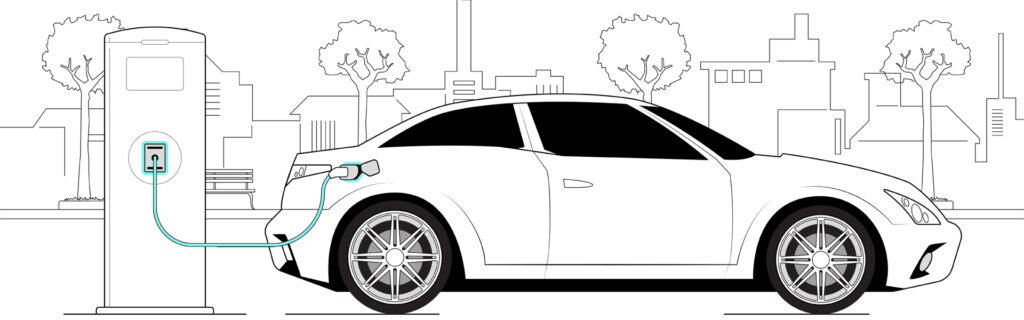
It seems the electric revolution is finally here. According to the
International Energy Agency
<https://www.iea.org/reports/g
ten million electric cars on the world’s roads already at the end of 2020 –
up 43% from 2019. By the end of this decade, the total number of electric
cars, buses, vans, and trucks is projected to jump to 145 million or
possibly even 230 million if enough countries tighten their emission
targets. Carmakers are investing billions to secure their slice of the
market. One of the challenges they face in building mass-market electric
vehicles (EVs) is fire safety. But probably not in the way most people
think.
Contrary to what action movies would have you believe, cars rarely burst
into flames. If they ever do catch fire, passengers usually have more than
enough time to walk away safely. That is why fire safety regulations for
cars are a lot less strict than for planes, trains, or even most electronics
used in homes. But now, with the advent of EVs, news reports of burning EVs
have caused new concerns.
Are electric cars at risk?
According to the US National Fire Protection Association (NFPA), electrical
failures are already one of the leading causes for fires in conventional
cars, accounting for one in four vehicle fires in the United States. With
EVs carrying high energy in their lithium batteries, it seems only logical
that they pose an even greater fire risk. Not so, says Sebastian Hoerold,
Head of Technical Service Thermoplastics & Market Manager Flame Retardants
at Clariant: >The fire risk of electric vehicles is not higher but different
from traditional cars with combustions engines.<
Not more but different risks
Electric power trains work at much higher voltages and currents. Most
conventional cars carry a twelve-volt battery to run the starter, lights,
and all onboard electronics. Even so-called mild hybrids, in which a
powerful electric motor supports the combustion engine, run on just 48
volts. In contrast, some all-electric vehicles have fast-charging cycles
that can involve 800 volts or more.
Then there are the differences in everyday use: Parking a diesel essentially
puts the car to sleep. But parking an EV usually involves charging it. >We
see some of the highest voltages and currents precisely as the car is
unattended,< says Hoerold. >That can be overnight in your garage or during
the day in a public parking area, say, underneath a busy shopping center or
an office building. It is this combination of high-energy batteries, high
voltages and currents during charging while being unattended that needs to
be considered in safety standards.<
High voltages, tight spaces
>Up until recently, the automotive industry was not much of a market for our
high-performing flame retardants. However, that is about to change
dramatically,< says Elmar Schmitt, Segment Manager for Clariant’s flame
retardant business. >In reinventing their product, carmakers will need new
materials with safety built in to deal with a whole new set of challenges
and requirements.<
First, there are the high voltages. These can cause short-circuits and
sparks that can ignite flammable materials. One of the ways to prevent such
failures is by design: Simply placing conducting parts further apart is one
strategy. Another is to encase components. But these approaches aren’t
always practical in car design. For one, cars are crammed with ever more
electric hardware. Spaces are tight. Components need to fit close together.
Adding material and assembly work to encase components drives up costs and
adds weight. >Carmakers have always been sensitive on these two fronts,<
says Schmitt. >Even small extra costs add up quickly, so does excess weight.
Every gram you can shave off an EV adds to its battery range, which is
currently one of the most important selling points.<
Resistant and lightweight
High-voltage plugs, connectors, bus bars and other electrical components
require high-performing polymers with high-performance flame retardants –
such as Clariant’s ExolitR. It has been in use for two decades in some of
the most demanding industries, from smart consumer electronics to home
appliances to industrial applications. Based on organic phosphorus
compounds, Clariant’s additives can stop plastics burning within seconds and
thus stop flames from spreading. It also helps minimize the risk of creepage
and sparks. >Exolit is non-halogenated, which makes it safer and more
environmentally compatible than most solutions out there,< says Schmitt.
>But it is the improved material performance that makes it especially
appealing to the EV industry.<
Adding Exolit to plastics does not affect or in some cases even improves
their electrical properties – measured as the Comparative Tracking Index
(CTI). >We enable manufacturers to reach Performance Level Category 0, which
holds for 600 volts,< Hoerold explains. >That way, conducting parts can be
fit closer together, allowing further miniaturization and weight cutting.<
Plus, Exolit itself adds remarkably little weight to the parts.
Harsh conditions
Then there is the matter of durability. Standard cars are expected to last
up to 200,000 miles. With fewer moving parts, EVs may get even more mileage.
However, that heavily depends on how well connectors, plugs, cables,
brackets, and the likes hold up to the constant stress caused by vibration,
extreme temperatures, UV light, corrosive liquids, dust and moisture. High
voltages and humidity can further exacerbate this stress through a process
called hydrolysis. >Over time, it can break down materials within the
polymer and lead to corrosion in the pins and connectors,< Hoerold explains.
>Exolit is hydrolysis-stable and can be used in dedicated hydrolysis
resistant formulations as well.<
Probably the most important draw to carmakers is how little the addition of
Clariant’s flame retardants affects a polymer’s other properties. >The
automotive industry has made an art of engineering cars to optimize costs,
production speed, durability, and so on,< Schmitt says. >They want their
polymers to perform the way they’re used to.< However, most flame retardants
make plastics more brittle, less workable, and even less durable overall.
Some make specific production processes harder or even impossible. >With
Exolit, we have carmakers covered,< says Hoerold. >For example, they are
very satisfied with the way it works with both laser welding and laser
marking. Plus, it affects the physical properties of the plastics as little
as possible.<
Aiding the revolution
In EVs, the color orange is a safety feature. It indicates high voltage
components and cables. Meeting and maintaining this specific standard color
throughout the entire lifetime of a car is crucial. Some flame retardants
can make it impossible to color parts accordingly. Exolit can be used for
any color. Other flame retardants can also cause heat-related discoloration
over time. >Our solution affects the color of the polymer less than any
other product,< Hoerold says.
It is clear that high-performing flame retardants are crucial in EVs. >The
industry standards and regulations on fire safety are not completely
finalized yet,< says Schmitt. >But we know that products such as Exolit will
have a role to play that goes beyond fire safety.< Combining high fire
safety standards and high CTI with good mechanical properties and
sustainable chemistry will help make electric vehicles more efficient and
reliable. That in turn will instill greater confidence in EVs and thus help
expedite the electric revolution around the world. It’s one of many ways in
which Clariant helps build a sustainable infrastructure and promote the kind
of immediate climate action we need to reach the Sustainable Development
Goals
More Stories
MESSRING completes new crash test facility for Mahindra in India
ROHM Develops an Ultra-Compact MOSFET Featuring Industry-Leading* Low ON-Resistance Ideal for Fast Charging Applications
More than 30 of the top 50 global suppliers have production facilities in Turkey