OEMs and their Tiers are ready to migrate to countries and regions which offer the lowest cost for the least carbon emissions when producing electric vehicles.
Automotive Industries (AI) asked David Stewart, Engineering Director, Research and Innovation at HSSMI, a sustainable manufacturing innovation consultancy,
what role giga factories will play in the future of the British auto sector.
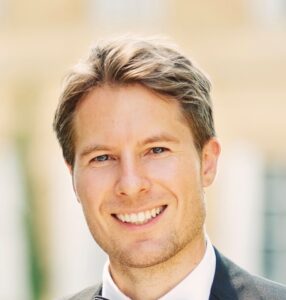
Stewart: They are very important for the future stability and growth of the UK automotive sector. The government’s green policies state that no petrol or diesel cars should be sold from 2030 onwards. OEMs are scrambling to hit these targets, and many have made commitments to have full electric derivatives of every vehicle they produce by this date. The battery represents the main powerpack to drive propulsion in these vehicles. Even if we make the move to hydrogen, they will still need a battery. OEMs therefore need to source them, and in big quantities. That is where gigafactories come in. If we don’t build the gigafactories, then we could risk losing our major automakers to the countries which are building gigafactories.
AI: Is the UK supply chain ready for electric vehicles?
Stewart: The ambition and plans to manufacture packs and EVs is there from the automakers. The gap at the moment is in supplying them with the right cells at the right price. The endof-life side needs further development – no dedicated facility exists yet. In terms of the issue of end-of-life batteries, there are encouraging signs from UK industry to build pilot plants to recycle these batteries.
AI: Is the “circular economy” the game changer in environmental sustainability that “big businesses” has been looking for?
Stewart: It should not be thought of as a game changer, but something that should intrinsically be done as good common sense. From an economic standpoint, why would you let the tremendous amount of value and energy spent on bringing those products into existence, to be wasted at end of life” The raw materials have a value, the man hours imparted on each product have a value, as does the energy. To recover this value through reuse, re manufacture and recycling makes good business sense.
AI: How efficient are the recycling processes around the raw chemicals used in battery innovation?
Stewart: There are several recycling processes that offer varying levels of efficiency and profitability. Hydrometallurgical has higher material costs as a result of chemicals used but is overall cheapest.Pyrometallurgical presents higher general expenses, utility costs, and is more labor intensive.”Direct recycling”, which relies heavily on manual disassembly offers the highest purity but also relies heavily on labor. In terms of the efficiency of the processes for particular metals, it is worth noting that no recycling process yields salts of sufficient quality or purity to be put directly into production. An additional point to consider is that material prices fluctuate strongly and recycling profitability is often not only determined by efficiency of process itself but by value of scrap material at particular point in time.
More Stories
What You Should Know Before Filing a Car Accident Claim
Injured in a Car Accident in St. Louis? Here’s What to Do Next
Historic Sportscar Racing (HSR) and Goodyear Announce Multi-Year Partnership