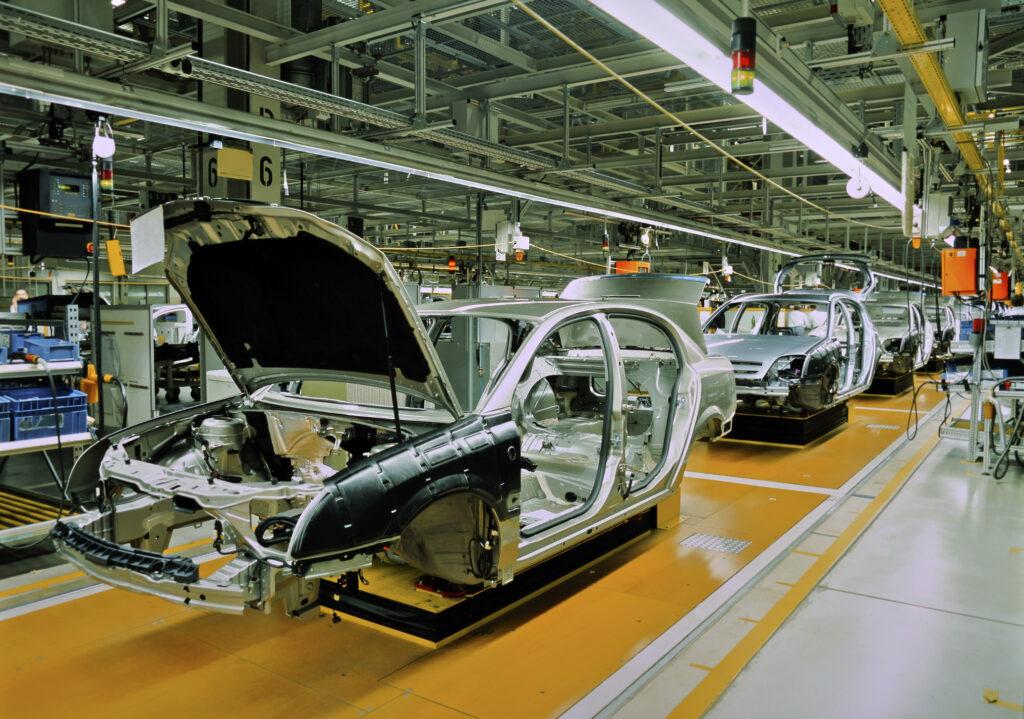
unfinished automobiles in a car plant
The Covid-19 pandemic highlighted how easily global supply chains can be
impacted by economic, environmental, and geopolitical forces. Now, many in
the automotive industry are looking to strengthen their supply chain
resiliency and better manage costs by moving their manufacturing operations
closer to customers.
As automakers consider nearshoring opportunities, it’s important to keep in
mind: the automotive supply chain looks very different than it did
pre-pandemic, and there are key strategies to consider when nearshoring and
trying to rebound production while saving costs. Pre-pandemic logistics
strategies are no longer as effective as the industry faces pressure to
recoup increased operating costs from the past three years.
Key Changes
Throughout the pandemic, the automotive industry saw significant inventory
and shipping challenges. Among top automakers, it wasn’t uncommon to exceed
logistics budgets by up to 200% due to high fuel costs, shipping rates and
dwell times. Now, automakers are faced with economic uncertainty and are
conflicted about keeping excess inventory when demand is so uncertain.
To remove some of this global volatility from their supply chains, many
manufacturers have nearshored to Mexico. In fact, throughout 2022, Mexico
experienced 12% FDI (Foreign Direct Investment) growth across 13 states due
to nearshoring efforts, the largest growth in the last 7 years. And the
highest jumps were in states where automotive manufacturing is historically
strong, including Monterrey which produces more than 20% of all auto parts
in Mexico. The National Association of Auto Transport in Mexico expects to
grow 20% in the next 4 years due to nearshoring efforts.
However, nearshoring doesn’t automatically protect from supply chain
disruption and increased costs. Every region comes with unique shipping
factors. Here are some things automakers must consider when assessing if
nearshoring is right for their operations:
The shipping environment of your new location. Every market comes with its
own unique challenges for shippers to consider. When determining a location
to shift operations, it’s important to understand the new factors that would
impact the supply chain.
For example, physical security is a bigger concern in some regions than
others. To mitigate the risk of losing cargo due to theft, diversifying
routes and border crossing locations can prevent repeat theft and delayed
shipments. Without completing a full assessment of the shipping
infrastructure, things like this can be missed and leave shipping operations
less efficient or more vulnerable to risks than before the move.
Customs and tariffs changes. Customs can make any international move
complex, but it’s important to understand the costs and trade procedures
that come with shipping from a new location. Moving from China to Mexico,
for instance, can come with tax incentives but only if certain requirements
are met.
To reap the rewards of USMCA, the free trade agreement between Mexico,
Canada and the U.S., companies need to meet a burden of proof that
manufacturing processes are making significant product changes before they
are shipped across the border. And because trade policy can change often,
it’s important to establish a trusted, knowledgeable partner for customs and
compliance before making the move to ensure cost savings is possible.
Cost. It’s easy to assume that moving manufacturing operations closer to a
product’s final destination would lower shipping costs, but that isn’t
always the case. Because of the complex global shipping environment and the
state of supply chain infrastructure in any country, ground transportation
can be equally as expensive as shipping containers across the ocean. This
spring, the cost of a truck from Mexico to the U.S. may be more expensive
than a container shipped from China to the same location.
One of the most significant cost savings opportunities from nearshoring can
be from decreased demurrage and detention charges. During significant dwell
times at the ports, automakers spend thousands of dollars from delays in
ocean shipping, often up to 30-40 days. If that same shipment was arriving
via truck from Mexico, it may only take 3-5 days and mitigate the risk of
delay. However, the cost of storage also needs to be considered since
transit times have been shortened significantly.
Assessing the cost variations that come with relocating operations is
important to understand the overall impact of nearshoring. For many
automakers, reduced risk of delay is worth a lot of money. Understanding the
overall cost of nearshoring requires a holistic look at the entire supply
chain so the decision can be made with all variables considered.
Flexibility is still crucial
The past few years have shown automakers the heightened importance of having
a supply chain that can adapt to changing situations.
Regardless of manufacturing location, no one can predict the future, and to
remain resilient, automotive supply chains need to be built with flexibility
in mind. For example, making sure all carriers aren’t based in just one
region can help protect shippers against congestion and geopolitical risks
in that part of the world. They can also leverage varying modes and routes
to ensure they can keep freight moving amidst disruption.
Working with a supply chain partner can help with understanding the varying
risks, costs, and opportunities that come with nearshoring. As automakers
consider nearshoring, it’s important to remember that flexibility is
necessary for every resilient supply chain and changing locations alone
can’t protect them from potential disruptions.
Mike Short is President, Global Forwarding at C.H. Robinson and Lynda
Andersen is Director, Automotive North America at C.H. Robinson.
More Stories
Professional vs. DIY Tinting: What You Should Know
New updated edition of “PXIMate” reference guide for T&M engineers available from Pickering Interfaces
5 Mistakes That Can Ruin Your Car Accident Claim