and other primary structure parts are increasingly made from lightweight composite materials to reduce fuel consumption and total cost of ownership. The automotive industry is next.
AI: How do composites compare with metals when it comes to performance?
Defoor: Composites’ specific strength and stiffness are around 9 – 10 times higher than steel and aluminum alloy and offer engineers and designers significantly greater design freedom given the wide range of available resin and fiber formats and compatible manufacturing processes.
Chopped random fiber formats like sheet molding compound (SMC) with isotropic properties provide the greatest flexibility for molding complex geometry parts, while continuous glass or carbon fiber epoxy components manufactured by high pressure resin transfer molding (HP-RTM), liquid compression molding (LCM) or prepreg compression molding (PCM) allow engineers to optimize structural component designs by utilizing the anisotropic properties of continuous fiber.
Epoxy composites are typically used in body panels, sometimes for aesthetic purposes, but more often now for structural components to improve passenger safety, vehicle stiffness and to improve driving dynamics. In all cases significant weight reduction is achieved. Composites are also imparting dynamic fatigue properties sought after in suspension and other applications. The same unique performance can take the additional load from heavy battery packs and effectively protect them against intrusion.
Battery trays or structural parts of the BIW avoid battery damage in case of a crash. Bolt-on underbody panels or skid plates are considered as an alternative battery protection strategy.
AI: Are there any other unique characteristics?
Defoor: Engineers are sometimes surprised to learn that composite materials in many cases will outperform traditional metal solutions for requirements like fire resistance (of key concern for EV battery enclosures) and chemical resistance.
Composites also allow for lower tooling cost relative to steel and aluminum, while providing greater potential for functionality integration.
AI: One of the challenges with composites is the supply chain. How do you address this?
Defoor: About five years ago many suppliers and OEMs were evaluating composites as a light weight material. Their purpose was to meet the more stringent emission targets by reducing vehicle weight. Since that time there have been many pre-production projects where raw material suppliers, equipment producers, engineering companies and part producers have developed innovative solutions. New fast-cure and high productivity composite material systems are now qualified at a number of Tiers and OEMs and engineers can design with these materials using standard CAE tools.
Having sufficient access to carbon fiber was a significant concern five years ago. Today there are multiple commercial sources of large tow carbon with adequate properties and cost for the mid to premium segment. Recycled carbon and glass fiber also have found their place. The high upfront investment required for new high rate production composite manufacturing technologies has been an impediment to technology adoption, but a number of large-scale operations have now launched successfully in multiple regions. The Tiers that have invested in equipment have also built up a full engineering suite to design parts with their manufacturability in mind. All of this helped to bring the cost per part down to the target level and reached the technology and manufacturing readiness level of full maturation.
AI: Please tell us more about your SMC solutions.
Defoor: SMC is probably the most-used thermoset composite applications in automotive manufacturing. These are typically lightweight body panels and liftgates made from styrene-based polyester or vinylester resins. The industry has been looking for materials solutions with reduced volatile organic compounds (VOC) emissions that help to improve air quality both in manufacturing facilities and in the passenger cell (following i.e. VDA 278 norm).
During 2020 Hexion launched a second generation of epoxybased SMC that is styrene-free and ultra-low in VOC and can be processed on existing SMC compounding lines. It can be processed with any mixture of carbon or glass fiber and yields lighter parts with unprecedented mechanical properties.
It is arguably one of the most efficient ways to achieve a very high yield of the carbon fiber, and is cost-competitive to aluminum. This concept has successfully been applied in pre-development projects on thick and complex shaped parts such as cradles, brackets and suspension parts.
With a new phenolic resin SMC solution also recently developed, we have a game changer for battery cases that require fire resistance. The new safety standards in China and Europe require that passengers get enough time to evacuate an EV in case of a thermal runaway of the battery. Battery enclosures made from fire retardant materials play a critical role to achieve this.
The solution Hexion developed starts with an innovative phenolic resin with an ultra-low formaldehyde release, that again can be pro-cessed on most standard SMC lines and presses. It can be combined with a variety of short and continuous fibers and offers a unique balance of best-in-class fire resistance and mechanical properties comparable to aluminum. Weight savings of up to 40% can be achieved, which really makes a difference on these sizeable parts.
More Stories
Acoustic sensor systems and Fraunhofer measurement technology for in practical testing ͏
OSI Systems Receives $10 Million Order for Cargo and Vehicle Inspection Systems
Mitsubishi Electric Automotive America Launches Guardian Generation 3 Trial with Seeing Machines in North America