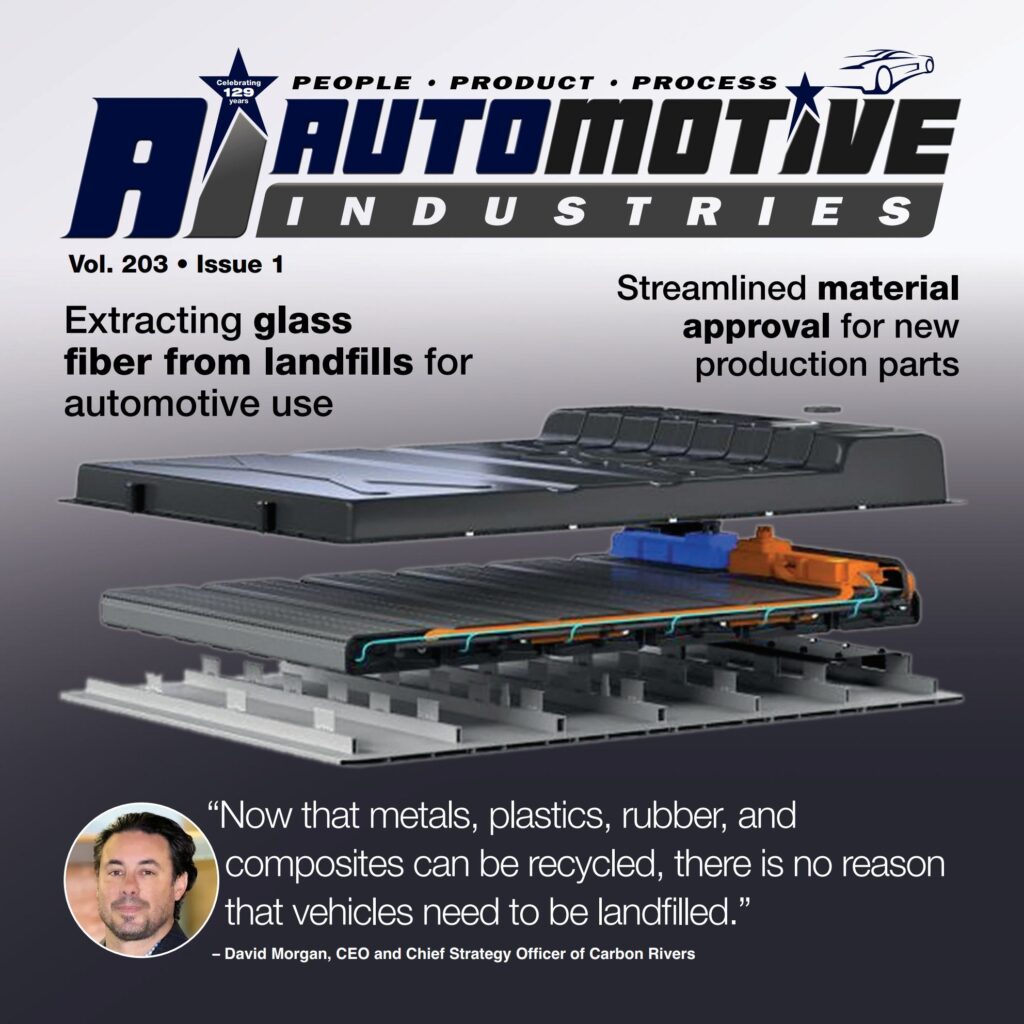
Carbon Rivers develops perpetual lifecycle for glass fiber and graphite
Electric vehicles and renewable energy producers such wind turbines are lauded for their environmental benefits, but there’s a significant concern about what happens to the components in the vehicles at the end of their life cycle.
Automotive Industries (AI) asked David Morgan, CEO and Chief Strategy Officer of Carbon Rivers, to share the company’s reclamation technology.
Morgan: Carbon Rivers originally collaborated with the US Department of Energy and the University of Tennessee to evaluate glass fiber recovery from end-of-life composites.
This original project, funded under an SBIR Phase I, II, and III commercial, was quite successful and then matured into the commercialization of the technology along with the capability of recovering glass fiber from post-industrial thermoset and thermoplastics as well.
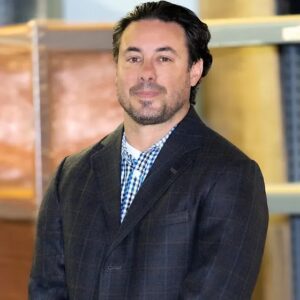
It is simply a three-part GF recovery technology where we mechanically reduce the composite feedstock (a carbon negative LCA process), then crack the polymer in order to separate out the GF from the light and heavy hydrocarbons (also a carbon negative LCA process), and finally chemically resizing the cleaned glass fiber for mechanicals to be used in various intermediates like thermoplastics and non-woven mats.
The process has been tremendously refined since its inception, but it is a remarkable achievement to recover glass fiber that is clean and mechanically intact for next life cycle manufacturing, and we even extract the condensed heavy hydrocarbons for a renewable oil that can be fractionated off the tower for various offtake products.
We call the rGF recovery process a perpetual life cycle since even the rGF fines can go back into remelt for a continuous filament.
AI: How does Carbon Rivers’ technology address the environmental impact of end-of-life electric vehicles?
Morgan: Our contribution to the automotive industry is not just on the post-consumer side but also the post-industrial side as well.
We can extract the glass fiber out from the manufacturer or the landfill.
We can process any composite thermoset or thermoplastic, so this allows tremendous opportunity for upstream waste solutions as well rGF incorporation back into the downstream supply chain.
At least for the composite piece, landfill is unnecessary for PI and PC automotive industry.
Now that metals, plastics, rubber, and composites can be recycled, there is no reason that vehicles need to be landfilled.
AI: Could you share how and where Carbon Rivers is collaborating with its customers to advance sustainable practices in the automotive sector.
Morgan: Carbon Rivers works closely with multiple automotive OEMs and their Tier suppliers for various rGF product development applications.
The production part approval process (PPAP) takes the better part of a year.
Carbon Rivers can help streamline that material approval process by first doing the mechanical and performance testing in house, and then providing the data and samples to our automotive partners.
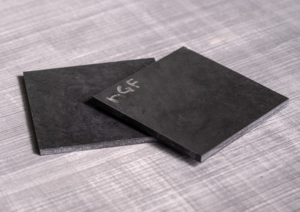
We all know that the EU has the directive of 25% recovered materials in automotive production by 2030. Although that is quite the lofty goal, CR can certainly help in that endeavor by providing multiple approved rGF intermediates into the supply chain.
AI: The conversion of a Mazda RX-8 from a petrol-driven car to a fully electric-powered supercar, using parts from recycled wind turbine blades is an impressive feat. What were the main challenges and learnings?
Morgan: Carbon Rivers has a crack engineering team, and maybe the most advantageous skill set is their inability to hear the phrase “not possible”.
The vehicle modification was comprehensive, but the re-wiring and installation of the Tesla P100D and battery system was not the most difficult feat – it was the integration of the charging system with the battery management system.
Our team figured out various hacks and work arounds to basically engineer a hot-sway EV supercar. When I say supercar, I mean it. At 600hp and 745 ft lb torque with a 0-60 around 2.2 seconds we require waivers to drive the EV RX8.
Regarding sustainable, recovered materials, the back bumper is noticeably not stock.
Rather, it is rGF from a wind blade infused into a pristine graphene resin layup for a significantly enhanced modulus and tensile bumper. We even have a pristine graphene automotive coating on the EV supercar that resists UV and corrosion.
If we end up winning the 24 Hours of Lemons Endurance Race, it would certainly be a world record for the first time an EV has beaten petrol vehicles in an endurance race.
Think of it as LeMans, just less sexy.
AI: Carbon Rivers also recovers graphite from end-of-life EV batteries. What challenges have you encountered in implementing this technology?
Morgan: Since we already manufacture pristine graphene from raw graphite, it was not too difficult to adapt the process to recovering high-quality pristine graphene from battery-quality graphite.
Since graphite is a critical material, it was important that we look into this process.
It has been successful, and we have a couple large EV battery groups that will supply our graphite so we can process the PG back into next-life cycle battery systems.
AI: Your company also provides ultra-lightweight, flexible, and UV-resistant ballistic material solutions for law enforcement and military use. What applications do you see for these materials in the automotive industry?
Morgan: At first glance, a pristine graphene gel-spun UHMWPE fabric might not appear related to the aforementioned technologies.
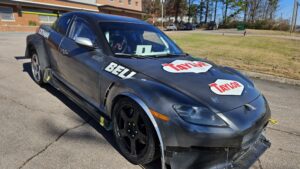
Nevertheless, CR specializes in advanced material commercialization.
The polyethylene graphene infused fabric (PEGI) is simply used for defense armor systems, hardening of architectural panels for schools, and other protective applications.
The automotive industry is using the fabric in skid plates for thermal mitigation and durability by protecting EV batteries from road debris.
AI: Carbon Rivers utilizes graphene nanoflakes in specialty coatings with various applications, from UV resistance to anti-viral properties. Can you share examples of how these coatings can be applied in the automotive sector, and what advantages they offer over traditional coatings?
Morgan: Just like we have used our PG automotive coating on the EV RX8 for UV resistance, hydrophobicity, anti-corrosion, and other performance enhancements, I think it would be suitable to coat the undercarriage to protect transportation, heavy equipment, and offroad vehicles against corrosion from weather and salt.
Of course, with these niche performance enhancements the PG anti-abrasion coating fits nicely with certain customer segments.
Even a PG clear coat would have a car look like it just came off the line ten years later when it was being sold.
AI: Carbon Rivers is currently seeking funding with its ANC partner to scale up glass fiber recovery for composite manufacturers. What are the key milestones and goals, and how do you envision it impacting the broader automotive and composite industries?
Morgan: Carbon Rivers is currently in partnership with global sustainability funding groups to scale up these circular economy and sustainable next-generation technologies for other regions of the world.
The manufacturing and labor creation that contribute to projects that are more ecological and humanitarian in nature (we have not even discussed PG sustainable marine coatings and concrete).
They are just the beginning for transforming communities, supply chains, and even energy grid systems for cleaner, more efficient economies.
We have advanced material technologies that are being deployed into global regions for elevating the quality of life and sustainable manufacturing that directly impact a community and family for the type of life they should have today, not tomorrow.
AI: Beyond wind turbine blades, Carbon Rivers aims to provide glass fiber solutions for a variety of industries, including automotive, aerospace, marine, and construction. How do you foresee the role of glass fiber recycling evolving?
Morgan: Carbon Rivers wants to achieve two initiatives with respect to a rGF circular economy.
First, we would want to have a domestic, regional intake and offtake for recovered GF intermediates going back into these industry supply chains.
We all know that transportation and logistics contribute to not only the overall costs for a waste solution
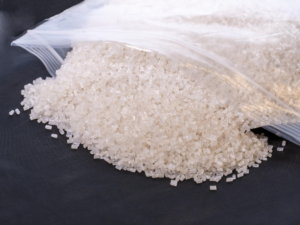
and supply chain project, but also the embodied energy and greenhouse gas required to make these sustainable supply chains happen.
Carbon Rivers has a GF recovery commercial technology that is itself carbon negative, but how can we decrease the footprint for the overall supply chain?
We see part of the solution as having domestic, regional facilities.
For example, taking in post-industrial and post-consumer composites in a Texas site, processing and recovering the GF, and then sending that back into the downstream supply chain within Texas manufacturing would be a novel approach to this industry challenge.
And in this supply chain for the composite industry, rGF intermediates will only supplement and not replace virgin production.
Second, our intention is to make a dent (albeit a noticeable, sustainable dent) in the industry so that a wind blade is processed into a Tier supplied sheet molded compound (SMC) for automotive manufacturing in Texas, as it were from grave to cradle.
This includes rGF non-wovens, SMC, BMC, thermoplastics, additive manufacturing, and other composite materials for the industry supply chain. rGF can ultimately be integral to any composite supply chain.
Interestingly, one of the biggest obstacles is market adoption.
One might be surprised at this, but for example in the wind industry, which is largely subsidized in the US market, budgets and testing are not allocated to new materials and product development.
This is unfortunate, especially when the rGF product has the same production specs, mechanicals, and performance as virgin product.
The other issue is for businesses to make proper business cases without the need for incentives and credits.
Currently the market is if it is sustainable, then it is profitable through credits. The inverse needs to be the case where if it is profitable, then it is sustainable.
More Stories
MESSRING completes new crash test facility for Mahindra in India
ROHM Develops an Ultra-Compact MOSFET Featuring Industry-Leading* Low ON-Resistance Ideal for Fast Charging Applications
More than 30 of the top 50 global suppliers have production facilities in Turkey