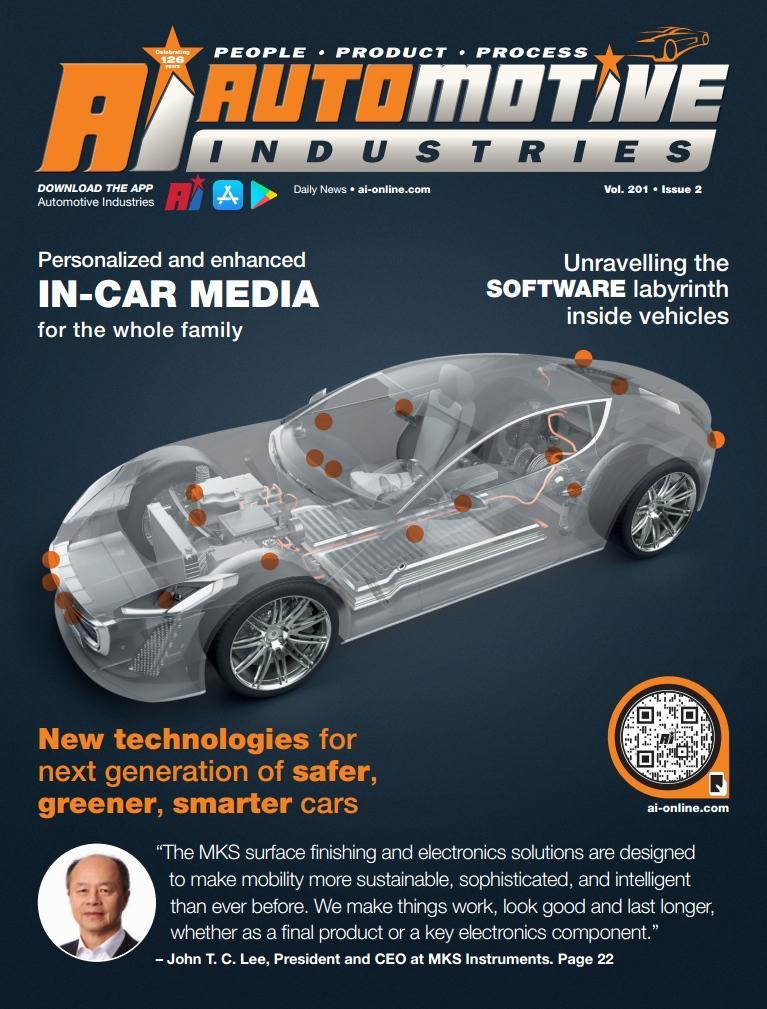
The future of mobility lies in vehicles that are safer, smarter and greener than ever before.
Critical to this transition is the development of new technology for a range of applications and components, including decorative and functional surface finishing solutions, lidar, night vision sensors and optics, and measurement of laser beams.
Automotive Industries (AI) asked John T. C. Lee, President and CEO at MKS Instruments, how the company is responding to these needs.
Lee: The MKS surface finishing solutions are designed to make mobility more sustainable, sophisticated, and intelligent than ever before. Our chemical solutions enhance durability, improve appearance, and create electrical conductivity and functionality. We make things work, look good and last longer, whether as a final product or a key electronics component.
MKS recently acquired Atotech, a global leader in process chemicals, equipment, software, and services for printed circuit boards, semiconductor packaging and surface finishing. Our goal is to be the leading supplier of surface finishing to the automotive industry, and to collaborate closely with the industry to further develop current standards. We also help drive design decisions, durability standards, and enable electrification and autonomous driving.
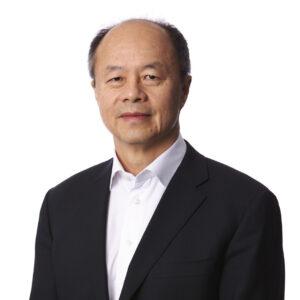
One battery pack, for example, can have 15,000 and more welded electrical contacts to connect the individual cells to a pack. We enable manufacturers to proactively monitor the laser beam making these welds, leading to higher quality, less scrap and thus higher sustainability.
Plus, precision welds mean the battery packs last longer.
Once the battery packs are produced, our gas analyzer is used to detect and speciate emissions from lithium-ion batteries to help ensure the quality and make them safer.
On the road, our highly accurate thermal imaging night vision systems maximize performance and minimize the risk of collisions.
AI: Please tell us more about your customized solutions.
Lee: Customization is a fundamental MKS strength. Essentially every semiconductor in the world is manufactured with MKS equipment. We have applied this focus on innovation and solving our customers’ most difficult problems in all the markets we support.
For example, we are modifying the size of our laser sensors and recalibrating them to enable laser manufacturers and system integrators to use them in automated laser cells. We also collaborate directly with automotive manufacturers on the development of individual laser measurement devices for new production lines.
Our customized surface finishing solutions facilitate new design opportunities and provide ideal functionality. With our OEM-approved technologies, we provide the right solution for decorative finishes, corrosion or wear resistant coatings as well as electronic components such as engine control units, ICE powertrains, info/entertainment, Advanced Driver Assistance Systems (ADAS), electronic powertrains or LIDAR and RADAR systems – whatever our customers need.
AI: How do you work with OEMs and Tiers?
Lee: Following the acquisition of Atotech, we offer the largest product portfolio, technical support and services in the market, through 15 global TechCenters, strategically located chemistry and equipment plants, and on-site customer support and consultation.
Our OEM teams understand the needs of OEMs and Tiers and collaborate with their development teams to create new manufacturing solutions, develop new automotive standards and engage in R
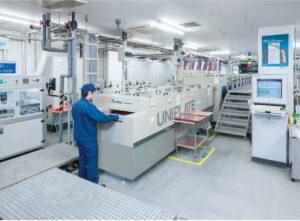
&D as needed. Customers worldwide value our comprehensive systems-and-solutions approach, innovative chemistry, world-class products and equipment, and superior service.
New processes are first tested in our laboratories and then in our TechCenters. For beta-phase testing, the process is used on a customer’s plating line, with all samples tested first by us and then by the OEM for approval.
AI: How do you help ensure consistent quality and minimize defects?
Lee: Our TechCenters offer a host of services, from routine analyses to customized examinations of samples. We collaborate closely with OEMs, customers, and industry partners to undertake sampling, prototyping, and pilot productions under production-scale conditions. We share our knowledge with our customers and industry partners through hands-on training in our TechCenters worldwide.
Our analytical and materials science laboratories handle all kinds of product quality and reliability testing, including performance tests. They are carried out in accordance with international standards and OEM specifications.
For the production line, MKS supplies a wide range of Ophir® laser measurement devices. Many of them are integrated in laser systems or automated production cells to ensure the lasers are operating according to the customer’s specifications. The ability to measure the quality of laser beams is vital to ensure that lasers used for welding, cutting or brazing consistently produce high-quality products.
Our measurement solutions are also key when it comes to laser-based sensing applications such as LiDAR and gestures recognition. Ophir measurement devices ensure eye safety and energy efficiency.
We also provide several products used in light and heavy-duty vehicle engine design, testing and certification. Our gas analyzer simultaneously measures, in a benchtop environment, multiple compo
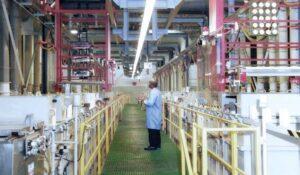
unds found in exhaust gases, providing engine manufacturers and testers comprehensive insight into the exhaust composition ensuring pollutant and greenhouse gas regulations are met. Our differential manometers measure pressure for engine and emission testing and internal car air leakage.
Our gas analyzer is also used to detect emissions from lithium-ion batteries, before and during a thermal runaway event, providing an important understanding of the breakdown mechanisms and enabling development of new battery designs that can reduce fire/safety hazards.
Our pressure measurement devices, manometers and gauges are used in various applications, including engine testing and certification and for thermal deposition of aluminum on headlamps, hubcaps and any other aluminum coated car parts, and anti-reflective materials on windshields.
AI: What is different about your approach to night vision?
Lee: As the largest automotive IR thermal optics supplier for the European automotive market, our lenses are integrated in the night visions systems of top European cars, with an installed base of hundreds of thousands of lenses.
For maximum performance and minimal collision risk, thermal imaging night vision systems must achieve high accuracy and allow for long distance object detection to provide the driver with sufficient response time.
The key to meeting these requirements is the use of high sensitivity and high-resolution optics – such as MKS’ athermalized lenses from its Ophir brand. Using innovative optical and mechanical designs, Ophir lenses allow for full operation in all environmental conditions, while also featuring a compact size and competitive costs.
MKS’ optics increase pedestrian recognition software performance, allowing a greater ability to anticipate potential hazards. The Ophir IR thermal imaging lenses feature the highest quality components and materials, designed especially to meet the needs of the industry.
AI: Anything you would like to add?
Lee: Solving difficult problems has been a core competency of MKS for over 60 years and the problems sets across our businesses are getting even harder. We are involved in everything from the semiconductors that power smartphones and artificial intelligence the lasers that enable eye surgery, to the chemistries critical to packaging chipsets for advanced electronics, and the chemistries and equipment for surface modification in the automotive and other consumer industries.
One thread common to all of the applications we serve is that the problems we solve are very difficult. Few can deliver the differentiation and precision required for the best solutions to those problems. By best I mean the solutions that not only best meet a customer’s product specifications but do so cost-effectively and at the highest yields.
More Stories
Buying Car Insurance in Toronto? Don’t Make These Rookie Mistakes
What You Should Know Before Filing a Car Accident Claim
Injured in a Car Accident in St. Louis? Here’s What to Do Next