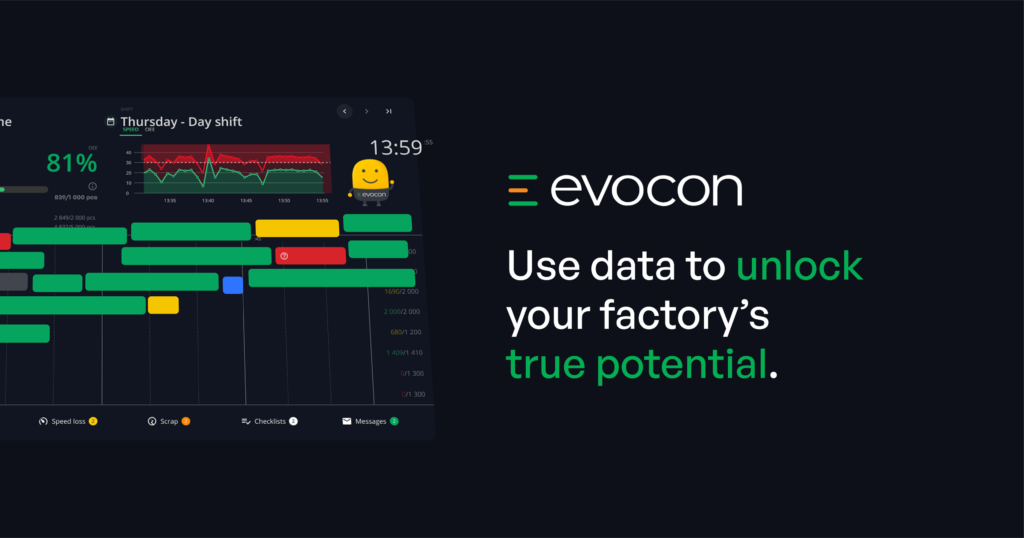
The rise of AI and companion technologies is dramatically reshaping factory operations. Dramatically is not a word we use lightly either. It is fair to say that the rise of AI, the Industrial Internet of Things (IIoT), and technologies like cloud computing are having as transformative an effect as Henry Ford’s introduction of the production line.
These advancements are setting new standards for productivity, quality, and sustainability in the automotive industry and across the entire manufacturing sector. This article explores how AI and other technologies are creating a new manufacturing world order.
The Role of AI in Modern Factories
Artificial Intelligence (AI) is a technology that always seemed to lie somewhere over the horizon. This all changed almost overnight with the sudden and dramatic emergence of generative AI.
This emergence has revolutionized factory operations beyond mere automation. Here are a few of the key ways that AI is helping to make factories smarter:
- Predictive maintenance: AI algorithms analyze data from machinery to predict potential breakdowns, reducing downtime and maintenance costs.
- Quality control: Advanced AI-driven inspection systems ensure higher accuracy in detecting defects, leading to improved product quality.
- Supply chain optimization: AI enhances supply chain management by forecasting demands, optimizing inventory, and streamlining logistics.
- Energy management: Intelligent systems analyze and optimize energy usage, contributing to more sustainable and cost-effective operations.
- Worker safety: AI-powered monitoring systems enhance worker safety by identifying hazardous situations and ensuring compliance with safety protocols.
It is worth noting that this list is far from comprehensive and the role of AI will continue to expand as the technology matures and becomes increasingly integrated into comprehensive factory monitoring systems.
Key Technologies Making Factories Smarter
AI is not a standalone technology when it comes to making factories more efficient. The current transformation is driven by a blend of complementary technologies that combine to amplify the capabilities of each individual component.
Key among these technologies are:
- Internet of Things (IoT): IoT devices collect vast amounts of data from factory equipment, providing the raw material for AI analysis. This data is crucial for predictive maintenance, quality control, and operational efficiency.
- Machine Learning (ML): As a subset of AI, ML algorithms learn from data, enabling factories to improve processes continuously. These algorithms are vital in areas like defect detection and process optimization.
- Robotics and automation: Robots, when integrated with AI, can perform complex tasks with precision and consistency. They are instrumental in reducing manual labor and increasing safety and efficiency.
- Cloud computing: Cloud platforms offer scalable storage and computing power, essential for managing the large datasets generated in smart factories. They enable real-time data analysis and remote monitoring.
- Edge computing: By processing data near its source, edge computing reduces latency and bandwidth use. This is crucial for real-time decision-making in fast-paced factory environments.
It is this “holistic” approach to factory floor management that is pushing the boundaries of what is achievable when it comes to efficiency, quality control, and sustainability.
The Role of Factory Monitoring Systems
Bringing these disparate technologies together to work as a cohesive unit is one of the major challenges facing factory managers. Central to achieving this is the role played by factory monitoring systems.
These systems are essential for getting the most out of the emerging technologies and among the key roles they are:
- Real-time monitoring: Factory monitoring systems provide a live view of production machines, offering insights into their current status and performance. This real-time data is essential for quick decision-making and immediate response to any issues.
- Intuitive data visualization: The status of machines and key performance indicators (KPIs) are presented in an intuitive, color-coded format. This makes it easier for teams to understand and manage the overall state of the factory.
- Historical data analysis: These systems allow for the monitoring of factory performance over extended periods, like the previous 1 to 24 hours. This historical perspective is crucial for identifying trends and making long-term improvements.
- Centralized management: For businesses with multiple factories, factory monitoring systems enable the tracking and management of all locations in one place, enhancing overall operational oversight.
- Performance display: By displaying factory performance data on large screens, these systems foster a culture of transparency and continuous improvement among teams and visitors.
Factory monitoring systems are the central core that coordinates and monitors the interconnected elements that are revolutionizing production processes and factory management.
Forging Ahead: The Future of Smart Manufacturing
The manufacturing sector has always been at the forefront of technological innovation. The rapid uptake of the latest advanced technologies is a testament to this trait. Thanks to AI, IoT, cloud computing and advanced factory monitoring systems the factory floor is now more efficient, cost-effective, safer, and more sustainable.
More Stories
DuPont materials science advances next generation of EV batteries at The Battery Show
How a Truck Driver Can Avoid Mistakes That Lead to Truck Accidents
Car Crash Types Explained: From Rear-End to Head-On Collisions