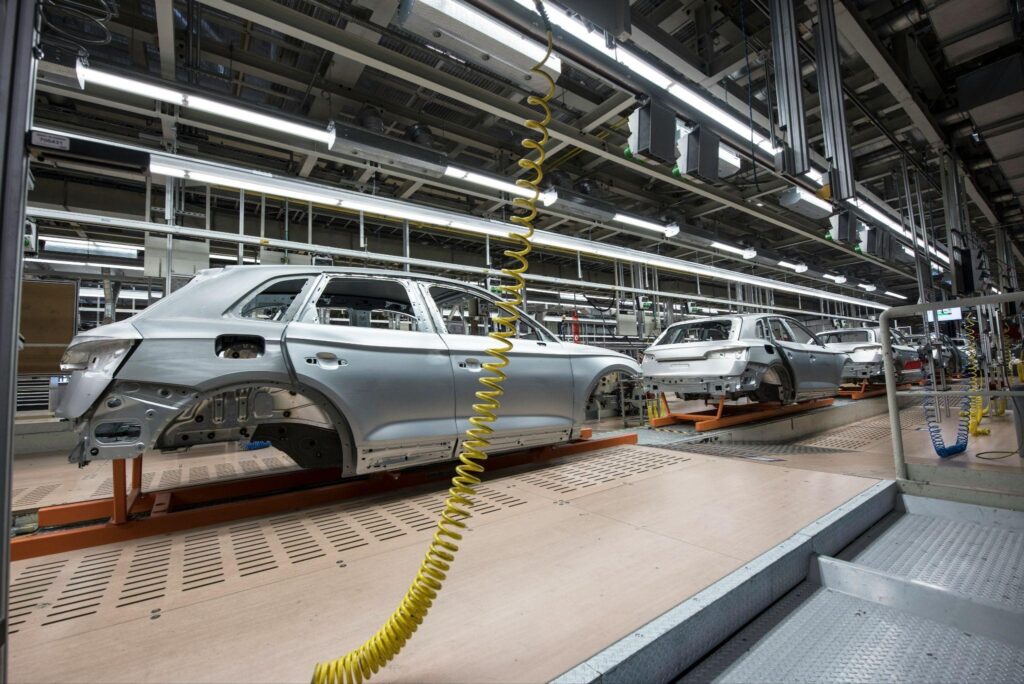
In today’s fast-paced automotive industry, the demand for precision, efficiency, and innovation is at an all-time high. Servo motors and drives have become indispensable in meeting these demands, transforming how vehicles are manufactured. These advanced technologies not only enhance the precision and speed of production but also play a critical role in automation, reliability, and cost-effectiveness. This article delves into the pivotal role that servo motors and drives play in modern automotive manufacturing, exploring their applications, advantages, and future trends.
What is the Role of Servo Motors in Automotive Manufacturing?
Servo motors are key components in automotive manufacturing, offering unparalleled precision and efficiency. These motors are designed to provide exact control of angular or linear position, velocity, and acceleration, which is essential for tasks that require high accuracy, such as assembling vehicle components or operating robotic arms. In this context, servo motors help reduce errors and improve overall productivity, making them ideal for use in mass production environments. The precision they offer allows manufacturers to meet the stringent quality standards required in automotive production, ensuring that each part is manufactured with consistency.
How Do Servo Drives Enhance Manufacturing Automation?
Servo motor drives are equally critical in the automation of manufacturing processes. They serve as the control system that interprets commands from the CNC or PLC system and converts them into signals that drive the motor, ensuring accurate and efficient movement.
Servo drives enhance automation by providing:
- Real-time feedback: Continuous monitoring and adjustments to ensure optimal performance.
- Energy efficiency: Servo drives use only the necessary amount of power, reducing energy consumption.
- Increased productivity: By reducing setup times and increasing speed, servo drives boost production output.
- Precision control: Servo drives provide high-resolution control of motor speed and position, ensuring that every movement is accurate and repeatable.
Key Features of Advanced Servo Drives
- Real-time feedback: Immediate adjustment of motor performance based on real-time data.
- Precision control: Ensures the accuracy of positioning, which is critical for precision tasks in automotive manufacturing.
- Energy efficiency: Optimized energy consumption leads to cost savings in high-output environments.
- Built-in diagnostics: Advanced systems that offer troubleshooting support and error prevention.
Comparing Servo Drives and Traditional Systems
While traditional motor systems still have their place in certain areas, servo drives are often a better choice for modern automotive manufacturing. Here are the key differences:
Pros of Servo Drives:
- High precision and accuracy.
- Real-time feedback for adjustments.
- Energy efficiency.
Cons of Traditional Systems:
- Limited precision.
- Higher energy consumption.
- Less adaptability to complex automation needs.
What Are the Different Types of Servo Motors Used in Automotive Manufacturing?
Servo motors come in various types, each suited to specific applications in automotive manufacturing. Understanding the differences between these motors is essential for choosing the right one for a particular task.
AC Servo Motors
AC servo motors are commonly used in applications requiring high torque at low speeds. Their ability to handle sudden load changes and their durability make them ideal for heavy-duty automotive manufacturing tasks like stamping or molding.
DC Servo Motors
DC servo motors are known for their simplicity and ease of control. They offer excellent performance in applications where precise speed control is essential, such as in conveyor systems and robotic applications.
Brushless Servo Motors
Brushless servo motors combine high performance with low maintenance. They are widely used in automotive manufacturing for tasks that require high precision and reliability, such as welding and assembly lines.
Integration of Servo Motors with Robotic Systems
The integration of servo motors into robotic systems has revolutionized automotive manufacturing. These motors provide the fine control necessary to operate robotic arms that assemble, weld, or paint vehicle parts with extreme precision. As robots become more advanced, servo motors allow for more complex, delicate movements, improving manufacturing quality and speed.
Case Studies of Robotic Automation Using Servo Motors
Leading automotive manufacturers such as Tesla and BMW have implemented servo motors in their robotic systems to enhance production. These systems not only increase production speed but also improve the overall quality of the vehicles produced by reducing human error and ensuring consistency in tasks such as welding and assembly.
How Are Servo Drives and Motors Optimized for Safety and Reliability?
In an industry where precision and safety are paramount, servo motors and drives come equipped with multiple safety features to protect both the equipment and operators.
- Overload protection: Prevents the system from overheating.
- Emergency stop functions: Immediate shutdown in case of malfunction.
- Feedback systems: Continuous monitoring of performance to detect and correct issues before they become problems.
- Fault diagnostics: Systems are equipped with self-diagnostic tools to identify potential issues before they cause significant disruptions.
Safety Protocols and Features in Servo Systems
- Emergency stop: Immediate halt to the motor in case of an emergency.
- Overload protection: Prevents system damage due to excessive load or overheating.
- Built-in diagnostics: Monitors motor performance to prevent failures.
- Motion control limits: Ensures the motor operates within predefined safety parameters.
What Are the Latest Innovations in Servo Technology?
The servo technology landscape is continuously evolving, with innovations aimed at increasing energy efficiency, precision, and integration capabilities.
Energy Efficiency Improvements
Manufacturers are now developing servo motors that consume less energy while maintaining or even improving performance levels. This reduces operational costs and minimizes the environmental impact of automotive production.
Advances in Precision and Speed
Newer servo motors and drives are capable of even finer precision and faster movements, which further enhances their application in automotive manufacturing. These improvements are particularly useful in processes like 3D printing and robotic assembly, where speed and accuracy are critical.
Step-by-Step Guide: Installing and Configuring a Servo Drive System
Proper installation and configuration are crucial for maximizing the efficiency of servo systems. Below is a guide to ensure optimal setup:
- Mount the servo motor securely.
- Connect the power supply and feedback cables.
- Configure the drive settings according to the manufacturer’s guidelines.
- Perform a calibration test to ensure the motor operates correctly.
- Adjust parameters such as speed and torque as needed.
Troubleshooting Common Issues with Servo Systems
- Overheating: Check for overloads and adjust cooling systems.
- Noise: Ensure proper lubrication and check for mechanical misalignments.
- Inconsistent movement: Recalibrate the motor and check feedback systems.
- Drive errors: Consult diagnostic tools to identify and resolve drive issues.
How to Select the Right Servo Motor and Drive for Your Automotive Manufacturing Needs?
Selecting the right servo system is critical to ensuring the efficiency and reliability of your manufacturing process.
Assessing Your Manufacturing Requirements
- Speed requirements: Choose a motor that matches your production speed needs.
- Torque demands: Ensure the motor can handle the necessary torque.
- Precision levels: Select a system that provides the required precision for your application.
- Energy consumption: Consider the energy efficiency of the system.
Economic Impact of Servo Motors and Drives on Automotive Manufacturing
Servo motors and drives not only enhance production capabilities but also provide long-term financial benefits by reducing energy consumption and improving operational efficiency.
Cost Analysis of Servo Systems vs. Traditional Motor Systems
- Initial investment: Servo systems may have a higher upfront cost but provide long-term savings through reduced energy consumption.
- Maintenance costs: Servo systems require less maintenance compared to traditional motors, lowering downtime and associated costs.
- Energy savings: With optimized energy use, servo motors can significantly reduce electricity bills over time.
Future Trends in Servo Technology and Automotive Manufacturing
The future of servo technology in automotive manufacturing looks promising, with advancements in AI, machine learning, and IoT expected to play a significant role. Servo motors and drives will likely become even more efficient, offering better integration with smart manufacturing systems and further enhancing precision and productivity.
Conclusion
Servo motors and drives are crucial to the modern automotive manufacturing landscape. Their ability to enhance precision, improve efficiency, and integrate seamlessly with automated systems makes them indispensable. As technology continues to advance, servo motors and drives will undoubtedly play an even more significant role in shaping the future of automotive production.
More Stories
DuPont materials science advances next generation of EV batteries at The Battery Show
How a Truck Driver Can Avoid Mistakes That Lead to Truck Accidents
Car Crash Types Explained: From Rear-End to Head-On Collisions