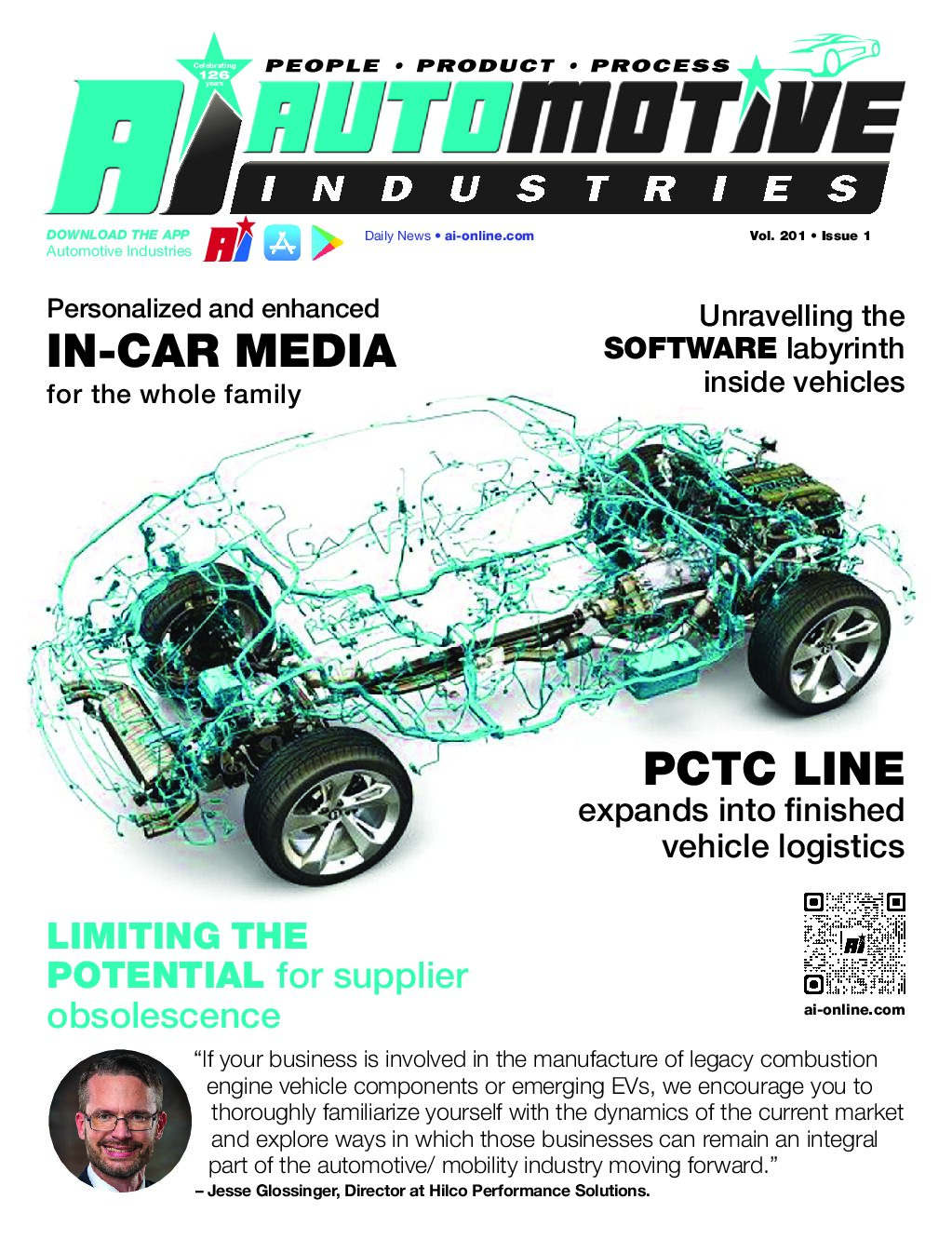
In this article we take a look at how the automotive industry’s transition to electric vehicles is creating unique challenges for auto manufacturers and placing existing supplier relationships at future risk.
In the automotive industry, as in others over the past several decades, we have seen manufacturers rely, in part, on a strategy of “planned obsolescence” to limit the duration of functional use and end-user desirability for their product offerings.
The purpose of such an approach is, of course, to reduce the amount of time that passes until a buyer is motivated to replace a maker’s product with a newer, seemingly better, model.
Since the early years of assembly line manufacturing, the automotive industry has implemented “trend-setting” design modifications to vehicles on an annual or recurring cycle to entice buyers.
From fender fins in the 1950s to air scoops and spoilers in the 60s and 70s, flip-up headlights in the 80s and panoramic sunroofs, matte paint finishes, retractable door handles and blackout tire rims in the 2000s, the list is expansive.
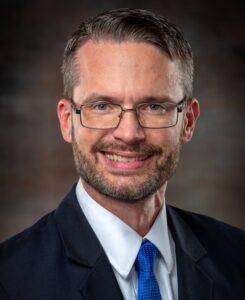
Simultaneous performance enhancements such as limited slip differential, front-wheel drive, turbochargers, anti-lock brakes, sport packages and fuel-efficient hybrid engines have also helped drive new vehicles off dealer lots and into consumer garages over the years.
Additionally, as cars age, the limited availability of spare OEM and alternative replacement parts compatible with those vehicles adds to the need for exploring a replacement vehicle.
Similar observations can be made for manufactured products ranging from vacuums to televisions, golf clubs and barbeques.
Most recently, the sunsetting of the 3G wireless connectivity network is contributing to automobile obsolescence for some makes.
Now, an unplanned obsolescence of sorts is occurring across the inner workings of the automotive industry and its supply chain as the car, itself, embarks on an unprecedented transformation from a human guided, internal combustion engine (ICE) propelled machine to a connected, autonomous, and electrified mobility device.
As this shift occurs, the business model that delivers this new form of engaged mobility to the customer is transforming as well.
Even though EVs make up only a small percentage of total vehicles on U.S. roads today, it is clear to most that the heyday of the ICE vehicle industry is likely coming to an end in the not-too-distant future due to government policy on climate change and advancements in battery technology.
General Motors has committed to making a $35 billion investment in electric and autonomous vehicles and introducing a minimum of 30 EV models through 2025.
In addition to making substantial EV investments, Ford Motor Company has announced plans to re-structure into ICE, EV, and Commercial business units.
Volvo, too, has revealed aggressive plans to transition to an all-EV company by the year 2030.
And Volkswagen has proclaimed that its mission is to become the world’s largest manufacturer of electric vehicles.
Multiple other automakers will eliminate new vehicles with gasoline and diesel engines entirely over the next 15 years.
For large manufacturers transitioning to these new platforms, the companies that supply them, and the infrastructure that supports the use of the vehicles they create, the impact will be significant.
Take, for example, suppliers of catalytic converters, exhaust assemblies and gas tanks.
In the world of electric vehicles, these parts have no functionality.
So, what does this mean for the future of their businesses?
For one thing, it means certain disruption to the way they have been doing business for years and in many, if not most cases, to the products they have been producing and supplying to the industry.
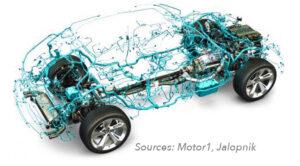
No example hits to the heart of the industry more than the fact that differentiation strategies will have to shift from power and performance prowess to effortless customer experiences and smart technology.
This disruption presents growth opportunities for the savviest suppliers.
It is important to also note that the experience of these companies in serving the evolving needs of auto manufacturers and their ability to innovate over the years to keep pace, bodes well for their future existence.
Furthermore, because legacy auto manufacturers on a global basis are proceeding toward an EV future with a keen eye still firmly focused on maintaining critical revenue from their internal combustion vehicle lineups, suppliers have some time in which to evolve.
Additionally, mass adoption rates of battery electric passenger vehicles in regions such as India, Southeast Asia, and Africa will likely be well behind that of China, Europe, and North America, thus preserving a global market, albeit smaller, for ICE componentry.
Regardless, with the world’s leading auto manufacturers having committed to aggressive timelines, the clock is ticking.
This, in turn, places notable pressure upstream on suppliers. In essence, it requires them to follow a relatively parallel course to ensure both their current revenue stream and their own future existence as the EV market heads toward an anticipated 16% share of the total U.S. auto market by 2026, according to research firm, AutoForecast Solutions.
Successfully bridging this period between the current and future state of the industry, requires auto manufacturers and their supply chain partners to not only develop new, EV platforms, componentry, systems and software, but to do so while also continuing to update existing ICE models and even introduce some new ones in order to maintain market share and profit targets.
This need has, by necessity, led to a blended manufacturing model with new or retooled plants coming online to handle the transition.
Due to the continued long-term relevance of their components, some suppliers, such as braking, steering and lighting system manufacturers are generally considered as well positioned to remain an integral part of an EV-driven automotive future.
Others, such as drivetrain, exhaust, engine component and other suppliers face greater risk of obsolescence.
Here, the extent of their own innovation and ingenuity will likely determine whether they evolve with the industry or cease to play a part in its march forward.
Might some of those suppliers’ components be adapted to help cool EV batteries, ventilate and control the temperature of passenger compartments, or help carmakers solve other challenges associated with delivering EVs with comfortable passenger compartments and long-range capabilities?
Additionally, as we have already seen with EV-only car companies such as Tesla and Lucid and to a certain extent with makers that have introduced EV models including Audi, Jaguar, Ford and GM, software and electronics are replacing most of the mechanical components utilized in legacy vehicles.
Along with this shift comes the need for a completely different vehicle architecture, one that does not rely upon a labyrinth of wires and cables, linked to dozens of independent electronic control units throughout the vehicle to collectively operate those mechanical systems. Instead, fewer, more powerful control units are already being utilized to bring extensive functionality to these vehicles’ feature-laden, software stack and firmware-driven systems.
While the need for these new, more computationally powerful CPUs creates opportunity for some suppliers, the sizable reduction of distributed wiring/cabling throughout future vehicles reduces opportunity for others.
These two examples, among the many other changes that are taking place as part of the EVs evolution, illustrate why it is so critical right now for those across the supply chain to determine what role their businesses can best play in the future of mobility and what steps they will need to take to ensure they are able to do so effectively.
Another important consideration and a risk for some suppliers is the fact that manufacturers are struggling to overcome the engineering constraints associated with what has traditionally been a heavily siloed development approach.
As the technological complexity of vehicles increases, the need for their systems to be developed from a more holistic architecture standpoint also becomes more critical to achieving success.
Two cases in point: Tesla has taken control of development of its own custom self-driving semiconductor chips, while Volkswagen is building a massive software development infrastructure to serve its various brands.
With this in mind, we expect to see others take steps aimed at more fully controlling the production and integration of electronics and other components, systems, and software in their vehicles.
Strategies for accomplishing this will vary but may well include more formalized joint ventures and partnerships with certain suppliers, as well as potential acquisitions of others.
The automotive industry is on a long march toward a future which, will no doubt, look and operate much differently than what we experience today.
While fully autonomous transportation for the masses, where vehicles are in constant communication with the road they are on and the cars they drive alongside, seems to be a long way off, the transition to electrification is happening now and must be addressed on a more immediate level.
Auto manufacturers and their suppliers must figure out how to reinvent not only the products they bring to market but the way in which they will ensure their timely arrival and suitability to an evolving consumer appetite for environmentally friendly, convenience-oriented mobility.
If your business or a business within your portfolio is involved in the manufacture of legacy combustion engine vehicle components or emerging EVs, we encourage you to thoroughly familiarize yourself with the dynamics of the current market and explore ways in which those businesses can remain an integral part of the automotive/ mobility industry moving forward.
With that in mind, questions you should consider asking today include:
- Does your business strategy have enough optionality and flexibility built-in?
- Can your existing manufacturing process and facilities be utilized or retooled to produce components critical to this future?
- Is there industrial equipment, a plant, or technology available for purchase that could help jump start that process?
- Do you hold proprietary patents, licenses or other intellectual property that could be monetized to help acquire technology, tools, or staff in order to secure your position as a valued supplier moving forward?
Hilco Performance Solutions (HPS) helps companies simplify and streamline business processes, and improve operational efficiency to stay competitive and gain market share in an increasingly interconnected economy.
Jesse Glossinger is a Director at Hilco Performance Solutions. He is a business transformation, finance, and strategy leader with over 20 years of experience in the automotive and financial services industries, including four years of international experience in Shanghai. He can be contacted at: jglossinger@hilcoglobal.com
More Stories
Buying Car Insurance in Toronto? Don’t Make These Rookie Mistakes
What You Should Know Before Filing a Car Accident Claim
Injured in a Car Accident in St. Louis? Here’s What to Do Next