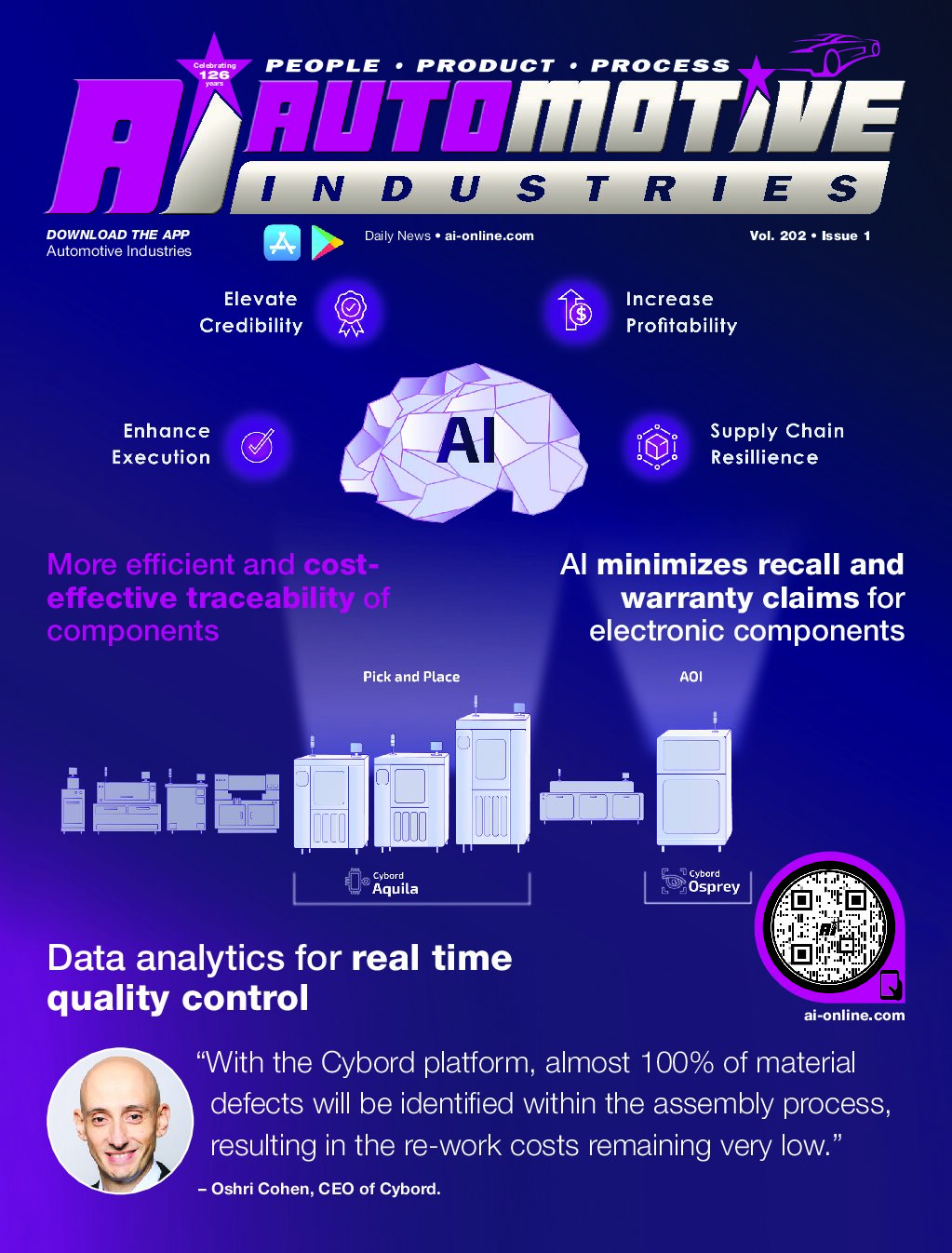
The global supply chain has been experiencing significant challenges in maintaining product quality in recent years.
These issues have resulted in unprecedented electronic component waste, which has impacted manufacturers, suppliers, and consumers alike. The problems stem from a range of factors, including inadequate quality control, lack of oversight, and insufficient communication between different players in the supply chain.
Companies like Cybord are helping Tier 1s and OEMs to tackle these challenges.
The challenges of supply chain quality
One of the most significant challenges in maintaining supply chain quality is the lack of oversight across the manufacturing process. Electronic components are produced by suppliers across the world, often in multiple locations, before being shipped to the final assembly line.
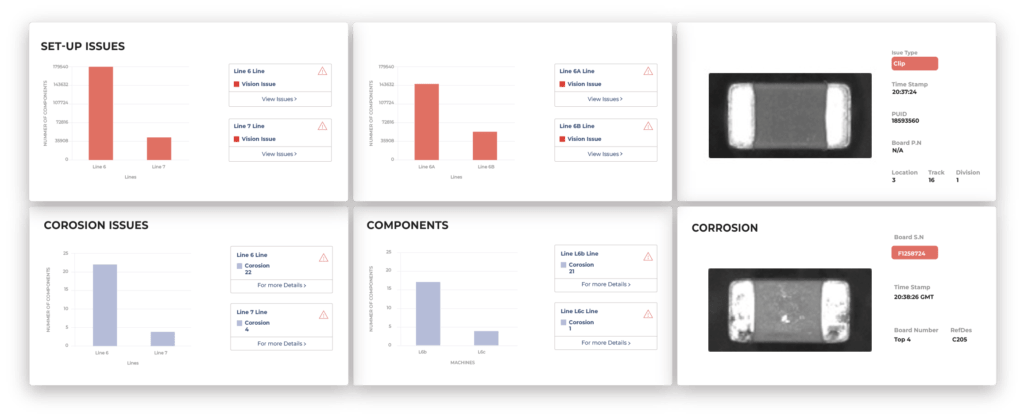
This can result in quality issues that may not be apparent until the final product is assembled. If these issues are not caught early, they can result in significant waste, recalls, and warranty claims.
Another challenge is the lack of communication between different players in the supply chain. Suppliers and manufacturers may not have a clear understanding of the product specifications or requirements, which can lead to confusion and errors in the production process.
The use of different suppliers for the same components can also result in inconsistencies in product quality.
Finally, quality control measures may not be in place or adequately enforced at every stage of the production process. As a result, defective components may pass through quality checks undetected, resulting in downstream failures and significant waste.
In conversation with Automotive Industries is Oshri Cohen, the CEO of Cybord, a leading inline visual-AI platform which provides a more comprehensive view of production lines. It ensures the assembled electronic components’ authenticity and quality, and provides the highest level of traceability.
Cohen is an executive officer with 20+ years of management experience in operations, engineering, and supply chain in multinational high-tech companies. Before joining Cybord, Cohen headed Supply Chain at Nvidia Networks. Prior to that he led global procurement and logistics at Mellanox (acquired by Nvidia).
Cohen holds a BSc. in Industrial Engineering from Ruppin academic Centre and MSc in system Engineering from Technion University.
Under his leadership, Cybord has experienced significant growth, expanded its customer base and developed advanced solutions to mitigate the risks of field failures and counterfeit electronic components.
Automotive Industries (AI) asked Cohen how Cybord’s software utilizes visual analysis techniques to detect defects and counterfeits in components.
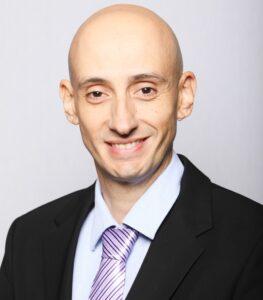
Cohen: By relying on AI and big data analytics, our solution looks at both the top and bottom of components and analyzes visual data and production metadata to ensure authenticity, quality, reliability and visual traceability of all electronic components.
The platform is installed onto a dedicated server within the factory. It then collects all images from existing surface-mount technology machines (SMT) and automated optical inspection (AOI) machines. This development differentiates us from others.
Our platform seamlessly connects to component assembly machines, allowing near real-time inspection of 100% of components a fraction of a second before the assembly process onto the boards is complete.
By examining all components within the assembly process, Cybord’s solution empowers customers to identify and eliminate faulty or counterfeit components, which in turn reduces costs by minimizing the scrap/rework rate and providing smooth and efficient product delivery times.
The platform works with standard assembly machines, making it compatible with virtually every assembly line in the world.
AI: How can the platform save time and costs for automotive manufacturers?
Cohen: We understood that introducing additional hardware to the manufacturing and inspection process comes with limitations and can lead to delays in delivery, and logistics, especially for budget-conscious companies.
Instead, we chose to tap into the world of AI and big data to find a cost-effective, and scalable solution to the growing issue of component quality control. Cybord’s platform is a software-only solution that doesn’t require any additional capital investments or modifications to production line layouts to deliver quality assurance.
When we identify a defective component while the board is still on the assembly line, the cost of fixing it is only 1x the price of the component. If this board progresses through the integration process, it will cost 100x more to fix it.
The worst-case scenario is one in which the board with the defective component falls through the cracks and enters the market. In this case, the customer will need to pay 1000x the amount to recall it and produce a replacement, which will not generate any new revenue for this customer.
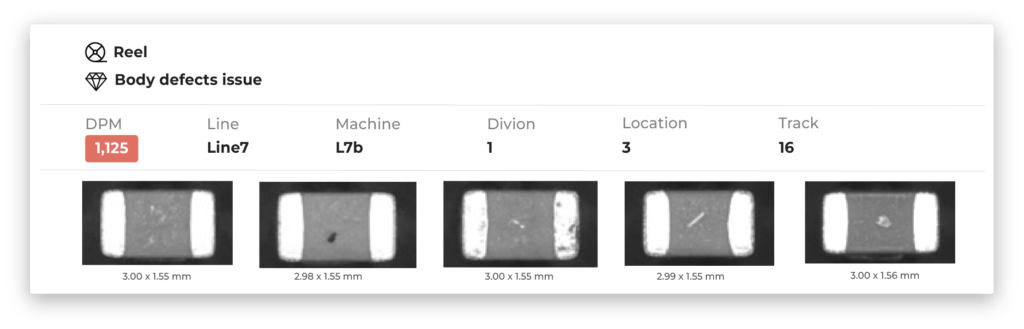
With the Cybord platform, almost 100% of material defects will be identified within the assembly process, resulting in the re-work costs remaining very low.
Another benefit this platform provides is the capability to identify an epidemic event before it is even assembled on the product. The Cybord platform reviews the defect rate of every component reel and in the case that it identifies a reoccurring event, the platform will indicate that the whole reel should be replaced to avoid epidemic failure.
With this strong feature, the re-work cost becomes zero as there will be no assembly of bad components.
AI: Could you elaborate on the level of precision and accuracy that Cybord’s software achieves in identifying defects or signs of counterfeit components? Are there any specific examples or case studies that demonstrate its capabilities?
Cohen: Statistics have shown that approximately 90% of component failures are associated with visual indications on the component itself. Our technology allows OEMs and OCMs to verify that each component is sourced from a reliable source, and that the homogeneity level within the same reel is high, and free from any visual defects, oxidation, or mold evidence.
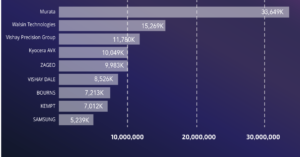
By doing so, our platform is able to provide complete inspection of 100% of the components that go onto a PCBA (Printed Circuit Board Assembly) and deliver the surgical traceability needed in a zero-trust supply chain environment.
For example, when we installed Cybord’s platform on a Tier 1 automotive company, the lab results of this case study confirmed that the components which Cybord indicated as faulty were significantly defective and should have been disqualified.
The company reported significantly improved product reliability and productivity with surgical precision and a reduction in disruptions within the manufacturing process, all of which ensure higher yields and better bottom lines.
AI: What about tracing components through the manufacturing process?
Cohen: Today, the most widespread standard for traceability is “batch traceability.” While batch traceability does track the production lot, serial number, and exact board placement for components, it fails to analyze the individual components themselves, thus jeopardizing the quality of the end products.
Current traceability standards, while a good start, still assume that all components within a reel are exactly the same, when in reality we know this is not the case.
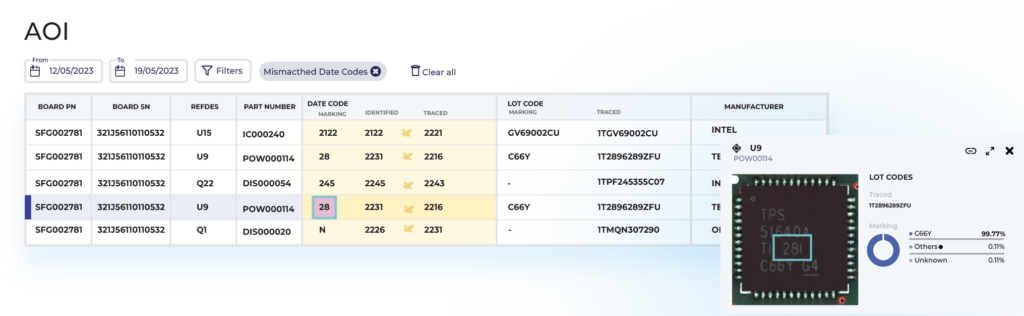
Our AI-powered visual technology can enable this heightened level of traceability, offering a more efficient and cost-effective solution.
Our solution can rapidly analyze every component on every board for authenticity and component integrity, allowing manufacturers to pinpoint any problematic component and conduct rapid, surgical recalls on an individual basis with minimal disruption to the manufacturing process.
The fact that our traceability is based on visual evidence makes it significantly stronger than the rest of the existing solutions on the market today, as Cybord’s system enables the customer to investigate the failure’s root cause before products are recalled from the field.
This significantly minimizes the population of products that require recall.
AI: What modifications are needed to integrate your system onto existing lines?
Cohen: Our software-only solution was built specifically to integrate with pre-existing SMT and AOI machines and processes.
Cybord is collaborating with the biggest machine manufacturers in the world to receive the components’ images as part of the process without causing any
delays or modifications to the existing assembly lines.
Cybord then feeds back the relevant analysis results in real-time, and in parallel analyzes many important statistics that can lead the customer to make informed decisions based on the actual material data accurately collected from the field.
AI: Are there any limitations or considerations to keep in mind when scaling up the software’s usage?
Cohen: The beauty of the Cybord platform is that it inherently enables scalability. Cybord’s solution is applicable for use across almost all verticals, and with companies of all sizes.
Everyone who builds and integrates electronic boards into their products needs such a system, but the platform most specifically addresses the needs of OEMs and EMSs.
Our technology is currently utilized by Tier 1 OEMs, Tier 1 automotive manufacturers, defense contractors, health tech industries, and DataCom companies.
The platform becomes stronger, sharper and faster as it ingests more components into its database.
Since the platform is based on AI deep neural networks analysis and not on machine vision, it is designed to scale-up.
More Stories
Venti Technologies Wins Multiple Pinnacle Awards for Innovation and Achievement in Technology
Launch of AltaScient.ai: New horizons for Risk and Sustainability Analytics
Expert Tips on Detailing a Car