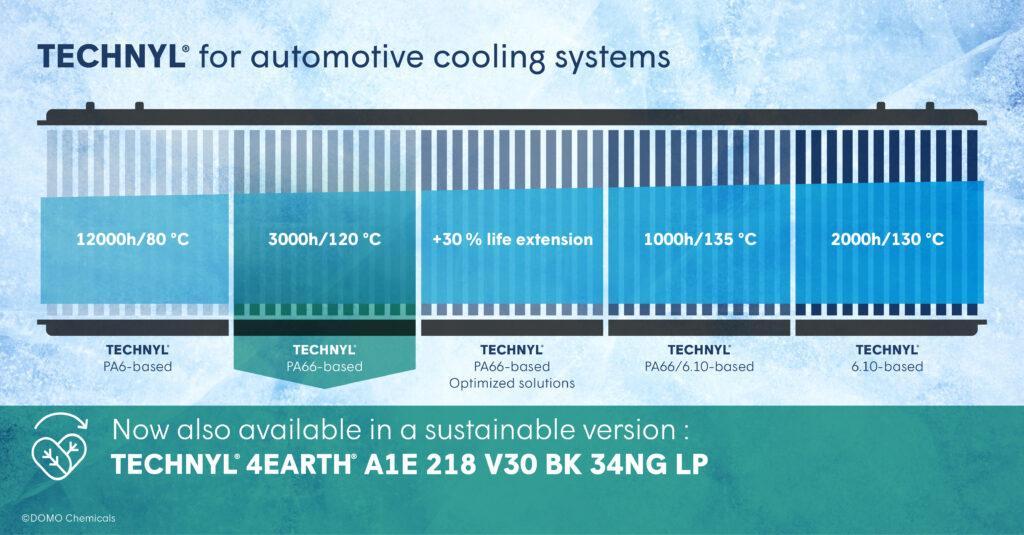
Recent developments in lightweighting, metal replacement, thermal management and e-mobility have reinforced the global need for sustainable and high-performance polyamide-based solutions.
One of the leaders in polyamide-based engineered materials solutions and services the automotive market, among others, is Belgium-based DOMO Chemicals. Automotive Industries (AI) spoke to Louise-Anne Fillot, Product and Application Development Manager for Automotive Market at DOMO, and Maarten Veevaete, Director Application Center at DOMO Chemicals.
AI: How is DOMO supporting the shift to a low-carbon automotive manufacturing economy?
Fillot: We start by ensuring we have a complete understanding of the new applications. We develop tests for samples or parts and can perform advanced simulations. This expertise, associated with our formulation expertise, is a key contribution we bring to our customers.
AI: How do you leverage your portfolio of products?
Fillot: Customers can benefit from a complete portfolio for cooling applications, starting with our well-established PA66-based solutions with improved coolant resistance TECHNYL® A 218 V30 34NG
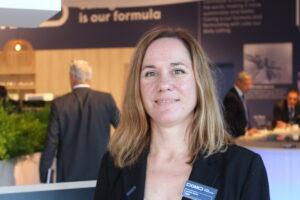
We have a new, sustainable variant produced with recycled polymer: TECHNYL® 4EARTH® A1E 218 V30 BK 34NG LP.
It exhibits coolant resistance at a level similar to our virgin-based reference TECHNYL® A 218 V30 34NG product, and meets all standard requirements for e-vehicle cooling applications, as well as combustion engines with cooling temperature requirements up to 135°C.
We also have PA6.10 or PA66/6.10-based solutions for outstanding performance, plus a new PA6 solution developed specifically for e-vehicles that has been successfully tested after coolant ageing for 12 000h at 80°C.
DOMO is able to perform predictive simulations with high accuracy based on in-house developed high quality material data cards, both for our TECHNYL® products, and our sustainable TECHNYL® 4EARTH® product range. This is unique in today’s market.
In addition to our simulation capabilities, the DOMO APT laboratory allows customers to evaluate the performance of parts under real-life conditions including fluid or hot air circulation under controlled temperature and pressure, vibrations or specific loading conditions. We can also develop molded demonstrators or produce prototypes with 3D printing.
So, we really complete the loop from product formulation to the final application.
AI: How sustainable is the new product?
Veevaete: As all other TECHNYL® 4EARTH® branded solutions, it has a lower CO2 footprint because it is based on recycled material. DOMO has a technological leadership in transforming post
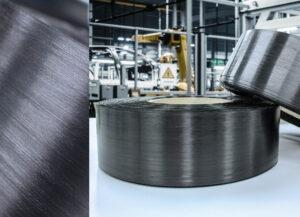
-industrial technical textiles from the production of automotive airbags, carpets, clothing and film for the packaging industry into premium-quality engineering plastics.
Different recycling technologies are used depending on the feedstock, offering environmental benefits while still providing top-quality products and solutions with technical performance comparable to traditional TECHNYL® Engineered Materials grades. The recycled feedstock, the selected processing technology or the energy mix at the production facility all influence the final CO2 footprint.
TECHNYL® 4EARTH® reduces the environmental impact of polyamide parts to levels never before achieved. We provide specific life cycle assessment (LCA) for all our materials, which helps our customers to select the most suitable sustainable solutions for their applications.
AI: What are the new extrusion solutions for EV cooling and air conditioners?
Fillot: TECHNYL® SHAPE is specifically designed for extrusion solutions for air conditioning and electric vehicle (EVs/HEVs) cooling circuit lines. Depending on the burst strength requirement of your application, DOMO experts will suggest the most suitable solutions within the TECHNYL® SHAPE product family, selecting among PA6, PA6.10/PA66 and PA6.10-based solutions, all with high barrier properties to refrigerants. What is important is to have a full picture of how the system behaves and that’s why we pay so much attention to the testing and the validation of the whole system, and not only measuring properties on ISO specimens.
AI: What about lightweighting?
Veevaete: Chassis and body structure lightweighting solutions offered by TECHNYL® can replace metal components. TECHNYL STAR® is a high strength, high flow polyamide, while TECHNYL® MAX is a robust, glass fiber reinforced polyamide. These formulations are well-suited for structural components such as transmission and motor mount cross beams, battery system mounts, air shutter grills and seat structures, as well as alternator and stator parts, and battery casings.

We are also working at fuel cell technology applications such as high-pressure hydrogen tanks. Based on a patented PA6 technology with excellent melt stiffness for blow molding and extrusion applications, DOMO is able to provide compounds with optimal processing properties, superior hydrogen barrier properties as well as excellent low temperature impact behavior.
The newly launched TECHNYL® LITE offers solutions for the outer protecting layers of those high-pressure tanks. To produce TECHNYL® LITE, DOMO is using another patented PA6 technology to impregnate endless glass or carbon fibers. The unidirectional tapes show outstanding mechanical properties which make them extremely suitable for the outer protective layer of high-pressure hydrogen tanks. In this way the complete high-pressure tank are made out of PA6, combining lightweighting aspects with increased recyclability.
TECHNYL® LITE is also suitable for other new mobility applications or sports and leisure applications. Due to its outstanding mechanical performance, its higher temperature resistance and improved bonding characteristics, TECHNYL® LITE is the material of choice for all kind of sustainable metal replacement and lightweight applications.
AI: What about the circular economy?
Veevaete: Most of the established large volume recycling grades available on the market are based on post-industrial feedstock. The ultimate goal of circular economy is to have automotive components being recycled for use in automotive applications at the end of life. For this, you need to have the right supply chain in place to ensure that you can track the materials throughout their life.
We are working with OEMs, brand owners and the Dutch startup Circularise, on establishing the systems needed. The goal is to allow a fully transparent supply chain through blockchain technology, allowing for a much easier collection system at the end of life of final parts.
The idea is to develop a digital twin of every batch that we produce. This is captured in the Circularise app, which shows the information needed by the consumer and the OEM, without disclosing sensitive information. The identifier for each batch will show the producer, the content, origin of the material, its environmental footprint and certifications.
For DOMO, this means we can supply our customers with all the information needed to back their sustainability claims. Meanwhile, another goal has also emerged: to be able to track the parts molded with DOMO materials and to recover them for reuse. We strongly believe that such a system could make the difference, but we are also well aware that a common effort within the whole industry is needed.
DOMO’s track record and market leadership in recycled polyamide compounds will help accelerate those developments. We are working on pilot studies to establish the feasibility of new mechanical and chemical recycling technologies for end-of-life parts, and using the recycled polymer and fillers for automotive applications.
AI: What is next?
Veevaete: Domo will continue working with our customers to develop materials for new mobility requirements. The automotive world is busy transitioning from internal combustion to battery or hydrogen-powered vehicles. Whichever technology is selected, polyamides will keep playing a key role because of their properties. The technology transition is facing many challenges such as lightweighting or new cooling requirements – for which DOMO has an extended TECHNYL® product range available. We will continue extending our sustainable TECHNYL® 4EARTH® product range to provide sustainable alternatives for internal combustion engine and e-mobility applications.

More Stories
RAM Trucks in Toronto: Why CarHub North York Chrysler Delivers the Best Experience
Acoustic sensor systems and Fraunhofer measurement technology for in practical testing ͏
OSI Systems Receives $10 Million Order for Cargo and Vehicle Inspection Systems