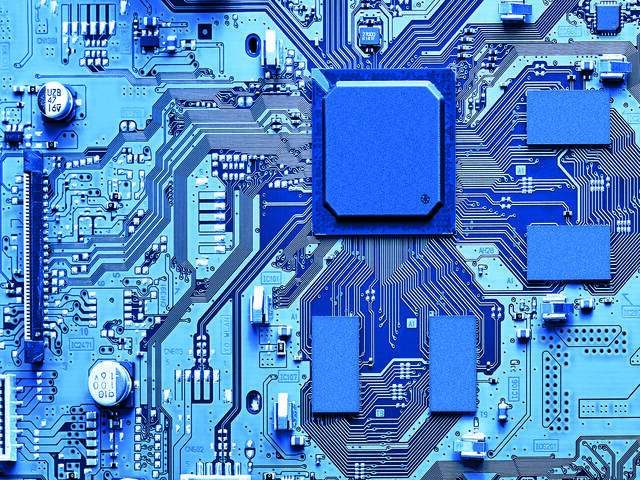
Automotive suppliers such as Bostik and its parent company Arkema have adopted ambitious programs to reduce the impact of their operations and products on the environment.
Automotive Industries (AI) asked Benoît Perrier, Global Automotive Director at Bostik, how 40 years of working directly with OEMs and Tiers has enabled Bostik to remain at the forefront of renewable technology.
Perrier: Working with an OEM always challenges our engineers to be more innovative. The OEM focus is on performance, quality and cost.
The biggest challenge lies with mature technologies, which have to be further refined and improved in order to have better performance and better cars.
Added to this is the megatrend of sustainability, which has resulted in us stepping up the development of technologies which have lower environmental impact.
This has resulted in the development of SAF&FIT® and Pliogrip®.
Combining, our MMA structural adhesives SAF&FIT® with Elium® , a thermoplastic resin for composite parts, facilitates recyclability (for example in the wind or boat industries).
Pliogrip® is a two-part polyurethane adhesive technology that provides outstanding long term durable adhesion to glass and carbon fiber thermosets, many thermoplastics, and coated metals, with minimum surface preparation.
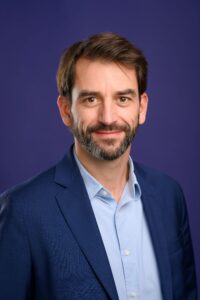
We work with the Tiers to help the team find a solution for their product and to fix any issues which have been identified, as well as meet the specifications set by the OEMs.
At the same time, we are developing technologies in the mid to long term to meet future needs.
AI: Is your full portfolio of automotive adhesive solutions available globally?
Perrier: This is one of the most important aspects of a solution. Just having the technology is only part of the solution.
The second part is being able to service the customer.
We ensure that we have our products and technical support close to our customers throughout the world.
We have R&D centers worldwide, in the US, in Europe, and in multiple locations in Asia – including China, Japan, South-Korea, Asia, Southeast Asia, and Australia.
This helps customers meet local legislative requirements.
While not every technology is manufactured in every place, we are able to supply our technologies worldwide, because when we start a business with a worldwide company like an OEM, they want us to be able to deliver to every plant.
AI: Do your high-performance technologies address even the most stringent assembly needs?
Perrier: Being part of the French-based Arkema group since 2015 has provided Bostik with additional support in the form of upstream R&D, as well as the integration of material.
Building on its unique innovative chemistry expertise, Arkema creates pioneering and more sustainable materials solutions for customers from a broad range of markets, with particular focus on new energies; natural resources management; home efficiency; lightweight materials; and consumer electronics.
Thanks to our day-to-day working with Arkema we have been able to achieve new standards of performance of our products.
AI: Does Arkema upstream integration allow you to predict change sooner and build solutions faster?
Perrier: We are guided by the future requirements of the end user.
Arkema is very closely connected with the major OEMs because they supply materials such as biobased polymers for vehicle batteries.
The requirements for the new generation of materials are fed through to us.
We are also guided by the future requirements introduced by pending legislation.
AI: How do you contribute to extending the lifespan of batteries?
Perrier: The main challenges are performance or range, and safety.
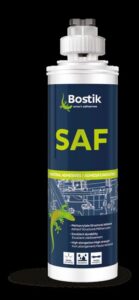
Our solutions focus on providing a product which performs as required during its lifespan and is cost-effective to recycle at the end of its life cycle.
Where necessary we make acquisitions in order to meet the requirements of customers.
In May 2023 Arkema acquired Polytec PT, which specializes in adhesives for batteries and electronics.
Polytec PT has expertise in thermal interface materials which are key to enable fast charging of the battery and efficient dissipation of the heat, which is one of the biggest problems.
Our solution is now highly efficient toward competition.
We are also working on structural adhesives to ensure the battery has the right amount of stiffness to ensure safety.
Over the next few months, we expect to be able to announce a breakthrough in the development of recyclable battery materials.
AI: What solutions do you offer for Hydrogen / Fuel Cell?
Perrier: It is estimated that by 2030, we will have two million vehicles, passenger cars or trucks and busses running on hydrogen in one form or another.
We need to determine whether or how a hydrogen fuel cell is compatible with the battery chassis of an electric vehicle. Both have to store energy in a battery, but the technology is in a state of flux.
We are working with the industry to find solutions.
Arkema and Bostik have specialized teams dealing with hydrogen fuel cell technology. One of the focus areas is a lightweight composite hydrogen tank.
We are working with partners in the sector to bond a protective layer for the tank, as well as the liner bonding.
The tank has to withstand intense temperatures and pressures when charging and discharging hydrogen, which puts tremendous strain on the bonds.
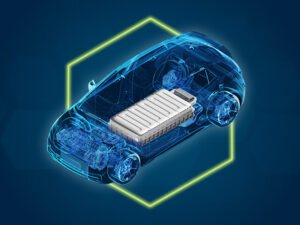
Arkema has anticipated this shift, developing materials and solutions that are already contributing to improving the industry’s performance and business model.
AI: What new technologies did you introduce at JEC 2024?
Perrier:
Bostik revealed its adhesive solutions to bond and repair composite parts, with a focus on its structural adhesives MMA SAF&FIT and Pliogrip™ range of 2K polyurethane and epoxy structural adhesives, Born2Bond™ Instant Adhesives, and SMP sealants.
Bostik presented our low-profile additives (LPA) to improve the intrinsic properties of composite materials, such as their chemical, thermal and mechanical resistance in sheet molding and bulk molding Compound (SMC, BMC).
AI: What’s next for Bostik?
Perrier: Over the past five years we have grown through organic business development and a number of acquisitions, and the journey continues.
Our objective is to become the true leader in the supply of more sustainable technologies for mobility.
The vision is to enable our customers and the end user to enjoy safer and more sustainable lives.
We will continue to innovate thanks to our people. Arkema has the technology and products, but it is the people who deliver.
Our mission is to attract and retain top industry talent.
More Stories
MESSRING completes new crash test facility for Mahindra in India
ROHM Develops an Ultra-Compact MOSFET Featuring Industry-Leading* Low ON-Resistance Ideal for Fast Charging Applications
More than 30 of the top 50 global suppliers have production facilities in Turkey